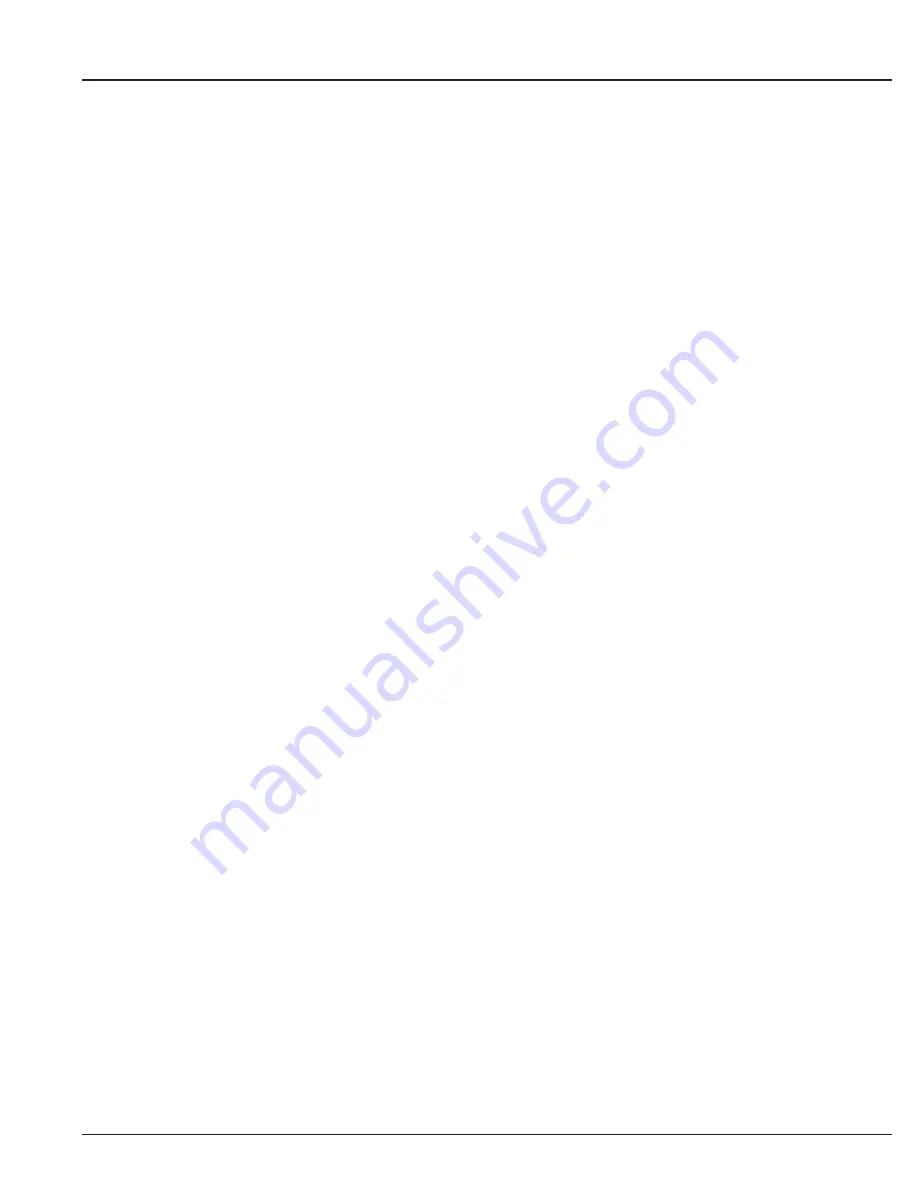
zipldr_setup&operations
www.OmniTurn.com
(541) 332-7004
(541)-332-1018 fax
Fast... Precise... A
ff
ordable...
Zip Loader Setup & Operations
Omni
Turn
Page 21 of 44
All Modes
Overview of Operation
Common Features
The ZipLoader will handle bars or parts up to 25 inches long and 1/8” to 1-1/16” in diameter. Bars or
parts are loaded into the tray. An optional hopper is available for parts up to 21 inches long and 3/4”
in diameter. At start of program a new bar or part is escaped into a “vee” and pushed through collet.
Load/unload times from about 3 to 7 seconds are typical, depending on size of part and material.
Bar Mode (M50)
In “Bar Mode”, the ZipLoader operates as a magazine bar-loader.
New bar is pushed to hard-stop on table, and the collet is closed. After machining, the part is cut off,
stop re-located at face of part, collet is opened and bar feeds out. The cycle repeats until End of Bar
sensor is reached. Conditional sub-routine in program instructs ZipLoader to eject remnant and load
new bar. If another bar is available the process continues as before. If there are no more bars in the
tray, a second conditional sub-routine instructs ZipLoader to feed forward to Eject sensor, which stops
the CNC and lights the red Stack Lamp, alerting the operator.
Part Mode (M51)
In “Part Mode”, the ZipLoader operates as a shaft-loader, and part is qualified at face.
Part is pushed against a hard-stop on table which is located at face of part. Set “InPlace” sensor on
ZipLoader to light at this point, which automatically closes the collet and stops pushing. After machin-
ing, part is ejected and new part is loaded. If ZipLoader shuttle passes “InPlace” sensor (no part in
collet), ZipLoader stops the CNC and lights the Stack Lamp, alerting the operator to add re-fill tray.
Stop Mode (M52)
In “Stop Mode”, the ZipLoader operates as a shaft-loader, and part is qualified at rear.
The shuttle stops against shot-pin on adjustable rear-stop on ZipLoader. Spring-loaded stop on table
gently pushes part against pusher and collet is closed. After machining, finished part is ejected. If
“Part Located” sensor on spring-loaded stop doesn’t light (no part at stop), ZipLoader stops the CNC
and lights the Stack Lamp, alerting the operator to re-fill tray or hopper.
Second Feed in Part Modes; (for Second Feed in Bar Mode see Page 22)
To feed part further out to do more machining near collet, stop spindle (m05), locate stop near face
of part, open collet (m13), push slow (m42), move stop slowly back to new Z location, stop pushing
(m44), close collet (m12).
Slow Eject (M59)
If parts are delicate, put m59 before m48 (eject) to eject parts using speed set by ‘Slow’ needle-valve.
2Part Mode (M53)
(option)
In “2Part Mode”, the finished part is pushed out by the next part to be machined; very fast cycle.
Part can be qualified at face or at rear, by using appropriate stop on tooling plate. This mode pro-
vides the fastest load/unload times, but requires an adjustable front-stop on the rodless cylinder, and
a “restrainer” on the tooling plate to prevent the second part from over-traveling. The program starts
with a part in the collet. The shuttle stops against an adjustable front-stop on ZipLoader, and hard or
spring-loaded stop on table locates the part before collet is closed.
Air-Eject Mode (M51)
(option)
In “Air-Eject Mode”, the finished part is pushed out by air blast; fast cycle.
This mode is similar to “Stop Mode”, but the shuttle doesn’t need to push past the adjustable stop on
ZipLoader. Part can be qualified at face or at rear, by using appropriate stop on tooling plate. Fast
cycle time for light parts can be accomplished by locating stop on table then opening the collet. For
tubing, air through tube while machining can keep chips out of tube.