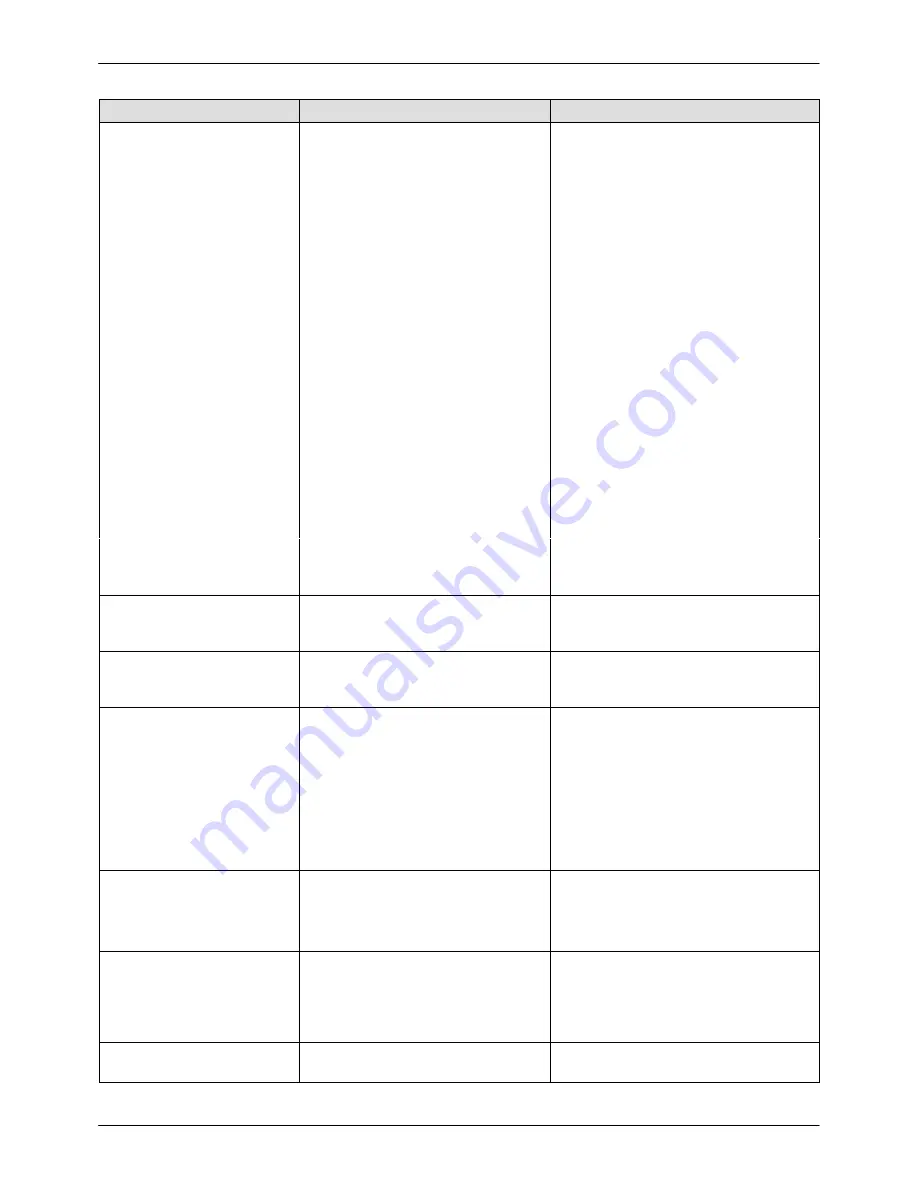
Troubleshooting
6‐3
Part 7192568-03
E
2020 Nordson Corporation
Corrective Action
Possible Cause
Problem
5.
Powder in feed
hopper not fluidizing,
or clouds of powder
erupting from surface
Fluidizing air pressure too low or
too high
Increase the fluidizing air pressure
until the powder is gently boiling.
Decrease the pressure if clouds of
powder are erupting from the surface.
Moist or oil-contaminated powder
Check the air supply for water or oil.
Check the filters, separators, and air
dryer. Replace the powder in the feed
source if it is contaminated. Refer to
the next possible cause.
Fluidizing plate gasket leaking, or
fluidizing plate plugged, cracked,
or installed incorrectly
Check for air leaks around the
fluidizing plate gasket. If leaks are
found, replace the gasket
Inspect the fluidizing plate for stains,
discoloration, polished surfaces, or
cracks. Replace it if it is
contaminated, plugged, or damaged.
The plate should be installed with the
smooth surface up (in contact with the
powder).
Incorrect ratio of reclaimed to virgin
powder
Increase or decrease the transfer
rate. The powder supply should be no
more than three parts reclaim-to-one
part virgin powder.
Uneven distribution of powder in
feed source
Check the powder and the fluidizing
plate for contamination as previously
described.
6.
Large dump valve on
bottom of hopper
leaking air/powder
Pinch valve inner sleeve failure
Replace inner sleeve
7.
Large dump valve on
bottom of hopper not
closing fully
Supply regulator set too low
Check/set supply air to pinch valve is
set according to the default settings
8.
Hopper not cleaning
sufficiently
Low system air pressure during
colour change
Ensure the operating pressure does
not fall below 6 bar during colour
change. Must remain consistent
throughout.
Note: Hopper cleaning consistency
will also vary based on the number of
gun in the system. Lower number of
guns may need additional cleaning
time.
9.
Contaminants in feed
hopper powder
Sieve screen torn
Replace the screen.
Sieve screen not thoroughly
cleaned before installation
Remove and clean the sieve screen.
10. Damage to sieve
screens
The Ultrasonic Sieve uses very fine
wire on the sieve screens.
Mishandling during cleaning or
replacement can damage the sieve
screen.
Use care when handling and cleaning
sieve screens.
11. Powder build up on
sieve screen
Screen not cleaned frequently
enough
Clean the sieve mesh at more
frequent intervals.