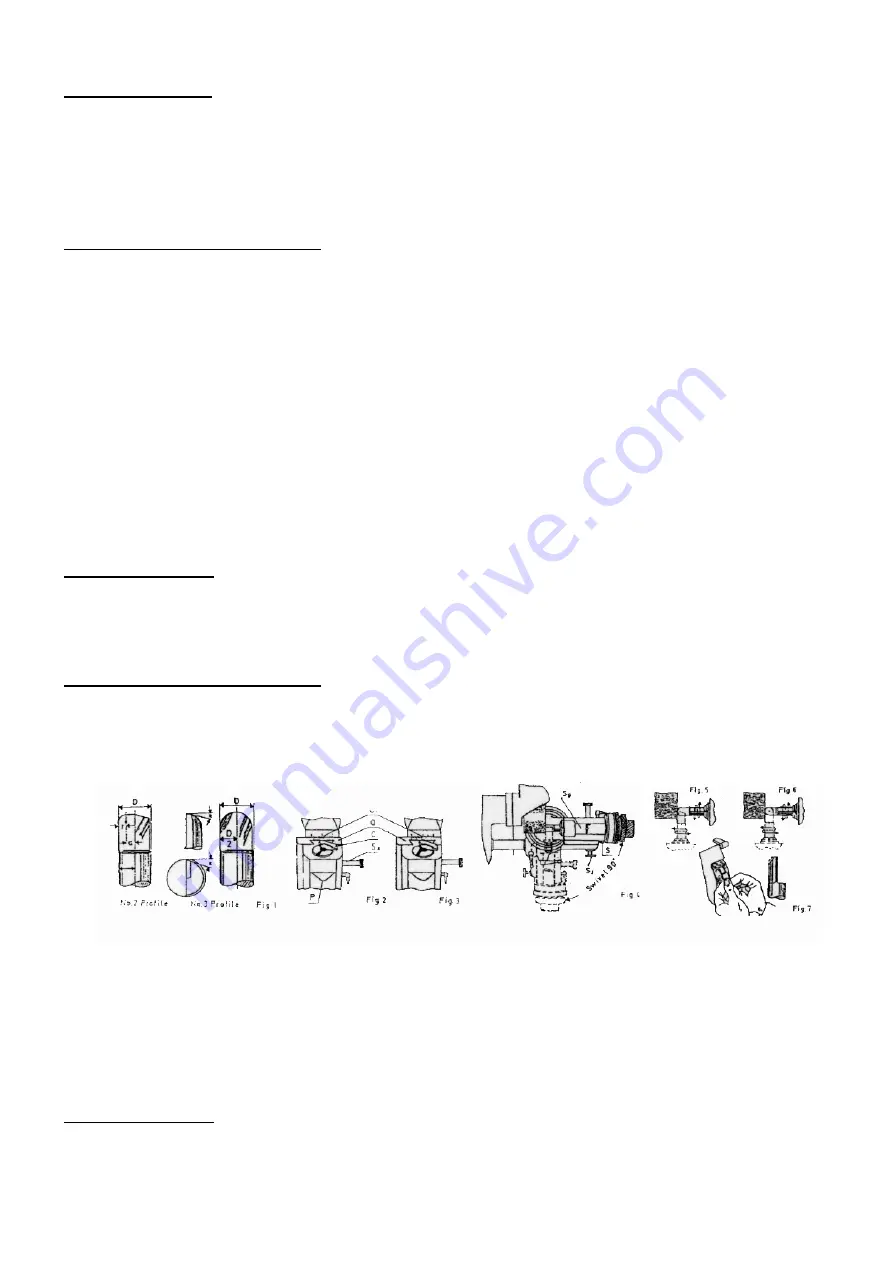
5.
Tighten clamping lever T4;release clamping lever T7;shift work fixture on tubular guide to bring cutter into light contact with
grinding wheel, tighten clamping lever T7;release clamping lever T4.
Circular Grinding
6.
Draw index pin P out of the slot; grind desired diameter by rotating spring collets bearing through 360
o
. During this operation
slowly rotate adjustable stop screw G, while continuously rotating the spring collets bearing, to advance the work fixture past
the grinding wheel; this will produce uniform stock removal. Fine adjustment during circular grinding is by screw H. Stop screw
G is used to establish the length of the cylindrical portion which should always be slightly longer than the cutting lip.
7.
Return whit dot into window Unengaged index pin P into short slot to enable bearing to be rotate 180
o
between the index plate
stops.
Grinding the Back Rake Angle
8.
When grinding the back rake angle, use the fine adjustment screw H over the entire range of rotation of the collets bering (see
Fig.3a). Grinding of the back rake angle is positive controlled. The angle is required to extend over the entire lengthy of the
cutting lip.
The vertical swivel bearing, which permits the work holding fixture to be swung back, enables relief angles up to 40
o
to be produced.
Relief angles over 40~can be obtained by additionally rotating the collets bearing in the index head. (Only for cylindrical or tapered
cutter with straight end cutting edges or for pointed cutters.)Upon completion of grinding operations a very narrow land must remain
at the cutting edge (see Fig.4).
Circular Grinding of Cutters-
Grinding the Back Angle of End Cutting Edges
The end cutting edge illustrated in Fig. 1 may be ground it an operation immediately following the grinding of the side cutting edge; or
it may be ground independently. In the latter case the cutter will have to be aligned by means of gauge Cad clamped in position.
Whenever a single-lip cutter is to be ground, the aligning will have to be used, as one leg of the cutting angle should be selected to
suit the material to be cut. (See page 5)
Setup Operations
1.
Release clamping levers T2; using setting scale S2, set swivel arm at approx. 3
o
; tighten clamping lever T2.
2.
At desired angle; for example set arm at 75
o
for back angle of 15
o
(see Fig.2and Fig.3). Tighten clamping lever T3and T6.
3.
Tighten clamping lever T4; release lever T7; shift work fixture on tubular guide to bring cutter into light contact with grinding
wheel tighten clamping lever T7; release lever T4.
Grinding the Back Rake Angle
4.
Fine adjustment screw H serves to set the index head laterally reactive to the wheel and to set the work for the desired depth of
cut. It is also possible to produce the desired back rake by holding the cutter against the circumference of the grinding wheel as
is shown in Fig4.
Circular Grinding of Cutters –
Grinding the Back Angle of End Cutting Edges (Round)
Cutter profiles having either on-center or-off-center radii are derived from cylindrical single0lip cutters having a straight end cutting
edge by rounding off the corner as shown in Fig.1 (No.2 and 3 profiles).
For this reason it is necessary, during grinding the end rake angle, that the work fixture is set at the side rake angle by means of
setting scale S2. If the end cutting edge is ground immediately after grinding the Sid setting edge, it will not be necessary to re-set the
work fixture and to re-align the cutting lip by means of gauge C.
Setup Operations
1.
a. No.2 profile : Release clamping lever T1:rotat knurled knob S4 to set cross slide by means of venire scale C1 for desires
radius (to the right);tighten clamping lever T1,9see Fing.2)as the radiuses corner is required to be tangent to the cutter
4