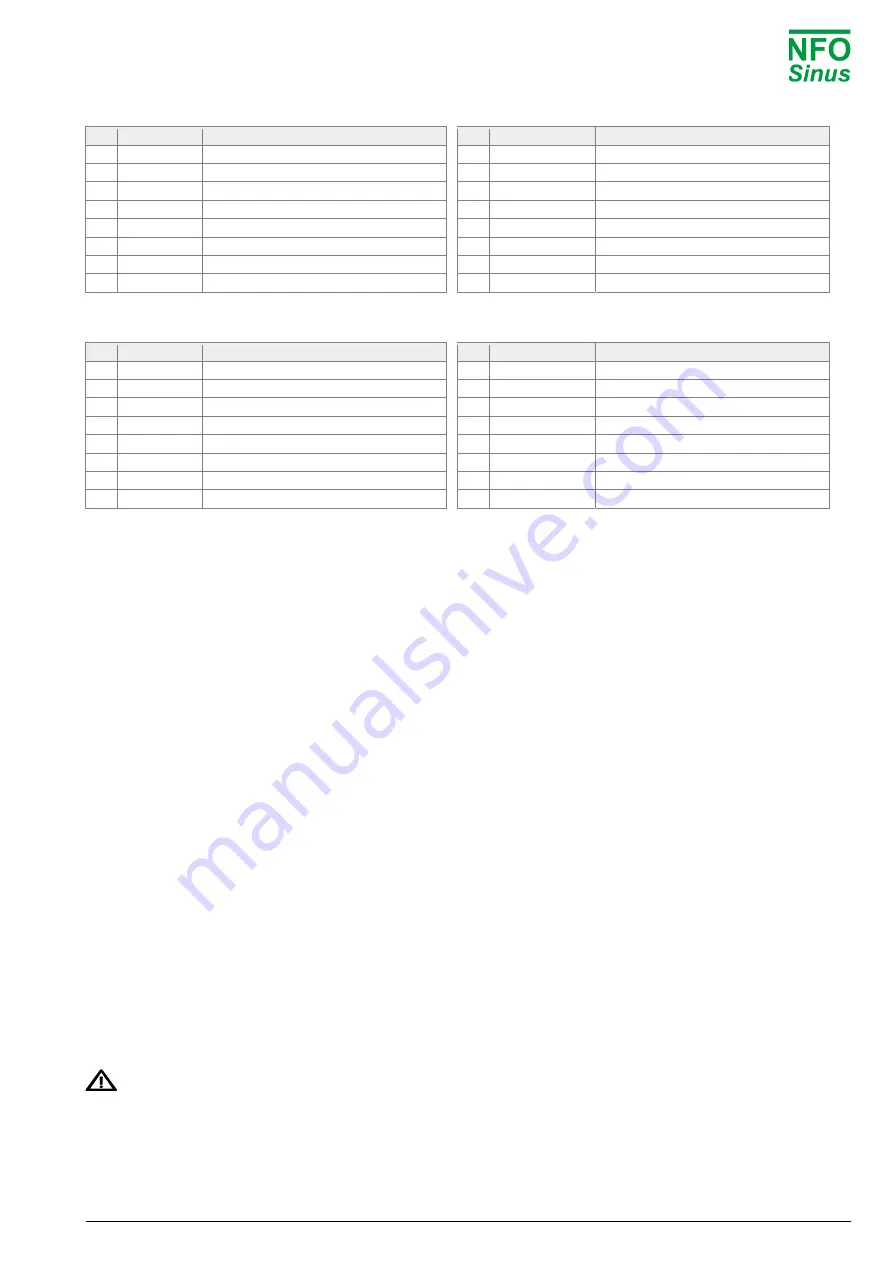
NFO
Drives
AB
2021
201013
‐
2
Operating
and
Installation
Manual
44
Profidrive control bit field description:
Bit Name
Description
Bit Name
Description
0 Switch on
Run command (run signal must be active)
8 Not used
-
1 Not used
(value echoed to drive status bit 4)
9 Not used
-
2 Not used
(value echoed to drive status bit 5)
10 PLC control
PLC takes control (must precede Enable)
3 Enable
Enable command (must precede Run cmd)
11 Not used
-
4 Not used
-
12 Not used
-
5 Not used
-
13 Not used
-
6 Not used
-
14 Not used
-
7 Fault ack
Fault acknowledge on 0 to 1 transition
15 Not used
-
Profidrive status bit field description:
Bit Name
Description
Bit Name
Description
0 Ready
Ready to receive enable command
8 Not used
-
1 Operating
Inverter output stage is active
9 Control requested Inverter is in bus mode
2 Enabled
Enabled, ready to receive run command
10 Setpoint reached Output frequency has reached setpoint
3 Fault active
Fault condition active (may require ack)
11 Limit active
Inverter has reached current limit
4 Not used
(returns value of drive control bit 1)
12 Sleep active
Output is suspended in sleep mode
5 Not used
(returns value of drive control bit 2)
13 Stopmode brake
Inverter will brake/ramp to stop
6 Disabled
Run signal not present on terminal DIN1
14 Reverse
Actual rotation is reverse
7 Alarm active
Alarm condition active (not require ack)
15 Stopping
Inverter is decelerating towards a stop
A communication example could be that master sets the PLC control bit and then waits for inverter to respond with
Control requested bit in status word. Then bus master sets the Enable bit and waits for inverter to respond with
Enabled. Now the bus master may start the motor using the Switch on command bit, and inverter will respond with
bit Operating.
When master clears the Switch on bit, inverter will decelerate towards a stop. When fully stopped, the Operating bit
will be cleared. Motor is now stopped and inverter is ready for a new start command. For other status bits and their
meaning, see table above.
Please contact NFO Drives AB for Profinet/Profibus setup files (gsdml/gsd format).
8
Brake chopper and power surge regulator
If the inverter is trying to decelerate a motor with a high load inertia, energy is fed back to the inverter. This causes
the voltage in the internal DC stage (power ter and -) to rise. To prevent the voltage rising too high and
damaging the inverter, a surge regulator limits the deceleration.
If the regulator limits the deceleration too much (taking longer time than parameter
Decel
), an external brake
resistor must be installed to convert the regenerated energy into heat. This resistor is mounted between power
ter and B (see Table 4 and Fig.1). When the brake chopper is active, it appears as an indication on the
display.
NOTE: The resistor’s power handling capacity must be dimensioned to absorb the generated excess energy from
the rotating load. Recommended resistance for inverters with 3 x 400V power supply is 100 – 300
. If the
resistance is too low, the brake chopper circuit may be damaged. The resistor must also be low-inductive in order
not to damage the brake chopper circuit.
If the retardation time is less than 5 sec, an external brake resistor must be installed. Avoid setting
the retardation ramp (parameter
Decelerate
) any shorter than necessary.
If in any doubt regarding how to install this type of equipment, always contact NFO Drives AB.
3006469-2022-04