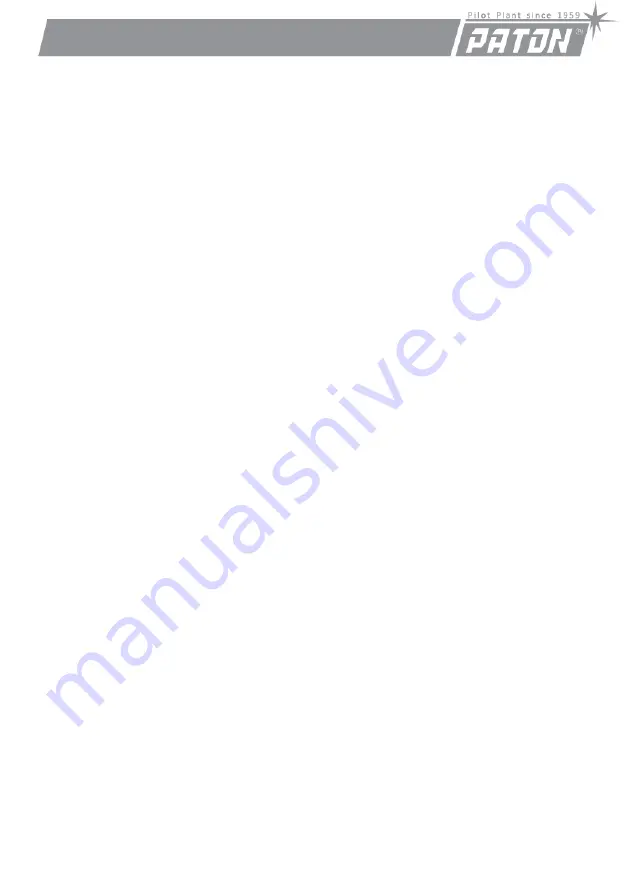
PATON
StandardMIG
MMA/TIG/MIG/MAG
-20 -
‐ connect the power current plug of the wire‐feeding machine of the source socket
А “+”
;
‐ connect and fasten
against the stop
the semiautomatic welding torch to
socket
13
;
‐ install a pressure reducer on the gas bottle with shielding gas “СО2”, “Ar”, or
“Ar+CO2”;
‐ connect gas hose to the pressure reducer of the gas bottle and fitting
16
on the
rear panel;
‐ open the cock of the gas bottle and check it for tightness;
‐ connect the mains plug of the source to the supply mains;
‐ set power switch
14
on the rear panel of the source to position “I”;
‐ set the semiautomatic MIG/MAG welding mode by pressing the button
6
; the
modes switch over end‐around;
- if the digital display of the wire-feeding machine
9
does not turn on, check the
rear panel fuse
15
(4A);
‐ use buttons
1
to set the required welding voltage;
- install the coil with the wire of the required diameter;
- lift up the pressure roller arm;
- lead the free end of the wire through the input channel into the welding torch;
- lower and clamp the welding wire between the rollers; the pressing force of the
rollers is written on a plastic handle; if there is no experience, then initially set to
the middle position (this is about 3);
- using buttons
12
, set the required wire feed speed;
- use button
8
to pull the wire through the entire channel and adjust the final
pressing force of the rollers according to the recommendations for semiautomatic
welding; at the same time, pay special attention to the force of clamping the coil
brake: the coil should be MINIMALLY-REQUIRED and easily rotated, but
spontaneous unwinding should not be observed;
‐ if necessary, additional functions of welding process can be adjusted – see a
changeover sequence in Clause 6.1.
Remember to supply shielding gas. In order to check its availability, a
button
11
is provided in the torch channel, at the moment of pressing which the
wire does not feed. If you are new to welding and do not have experience in
establishing optimum pressure for welding of a specific work piece, you can for the
first time set gas pressure above the optimum value ~0.2MPa: this will have a
minor effect on the process, only increase consumption of shielding gas. However,
follow general recommendations on semiautomatic welding in the future to save
gas. Start also with an average position of wire feeding speed controller on the
feeding machine (~ 6.0...8.0m/min.) and average source voltage (~19V) for any
Содержание StandardMIG-160
Страница 1: ......
Страница 2: ...PATON StandardMIG MMA TIG MIG MAG 2 ...
Страница 7: ... 7 PATON StandardMIG MMA TIG MIG MAG ...