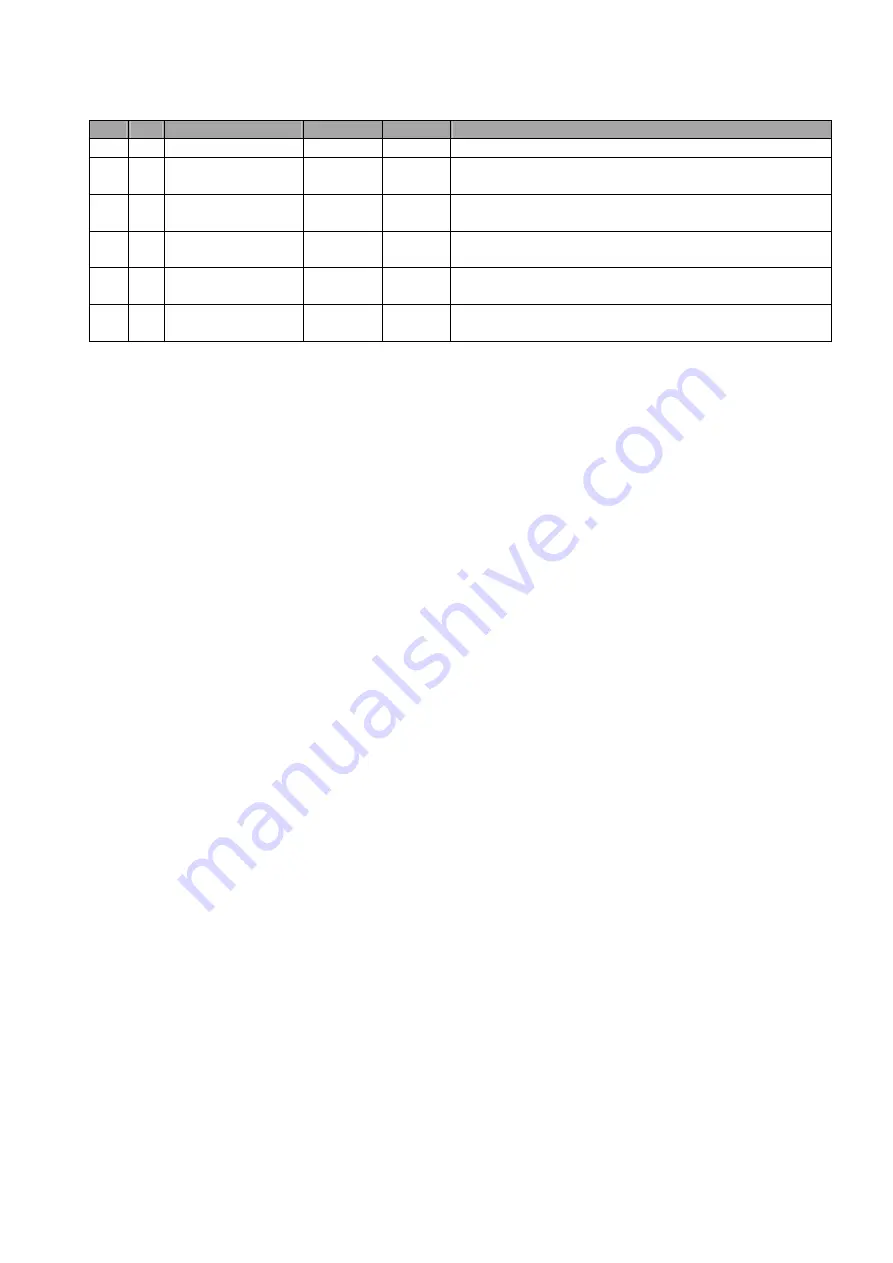
№
SR-ZSV00039
-
29
-
Motor Business Unit, Appliances Company, Panasonic Corporation
Specify the following parameters for real-time auto tuning in accordance with gain switching settings.
Category
No.
Parameter
Setup range
Unit
Function
1
14
2nd gain setup
0
1
Specify "0" for other cases than maintaining current settings.
1
15
Mode of position
control switching
0
10
If gain switching is valid, specify "10."
If gain switching is invalid, specify "0."
1
16
Delay time of position
control switching
0
10000
0.1 ms
Specify "50" for other cases than maintaining current settings.
1
17
Level of position
control switching
0
20000
Specify "50" for other cases than maintaining current settings.
1
18
Hysteresis at position
control switching
0
20000
Specify "33" for other cases than maintaining current settings.
1
19
Position gain
switching time
0
10000
0.1 ms
Specify "33" for other cases than maintaining current settings.
5) Usage
Control parameters are specified automatically if a value other than "0" is specified for Pr0.02 "Real-time auto-g
ain tuning setup" in accordance with Pr0.03 "Selection of machine stiffness at realtime auto-gain tuning"
Input an operation command after the drive has been enabled by Servo On. If estimation load characteristic is
successful, Pr0.04 "Inertia ratio" is updated. In addition, some mode setting may cause changes of Pr6.07
"Torque command additional value", Pr6.08 "Positive direction torque compensation value", and Pr6.09
"Negative direction torque compensation value".
Specifying higher settings for Pr0.03 "Selection of machine stiffness at realtime auto-gain tuning" can
increase response of motor. Adjust to the optimum value while monitoring the positioning stabilization
time and vibration conditions.
6) Other cautions
①
Strange noises or vibrations may occur on the first action of turning on the servo immediately after startup
or setting higher value of Pr0.03 "Selection of machine stiffness at realtime auto-gain tuning" until estima-
tion of load characteristic becomes stable. This is not a fault if the function becomes stable soon. If os-
cillation or continued generation of abnormal noise through three or more reciprocating movements often
occurs, take the following steps.
1) Specify lower value for Pr0.03 "Selection of machine stiffness at realtime auto-gain tuning"
2) Specify "0" for Pr0.02 "Real-time auto-gain tuning setup" and make real-time auto tuning invalid.
3) Specify a theoretical value of device for Pr0.04 "Inertia ratio" and specify "0" for Pr6.07 "Torque
command additional value", Pr6.08 "Positive direction torque compensation value", and Pr6.09 "Nega-
tive direction torque compensation value".
②
After occurrence of strange noises or vibrations, values of Pr0.04 "Inertia ratio," Pr6.07 "Torque command
additional value", Pr6.08 "Positive direction torque compensation value", or Pr6.09 "Negative direction
torque compensation value" may have been changed into extreme values. If this is the case, take Step 3)
above.
③
The results of real-time automatic gain tuning, such as Pr0.04 "Inertia ratio," Pr6.07 "Torque command ad-
ditional value", Pr6.08 "Positive direction torque compensation value", and Pr6.09 "Negative direction
torque compensation value" are written in EEPROM in every 30 minutes. Upon restarting of power, auto
tuning is performed using the data for initial values. The results of real-time auto gain tuning are not
stored if the power is turned off before 30 minutes have elapsed. In this case, manually write the parame-
ters to the EEPROM before turning off the power.
④
The control gain is updated when the motor is stopped. Therefore, if motor is not stopped because gain is
excessively low or commands are given continually in one direction, the change in Pr0.03 “Real-time
auto-tuning machine stiffness setup” may not be reflected. In this case, abnormal sound or oscillation
may be generated depending on the stiffness setting that is reflected after the motor stops.
After the stiffness setting is changed, be sure to stop the motor and check that the stiffness setting is re-
flected before performing next operation.