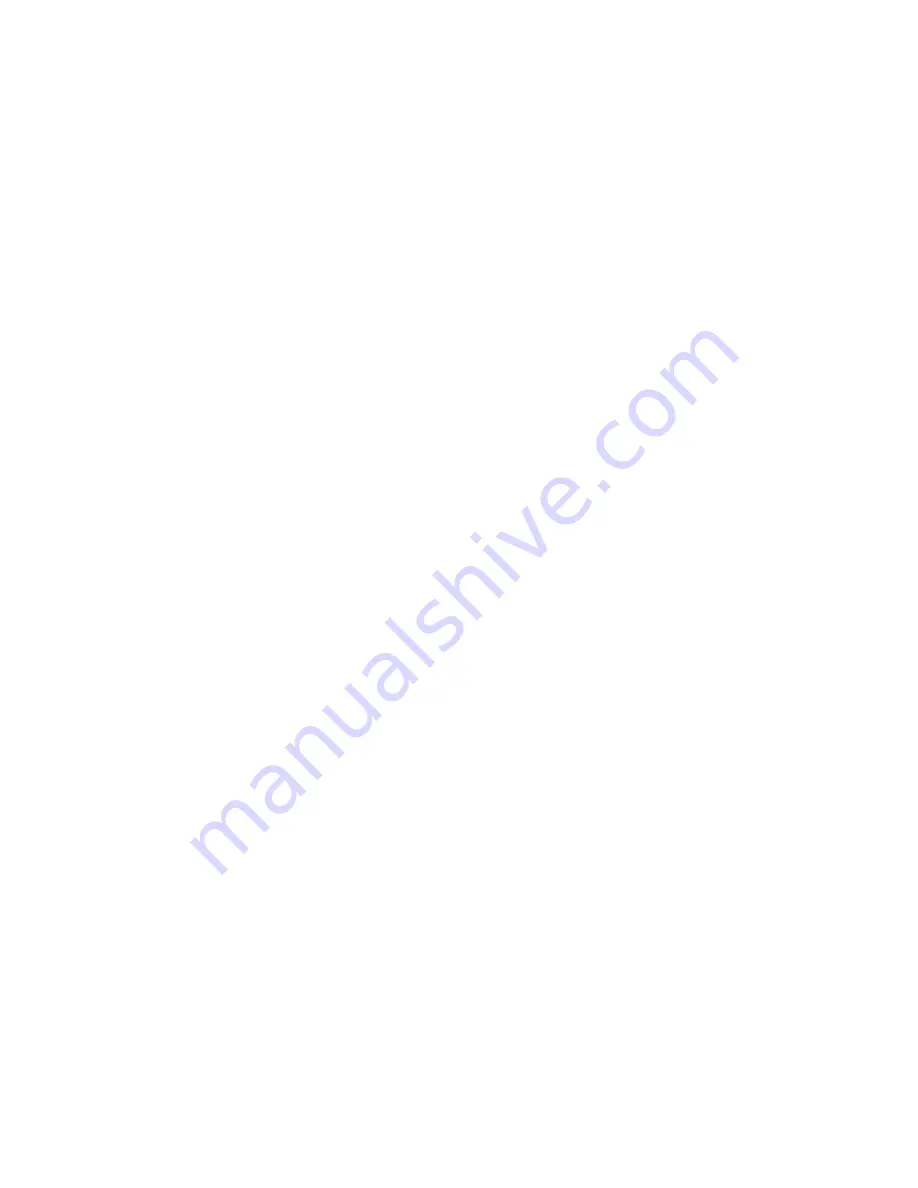
64
6K Hardware Installation Guide
output diode ............................................................ 25, 27
outputs
analog outputs on EVM32 ........................................ 60
digital outputs on EVM32.......................................... 58
high current relay outputs on EVM32 ....................... 59
onboard .............................................................. 25, 27
reed relay outputs on EVM32 ................................... 56
solid state relay outputs on EVM32 .......................... 59
VM25 connections.................................................... 45
part numbers ................................................................... 3
PDS drive connections.................................................. 20
performance specifications.............................................. 4
PKH130M drive connections ......................................... 21
position
error, max. allowable ................................................ 64
power input
6K 33
EVM32 ..................................................................... 55
power LED .................................................................... 41
precautions................................................ 2, 5, 34, 52, 54
product return procedure............................................... 44
recommended installation process.................................. 2
reed relay outputs on EVM32........................................ 56
related publications ..........................................................ii
relay outputs on EVM32 ................................................ 56
return procedure............................................................ 44
RP240 connections ....................................................... 32
RS-232 connections...................................................... 29
RS-485
connections .............................................................. 30
DIP switches, accessing & setting .............................. 5
S drive connections....................................................... 20
safety stop switch (enable input) ..................................... 9
schematics, internal ................................See connections
screw-terminal adapter ..................................................45
servo tuning ...................................................................61
ship kit .............................................................................3
EVM32 ......................................................................47
SIM boards, EVM32 ......................................................47
SIM8-AN-IN ...................................................................47
SIM8-IN .........................................................................47
SIM8-OUT-EVM32 ........................................................47
sizing your power supply, 6K .........................................33
solid state relay outputs on EVM32 ...............................59
solutions to common problems ......................................39
specifications
environmental (6K)......................................................7
EVM32 ......................................................................48
general........................................................................4
staight-through cable .....................................................29
status LEDs ...................................................................41
SV drive connections.....................................................15
technical support ...........................................................38
temperature specification.................................................7
testing I/O installation ....................................................34
TQ10 drive connections.................................................16
trigger input connections..........................................25, 26
troubleshooting ..............................................................37
methods ....................................................................38
resolving serial communication problems .................43
solutions to common problems .................................39
tuning, servo ..................................................................61
Vix drive connections
servo.........................................................................16
step & direction .........................................................22
VM25 25-pin screw-terminal adapter .............................45
Zeta drive connections...................................................20
www.comoso.com
Содержание 6K Series
Страница 1: ...www comoso com ...
Страница 12: ...6 6K Hardware Installation Guide 6K Series Dimensions Mounting Dimensions 6K2 6K4 6K6 6K8 www comoso com ...
Страница 37: ...Chapter 1 Installation 31 2 Wire Connections plus ground www comoso com ...
Страница 55: ...Appendix B EVM32 Installation 49 EVM32 ll Dimensions www comoso com ...