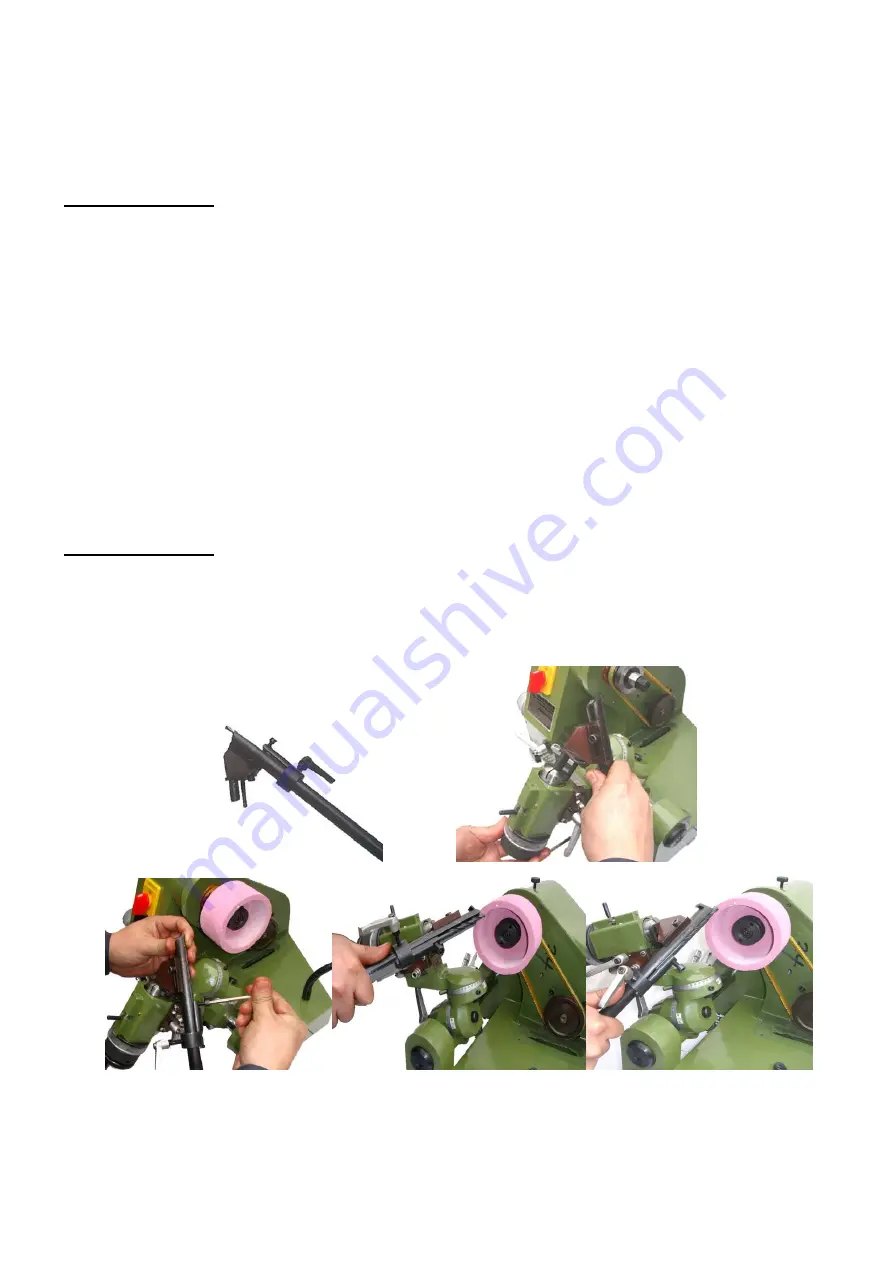
slide
of the index head bracket, introducing retaining pin 2 into the bore of the off-side setting gauge. Adjustable stop 5 has a flat furnace on
one side for holding twist drills of 3 to 18mm (/18”to11/16”) diameter. The drill is held by hand against stop 5 and the swivel-mounted
V-guide 4 during grinding (Fig.1). After backing off clamping screw 7, stop 5 with ring 999 can be pulled off (depress catch 10) and
mounted in reveres position. This permits clamping of small drills (3 to 6mm or 1/8”to 1/r”dia.)By means of clamping screw 6, since
experience has shown that such drills are difficult to hold by hand grinding.
Setup Operations
1.
Release clamps K3 and K4. Hold index drum T4 against stop by means of the knob and set swivel arm at 13 .Retighten clamps
K3 and K4.
2.
Release clamp K2 and set swivel arm at zero on setting scale T2 (resulting in a normally suitable rake angle). If larger or
smaller rake angles are required, adjust swivel arm accordingly. Retighten clamp K2.Release clamp K6 and screw D6. Move
index head slide T until its front face roughly coincides with the front face
3.
of cross slide Q. Retighten clamp K6 and screw D6.Only if new grinding wheel is used :
4.
Release clamp K5,move cross slide Q fully to the right using knurled screw S5.Retighten clamp K5.Release clamp 3(on
attachment) and adjust swivel-mounted V-guide 4 until the scale shows the diameter of the twist
5.
Drill to be ground. Retighten clamp 3.Release clamp K1,tighten clamp K. Move index head bracket on the tubular guide until
gauge plate 8 is position
6.
approx. .04” (laterally of the face of the grinning wheel. Align vertical swivel mount index mark with reference line of tubular
guide, then retighten clamp K1 and release clamp K. Place theist drill on V-guide 4.Back off clamping screw 7 and advance
stop 5 until the cutting face of the drill rests
7.
Against gauge plate 8, projecting approx. 0.02” (.5mm) Tighten clamping screw 7. When using the adjustable stop in reverse
position (for small twist drills of 3 to 6mm 1/8”to 1/4” dia.), tighten clamping screw 6.
Setup Operations
8.
Swivel twist drill grinding attachment upwards. Use fine adjustment screw F to advance the drill until it contacts the grinding
wheel. Grinding first cutting edge by swiveling the attachment downwards (Fig.3). Repeat feed and grinding operation if
required.
9.
Place twist drill into V-guide 4 in 180 inverted position and grind second cutting edge leaving the attachment and the adjustable
stop in the previously used position (i.e. not advancing fine adjustment screw F.)
INSTRUCTION FOR GRINDING END MILL
Change the original work head into End mill attachment work head. (As drawing l)
Insert the suitable size U2 collets into the tapered hole of the end mill attachment work head.
9