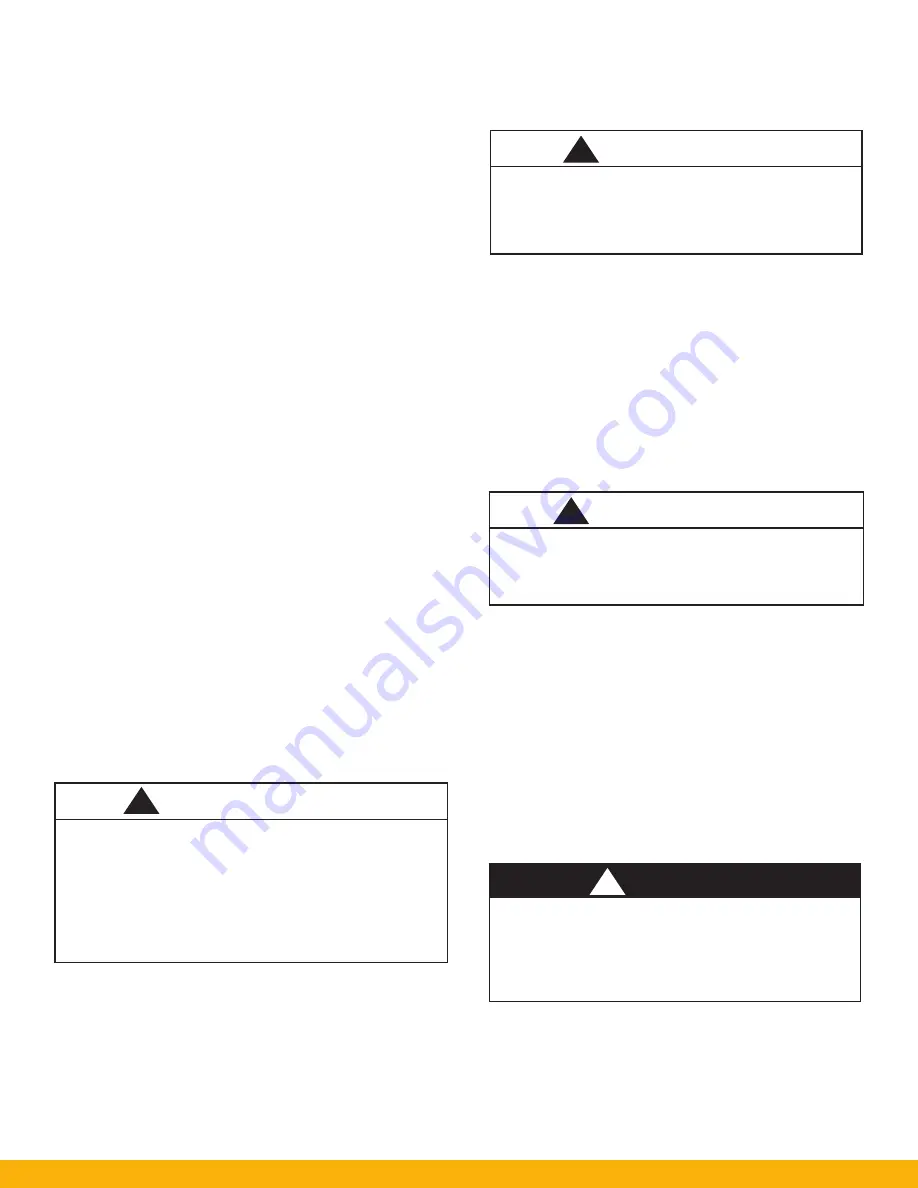
25
Replacement cartridge filters should be ordered when the
differential pressure is consistently above 5” w.g. (127 mmAq
or system airflow is inadequate and won’t significantly recover
with off-line (no fan pulse) cleaning. To order filters, contact Parker
at 1-800-343-4048.
TO REPLACE CARTRIDGE FILTERS
1. Read and follow caution instructions in box above before
servicing your unit. Start with the top row of QuickSeal doors.
(Figure 17)
2. Tap the metal surface of each filter access door to remove col-
lected particles from the inner door gasket. Pull the QuickSeal
door handle away from the dust collector until the handle makes
a 90° angle with the door cover. The filter access door is now
in an unlatched position. Lift the QuickSeal filter access door
upward until the door rods clear the side support brackets. Pull
the door away from the dust collector. Tilt the door cover away
from the dust collector once free from the support brackets to
trap any dust on the inside of the filter access door. Dispose
of dust into a suitable container. Place filter access door in a
safe place.
3. Move filter from side to side to break the gasket seal between
filter-to-filter-to-tubesheet locations. Rotate the filter 180° to
allow the dust on top of the cartridge filter to fall into the dust
collector hopper.
4. Slide the filters out of the dust collector and transfer to a suit-
able disposal container. Repeat this procedure for the remaining
filters.
5. Inspect the tubesheet and make certain the gasket sealing area is
free of dust to ensure proper sealing of the new filter. Make certain
the area is dry after the cleaning process is complete.
6. Install new ProTura
®
Nanofiber cartridges into each filter compart-
ment, gasket end first. Clean the filter door gaskets and align with
door rod support brackets on the dust collector. Door handle must
be placed at a 90° angle to filter access door prior to placing the
door cover plate support rod in the support brackets (refer to Figure
17). The flat surface of the door handle should be facing down-
ward. To close the filter access door, push the door handle upward,
toward the unit.
The QuickSeal filter access door handle must be in
a perpendicular orientation to door surface prior to
being closed. A flat solid section of door handle will be
visible when door assembly is in the properly closed
position. Refer to Figure 17.
If cam surface of the door handle is visible, QuickSeal
filter door assembly has been improperly installed.
7. The SFC dust collector is now ready to be placed back in service.
Reconnect electrical power and air supply. Please follow the ini-
tial start-up checklist to ensure proper unit performance.
5.2 Dust Removal
Do not let the dust storage drum overfill. This can
cause poor dust collector performance and
require extensive clean-up due to the overflow of
dust when removing the collection container(s).
Turn off the dust collector (power to fan system and com-
pressed air to cleaning system) and empty the dust storage
drum as necessary to prevent dust from accumulating in the
hopper(s). Empty the dust storage drum(s) when two-thirds
full. If the hopper has a slide gate, close the slide gate before
servicing the dust storage drum(s). The dust collector fan
and compressed air cleaning systems do not have to be
turned off if the hopper slide gate is closed prior to servicing
storage drums. Remember to open the slide gate when the
dust storage drum is replaced.
5.3 Servicing the Compressed Air
Components
Shut off and slowly release the pressure in the
compressed air piping or the SFC compressed air
manifold reservoir prior to servicing this equipment.
1. The compressed air system should be periodically checked
to ensure clean, dry, oil-free air is delivered to the SFC dust
collector. Check the compressed air components and service
as recommended by the manufacturer.
2. Periodically check the dust collector air manifold reservoir(s)
for contaminants and drain any condensed liquid from mani-
fold reservoirs.
3.
With the compressed air supply turned on, check the
diaphragm valves, electronic solenoid valves and intercon-
necting tubing between both devices for any air leakage.
Replace any components that are defective or worn.
5.4 Servicing The Direct Drive Blower and
Motor System
ELECTRIC SHOCK HAZARD
All electrical work should be performed by a qual-
ified electrician in accordance with local electrical
codes. Disconnect electrical power before install-
ing or servicing any electrical component.
Refer to blower assembly Installation and Operation Manual
provided with blower assembly for servicing requirements.
!
WARNING
!
WARNING
!
WARNING
!
D A N G E R
Содержание SFC
Страница 1: ...Downward Flow Cartridge Dust Collector Owner s Manual Model SFC...
Страница 7: ...v Page intentionally left blank...
Страница 11: ...4 FIGURE 2 SFC Typical SINGLE UNIT Installation Diagram PARKER PARKER 44 10335 0001...
Страница 12: ...5 FIGURE 3 Recommended Unit Clearances 44 10337 0001...
Страница 14: ...7 FIGURE 4 Single Hopper SFC 44 10309 0001...
Страница 15: ...8 FIGURE 5 Multiple Hopper SFC 44 10309 0002...
Страница 16: ...9 FIGURE 6 Multiple Hopper SFC 44 10309 0003...
Страница 17: ...10 FIGURE 7 Multiple Modules SFC 44 10310 0001...
Страница 19: ...12 FIGURE 8 SFC Pressure Gauge Installation 44 10333 0001 Rev A...
Страница 20: ...13 FIGURE 9 Solenoid Wiring to Pulse Controls for 2 3 4 and 5 Tier Units...
Страница 21: ...14 FIGURE 10 Pneumatic Valve Assembly 44 10332 0001...
Страница 24: ...17 FIGURE 12 Abrasive Inlet Installation 44 10338 0001...
Страница 27: ...20 FIGURE 16 EDAP Interconnection FIGURE 15 EDAP Installation 48 10007...
Страница 30: ...23 FIGURE 17 SFC Series Door Filter Installation 44 10329 0001...
Страница 37: ...30 7 Illustrated Parts FIGURE 21 SFC Series 44 10330 0001 FIGURE 22 SFC Series Explosion Vents...
Страница 39: ...32 Page intentionally left blank...