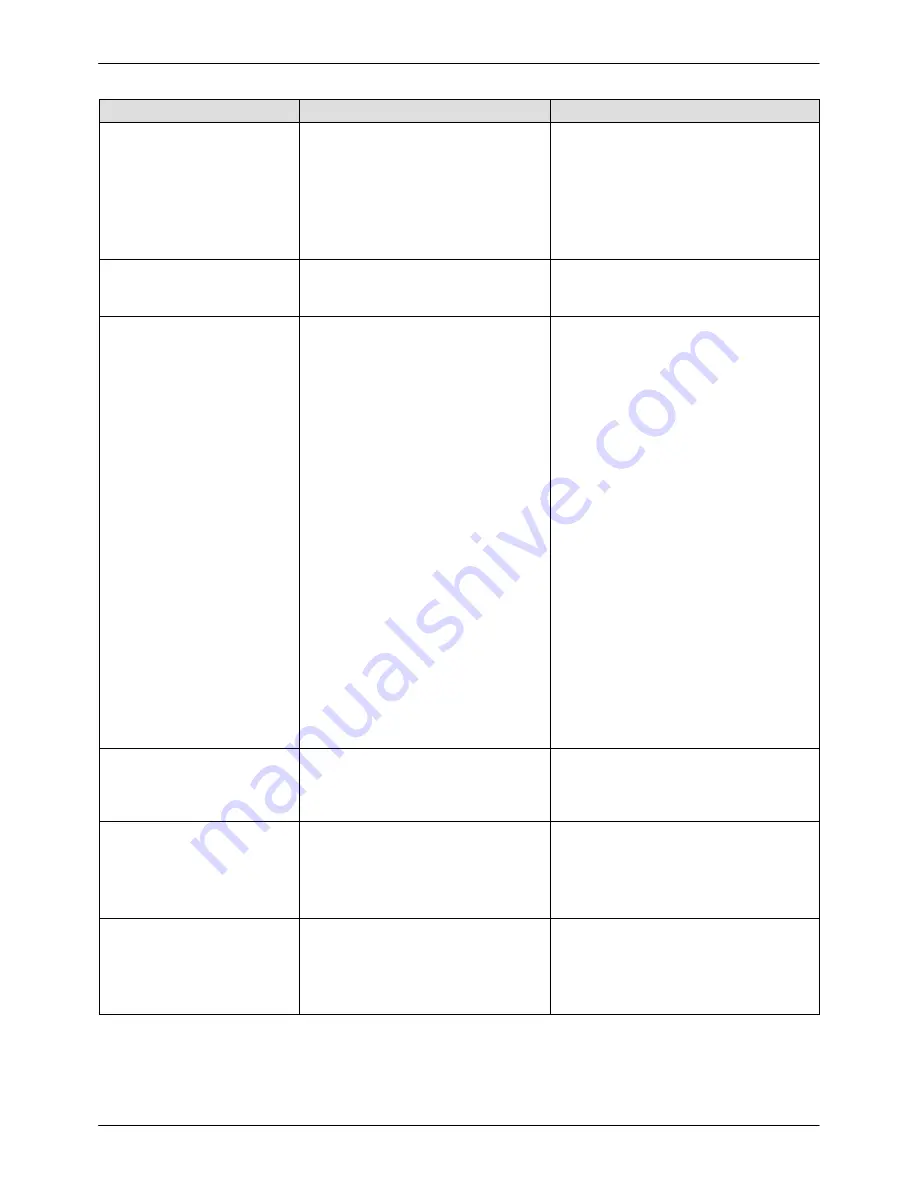
Troubleshooting
6‐4
Part 7192568-03
E
2020 Nordson Corporation
Corrective Action
Possible Cause
Problem
12. Sieve screen backing
up with certain
powders
Incorrect amplitude setting in
controller.
Loose ultrasonic transducer/probe
(if sieve not operating)
Default setting for sieve screen
amplitude is set to 50% from factory.
Contact your Nordson representative
to adjust the amplitude.
Check connection is the correct
torque setting, 15-20 Nm
13. Excessive sieve noise
Knobs or clamps not tightened;
screen gasket damaged
Make sure the clamps are tight.
Check the screen gasket and replace
it if damaged.
14. Reclaim or fresh
powder transfer pump
turned on, but pump
does not run
E-Stop button pressed
Reset the E-Stop button.
Afterfilter exhaust fan not running,
or fan interlock circuit defective
Turn on the exhaust fan. Check the
fan interlock wiring between the feed
center panel and the main system
panel.
Sieve motor not running
Reclaim or Virgin pumps will not run
unless the sieve is on. Turn on the
sieve.
Reclaim or Virgin Powder wiring
circuit is defective
Check the wiring. Repair or replace
as needed.
No air supply to solenoid valve
assembly, or solenoid valve not
opening
Check the air supply to the solenoid
valve assembly on the side of feed
center. Check the solenoid valve and
wiring. Replace the valve or repair the
wiring as needed. Refer to Section 2
for the solenoid valve location.
Problem with transfer pump
controls or pump.
Check the pump and controls. Refer
to High Capacity HDLV pump manual.
L
evel sensor failed or wiring
defective
Check level sensor and wiring. Repair
or replace as needed.
15. Reclaim or Fresh
powder transfer
pump cannot be
purged
Reclaim or Virgin pump not turned
on
Turn the Reclaim or Virgin pump
switch to the On position.
16. Reclaim or Fresh
powder transfer pump
turned off but
continues to run
Solenoid valve in manual override
Check the solenoid valve assembly.
Make sure the manual operator on the
valve is not in override position.
Solenoid valve failed open
Replace the valve.
17. Fresh powder transfer
pump is turned on but
pump not running
Level sensor on feed hopper is
detecting powder in hopper
The pump will not turn on until the
powder level falls below the level
sensor and the delay timer runs out.
Refer to Problem 14 for other
causes