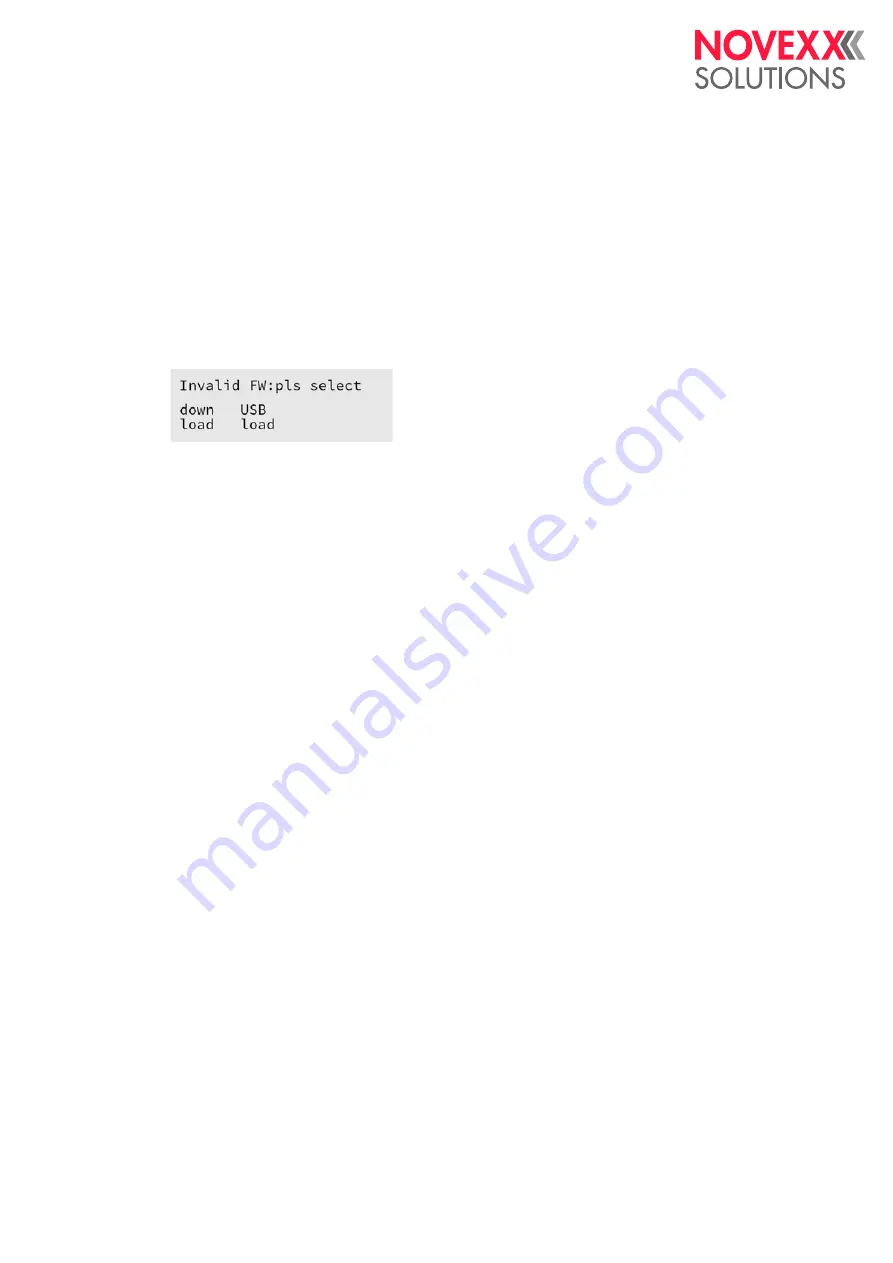
Service Manual
ALS/XLS 20x/256/272
02/2019 | 00
229
General software errors
The occurrence of errors in the firmware can never be completely precluded. These types of errors
are given the name “general software error” in the error directory. They can only be corrected by
the manufacturer.
If an error listed as a “general software error” in the error directory occurs repeatedly, please inform
the manufacturer, quoting the error number and explaining the circumstances in which it occurred.
Machine fails to start
If no valid firmware is installed, the startup of the machine ends with the following bootloader mes-
sage::
The missing firmware can now be loaded via the serial interface or from an USB stick.
For details see chap.
For details see chap.
Содержание ALS/XLS 204
Страница 2: ......
Страница 8: ...Service Manual ALS 20x 256 272 05 2019 8 Contents ...
Страница 110: ...Service Manual ALS XLS 20x 256 272 02 2019 02 110 ...
Страница 258: ...Service Manual ALS XLS 20x 256 272 02 2019 03 258 Repair 199 Removing the fan C A B C D ...
Страница 309: ......
Страница 310: ......
Страница 311: ......
Страница 312: ...Novexx Solutions GmbH Ohmstraße 3 85386 Eching Germany 49 8165 925 0 www novexx com ...