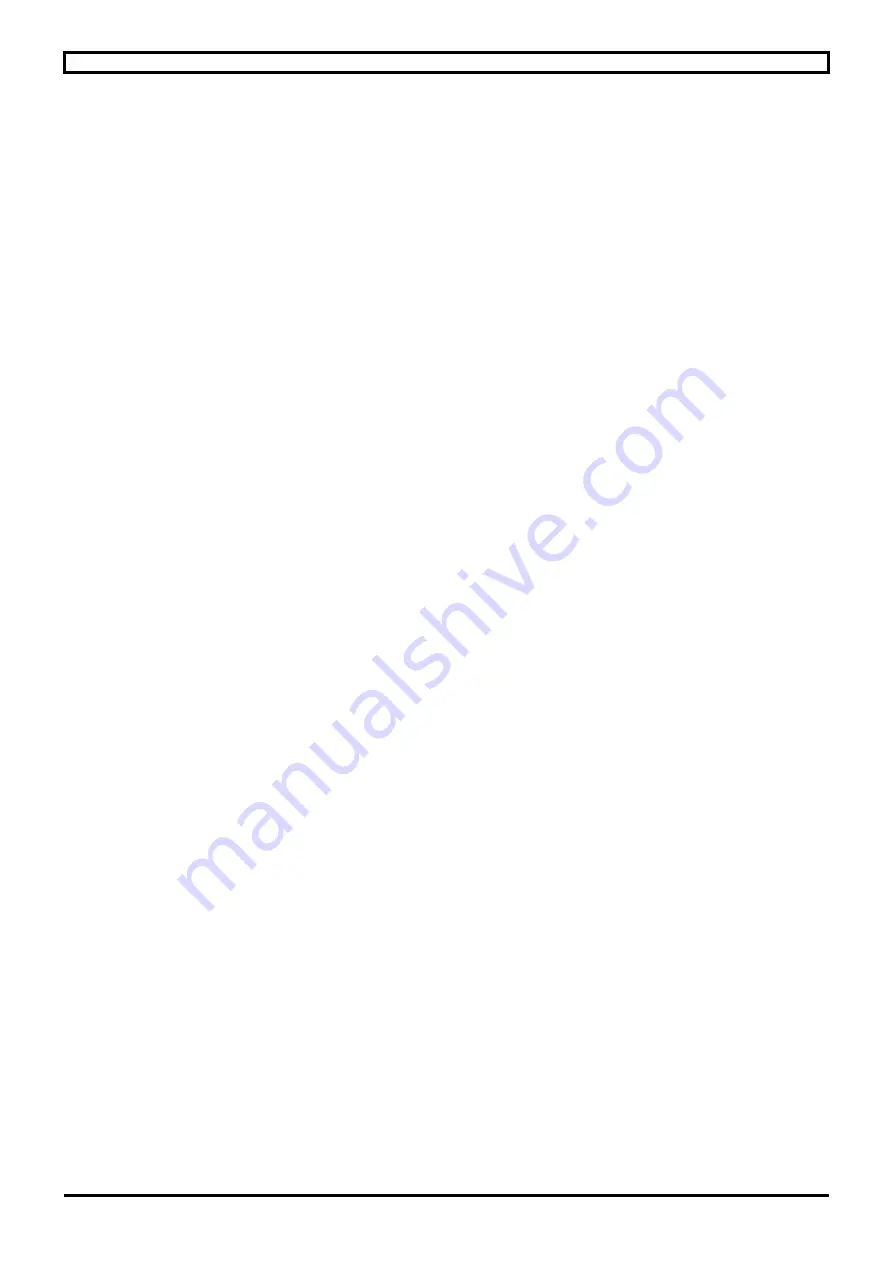
24
GENERAL EMC - HARMONICS - MAINS INTERFERENCE
POWERDRIVE FX Installation guide
4729 en - 2017.08 / c
4.4.2.2 - Presence of commutation notches on the line
When high-power thyristor-controlled equipment is connected
on the same line as the drive, it is essential to ensure that the
harmonics generated by the commutation notches do not
excessively distort the mains voltage and do not create voltage
peaks with amplitude higher than 1.6 x mains Vrms. If this is
the case, it is essential to take corrective measures to
guarantee the mains quality.
4.4.2.3 - Overhead power supply
An overhead power supply is not allowed for the
POWERDRIVE FX
.
4.4.3 - Mains short-circuit power
As with all variable speed drives, the mains short-circuit
power to which the
POWERDRIVE FX
is connected has an
effect on its behaviour. Notably, when the mains short-circuit
power is low, voltage oscillations may appear due to
resonances between the inductive impedance of the mains
and the filtering capacity of the
POWERDRIVE FX
. To avoid
the
POWERDRIVE FX
tripping because of these oscillations,
make sure that the ratio R
sc
= I
sc
/(n x I
L
M) is higher than 50.
Where:
I
sc
: Mains short-circuit current at the point of connection
n: Number of
POWERDRIVE FX
drives connected on the
same power supply line
I
L
M:
POWERDRIVE FX
rated input current
As a matter of course, check that:
•
The sum of the power of all
POWERDRIVE FX
drives
connected to the same transformer does not exceed 35% of
the total transformer rated power.
• The sum of the power of the
POWERDRIVE FX
drives
installed on a generator does not exceed 20% of its rated
power.
4.4.4 - Ground connections
The earth equipotential of some industrial sites is not always
observed. This lack of equipotential leads to leakage currents
which flow via the earth cables (green/yellow), the machine
chassis, the pipework, etc, and also via the electrical
equipment. In some extreme cases, these currents can trip
the drive.
It is essential that the earth network is designed and
implemented by the installation supervisor so that its
impedance is as low as possible, so as to distribute the fault
currents and high-frequency currents without them passing
through electronic equipment.
Metal grounds must be mechanically connected to each other
with the largest possible electrical contact area. Under no
circumstances can the earth connections designed to protect
people, by linking metal grounds to earth via a cable, serve as
a substitute for the ground connections (see IEC 61000-5-2).
The immunity and radio-frequency emission level are directly
linked to the quality of the ground connections.
4.5 - Basic precautions for installation
These are to be taken into account when wiring the cabinet
and any external components. In each paragraph, they are
listed in decreasing order of effect on correct operation of the
installation.
4.5.1 - Wiring inside the cabinet
- Do not run the control cables and the power cables in the
same cable ducts.
- For control cables, use shielded twisted cables.
4.5.2 - Wiring outside the cabinet
- Connect the motor earth terminal directly to that of the
drive.
It is recommended that a shielded symmetrical cable is used:
three phase conductors and coaxial or symmetrical PE
conductor and shielding.
A separate PE protective conductor is mandatory if the
conductivity of the cable shielding is less than 50% of the
conductivity of the phase conductor.
- The shielding must be connected at both ends: drive end
and motor end (completely connected).
- In the second industrial environment, the shielded motor
power supply cable can be replaced by a 3-core + earth cable
placed in a fully enclosed metal conduit (metal cable duct for
example). This metal conduit must be mechanically connected
to the electrical cabinet and the structure supporting the motor.
If the conduit consists of several pieces, these should be
interconnected by braids to ensure earth continuity. The cables
must be fixed securely at the bottom of the conduit.
- There is no need to shield the power supply cables between
the mains supply and the drive.
- Isolate the power cables from the control cables. The power
cables must intersect the other cables at an angle of 90°.
- Isolate sensitive elements (probes, sensors, etc.) from metal
structures which may be shared by the motor support.
Содержание POWERDRIVE FX 100T
Страница 1: ...POWERDRIVE FX Installation guide 4 quadrant Variable speed drive Part number 4729 en 2017 08 c...
Страница 9: ...9 GENERAL INFORMATION POWERDRIVE FX Installation guide 4729 en 2017 08 c Notes...
Страница 15: ...15 MECHANICAL INSTALLATION POWERDRIVE FX Installation guide 4729 en 2017 08 c Notes...
Страница 37: ...37 UL LISTING INFORMATION POWERDRIVE FX Installation guide 4729 en 2017 08 c NOTES...
Страница 38: ...38 UL LISTING INFORMATION POWERDRIVE FX Installation guide 4729 en 2017 08 c NOTES...
Страница 39: ......