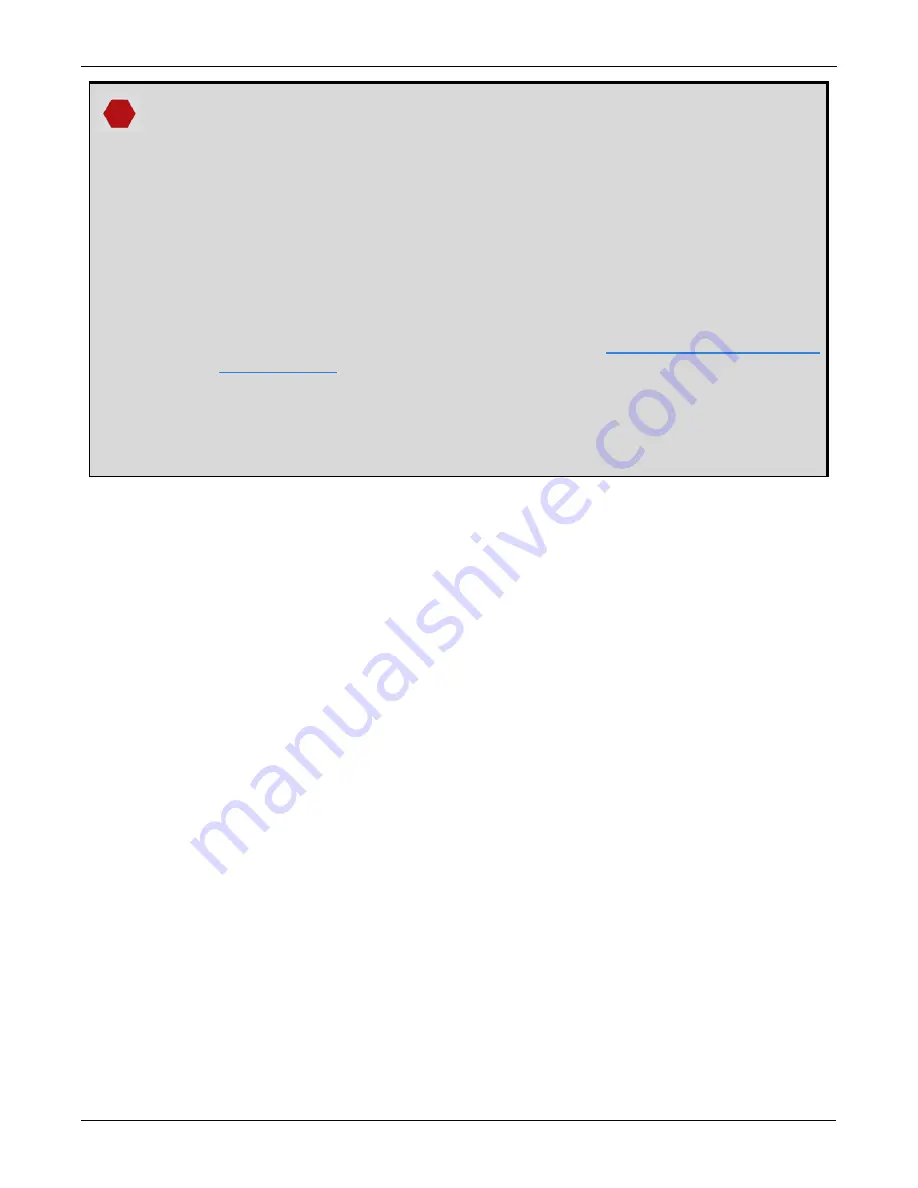
Chapter 4 SMART7 with SPAN Operation
SMART7 Installation and Operation User Manual v6
76
Logging Restriction Important Notice
Logging excessive amounts of high rate data can overload the system. When configuring the output for
SPAN, NovAtel recommends that only one high rate (>50 Hz) message be configured for output at a
time. It is possible to log more than one message at high rates, but doing so could have negative
impacts on the system. Also, if logging 100/200 Hz data, always use the binary format and, if possible,
the short header binary format (available on most INS logs).
For optimal performance, log only one high rate output at a time. These logs could be:
l
Raw data for post processing
RAWIMUXSB ONNEW
l
RAWIMU logs are not valid with the ONTIME trigger. The raw IMU observations contained in
these logs are sequential changes in velocity and rotation. As such, you can only use them
for navigation if they are logged at their full rate. Refer to the
for log and command details.
l
Real time INS solution
IMURATEPVA ONNEW or IMURATEPVAS ONNEW
l
Other possible INS solution logs available at high rates are: INSPVASB, INSPOSSB,
INSVELSB, INSATTSB
Specific logs need to be collected for post-processing. See
Data Collection for Post Processing
To store data from an OEM7 receiver, connect the receiver to a computer running NovAtel Connect or other ter-
minal program capable of recording data.
4.5.5 Body to Vehicle Frame Rotation Calibration Routine
Kinematic alignment requires that the rotational offset between the vehicle and IMU Body frame (RBV) is known.
If the angles are simple (that is, a simple rotation about one axis) the values can easily be entered manually
through the
SETINSROTATION RBV
command. If the rotational offset is more complex (that is, rotation is
about 2 or 3 axis), then the calibration routine provides a more accurate estimation of the values.
The steps for the calibration routine are:
1. Apply power to the SMART7.
2. Configure the SPAN system including an approximate IMU Body to Vehicle frame (RBV) rotation. See
3. Ensure that an accurate lever arm has been entered into the system.
4. Perform an initial system alignment using one of the methods described in
on page 71. Ensure the system reaches Solution Good.
5. Enable calibration using the
INSCALIBRATE
command with an optional standard deviation target.
INSCALIBRATE RBV NEW [target_stdev]
6. To monitor the calibration, log INSCALSTATUS using the ONCHANGED trigger.
7. Start to move the system. Movement of the system is required for the observation of the angular offsets.
Drive a straight course on level ground (remember that most roads have a crown resulting in a constant roll
of a few degrees). Avoid driving on a surface with a constant, non-zero, slope to prevent biases in the com-
puted angles. Vehicle speed must be greater than 5 m/s (18 km/hr) for the calibration to complete.
8. When the calibration is complete, either because the accuracy requirement has been met, or the calibration