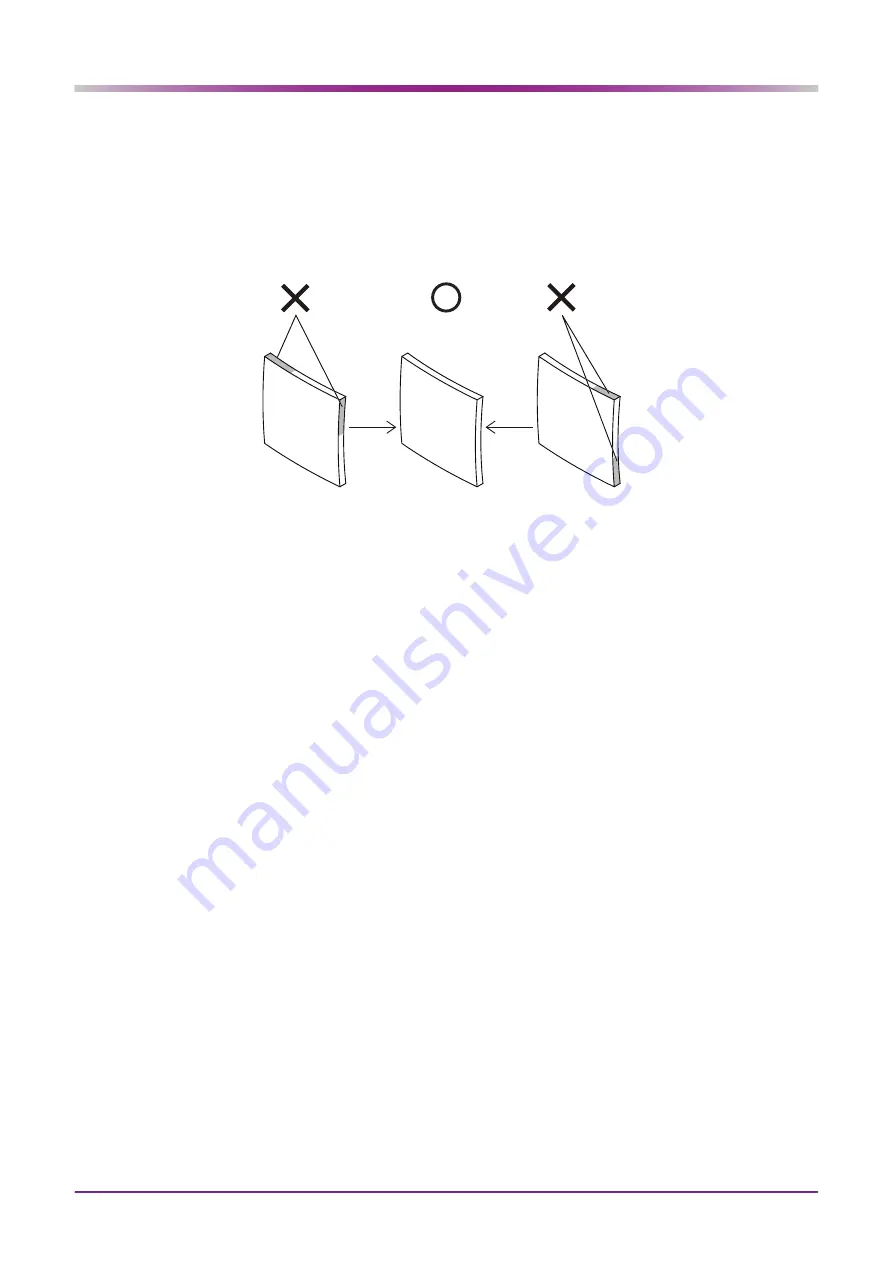
52
CHECK AND ADJUSTMENT PROCEDURES: Polish Axis Check and Adjustment
5
Continue the processing method on the layout screen using the same procedures
explained by the following steps starting from size setting.
to
6
Confirm that there are no unpolished portions or unpolished portions of equal size on
both the right and left surfaces of the lens edge.
7
When the unpolished portions are not equal on both sides of the lens edge, adjust
the Polish axis parameter.
“3.10.2 Polish axis check” (page 53)
Unpolished portions
present
No unpolished portions
present
Unpolished portions
present
Содержание LE-700
Страница 6: ...IV ...
Страница 24: ...18 INSTALLATION Cooling Water and Cleaning Water ...
Страница 78: ...72 CHECK AND ADJUSTMENT PROCEDURES Date and Time Setting ...