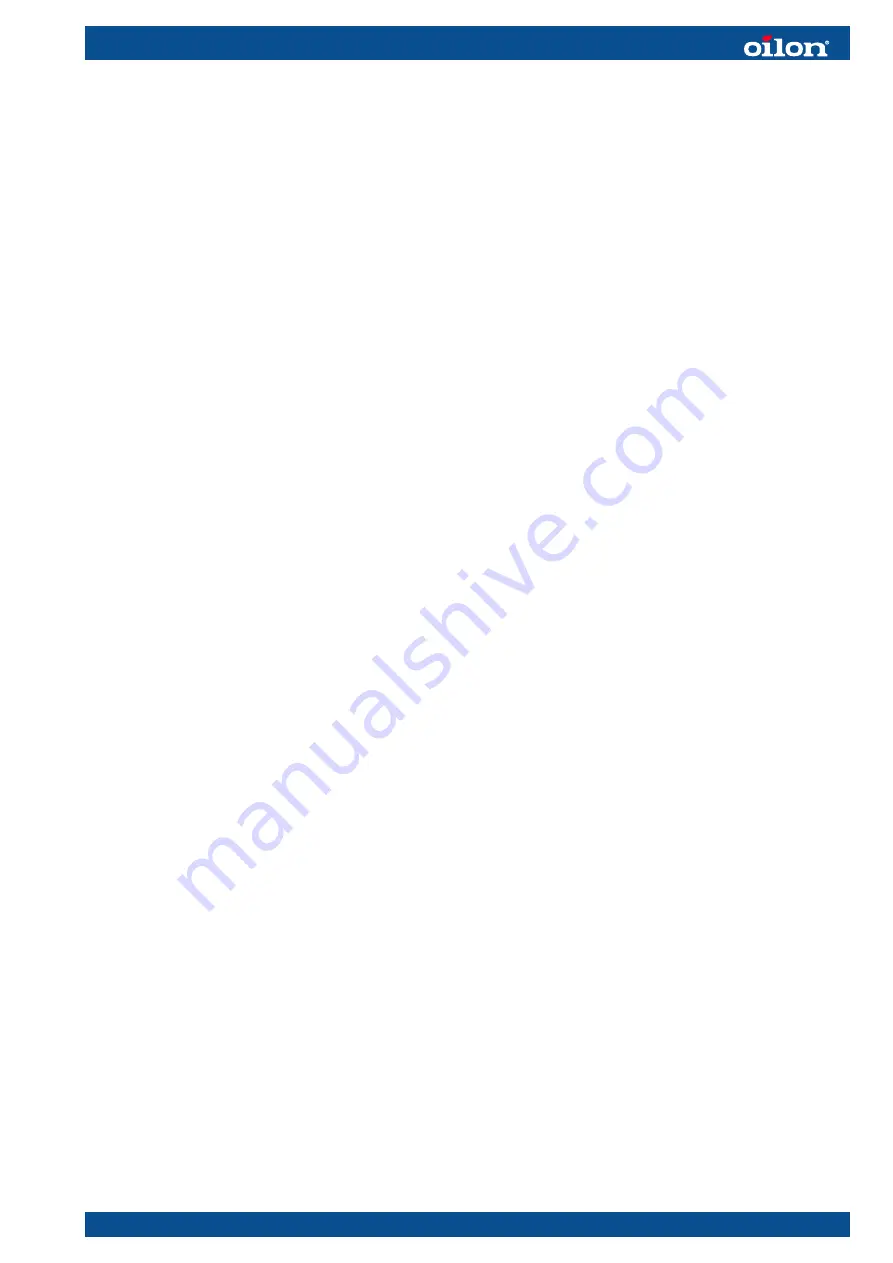
Boiler equipment and remote control connections are connected to the burner wiring
base. Because of the limited number of N/PE connectors and cable gland billets,
possible cascade connection of the appliance must be implemented outside the
burner’s wiring base.
● When using frequency converter, do cabling work and grounding according to
manufacturer instructions.
● Locate frequency converter as near to motor as possible to avoid interference
caused by long cabling.
● Separate supply cables from control and bus cables in cable rack if they cannot be
installed in separate cable racks.
● Check that shielded cables have proper connections.
M5164 1640EN
31 (95)
Содержание GKP-50 MH
Страница 2: ......
Страница 21: ...3 3 Installing burner GKP 50 MH main dimensions D048897 ver 3 M5164 1640EN 19 95...
Страница 98: ...96 95 M5164 1640EN...
Страница 99: ......
Страница 100: ...Tarmontie 4 FI 15860 HOLLOLA FINLAND Tel 358 3 85 761 Fax 358 3 857 6239 Email info oilon com www oilon com...