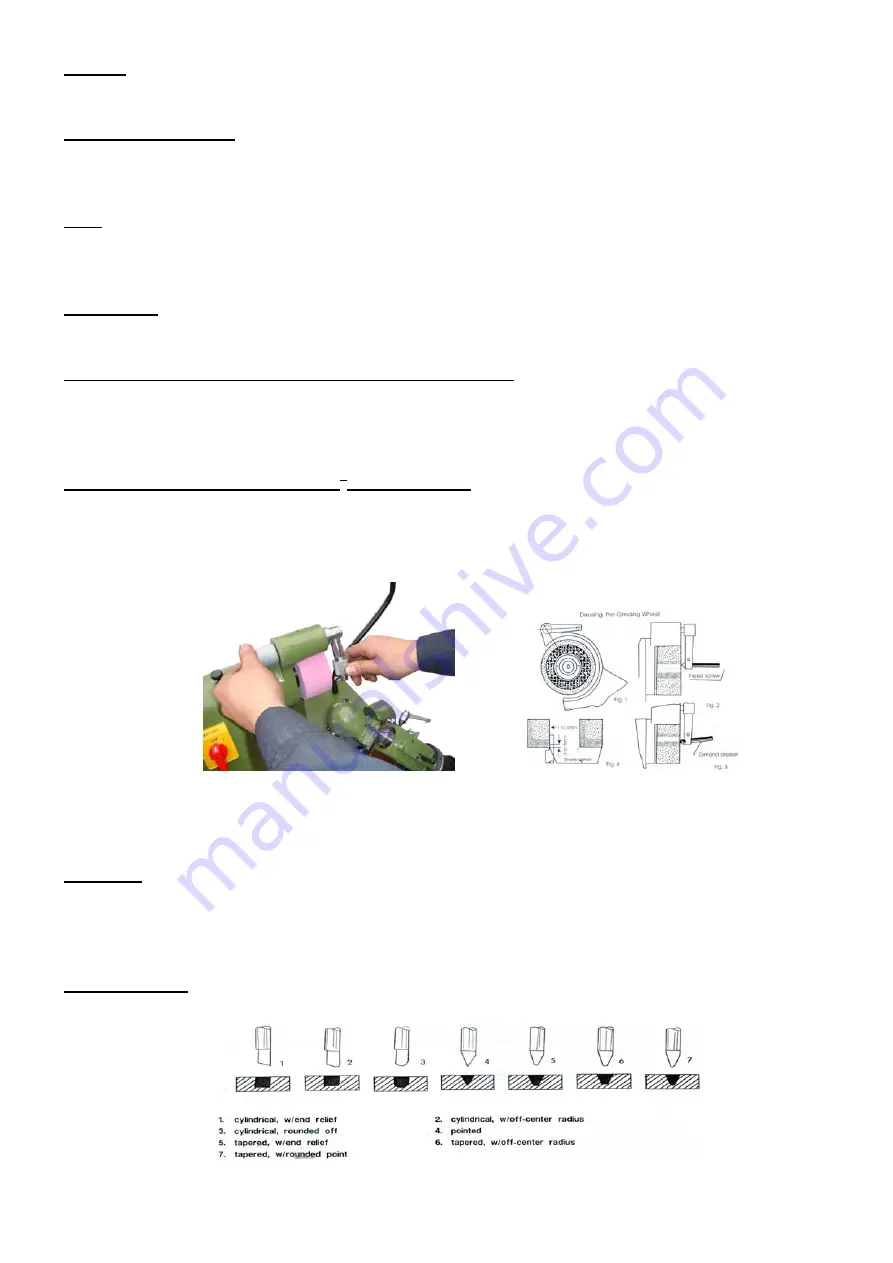
Servicing the Index Head Bracket
General
After a major period of use it will be necessary to dismantle the index head bracket and to clean and lubricate the collect
sleeve bearing, the index head slide, and the swivel arm.
Collets Sleeve Bearing
To remove the collect sleeve proceed as follows; Remove ring nut N5, index drum N4, and index ring R7, in that order.
Remove two nuts M3 pull or out index bearing sleeve E. The annular grease chamber in the longitudinal slide L, which has thus
been made accessible, should then be cleaned with petrol and refilled with tease.
Slide
Release clamping screw T5 and remove screw S5.Pull our index head slide S. Clean all working surfaces, smear lightly with
oil, cross slide Q can not be removed. Release clamping screw t1 and turn screw S4 to move the cross slide to its extreme positions.
Clean the bearing surfaces smear lightly with oil.
Swivel Arm
To remove the swivel arm and the index head as a unit remove the two nuts M4.Clean the bearing surfaces and smear them
with oil.
Adjusting the Clamping Mechanism of Index Drum F.
After a major period of use clamping lever T6 should no longer lock swivel index drum F, screw U2 will have to be adjusted.
For this purpose proceed as follows: Remove swivel arm as described above; remove screw U3 and stop plate A1; back off nut M2
and screw U1 and pull out clamping lever T6. Lift off index drum F to pull out adjusting nut and screw U2 rotate screw 180
o
relative
to nut to reduce the length-to reassemble parts reverse procedure.
Adjusting the stop pin for the 90
o
swivel motion
If, due to constant striking of stop plate A1 against stop pin A2 and A3, the swivel range should no longer be
exactly 90
o
correct the adjustment by turning the two eccentric stop pin A2 and A3. Turning stop pin A2 will change the
cylindrical setting of the collect sleeve bearing, while turning stop pin A3 will adjust the 90
o
swivel motion.
Dressing the Grinding Wheel
Wheel Turing and dressing should be performed at regular intervals. Dressing is done by means of a diamond set in a tip
which is held in a rod. The latter is attached to an arm which is provided with a feed screw. The diamond tool assembly s supported by
the wheel guard (see Fig. 1 and 2) wheel Turing and dressing is particularity necessary when the wheel has become headed or when
sharp corner has been worn off. Failure to comply with rule will result in poor surface finish and overheating of the cutting tools.
Messing:
1. Loosen clamping nut D. Shift dressing diamond to the right. Swing the dressing attachment in front of the wheel rim.
2. Set diamond, dresser 1 mm in front of the wheel. Lock clamping nut D.
3. Turn feed screw until the dressing diamond contacts the wheel. The layer to be dressed is 0.2mm.Give feed screw 1/5th turn.
Cutter Profiles-Tool Angle-Cutting Speeds
Cutter Profiles
As rule, single-lip milling cutters are given one of the seven basic profiles illustrated below:
1