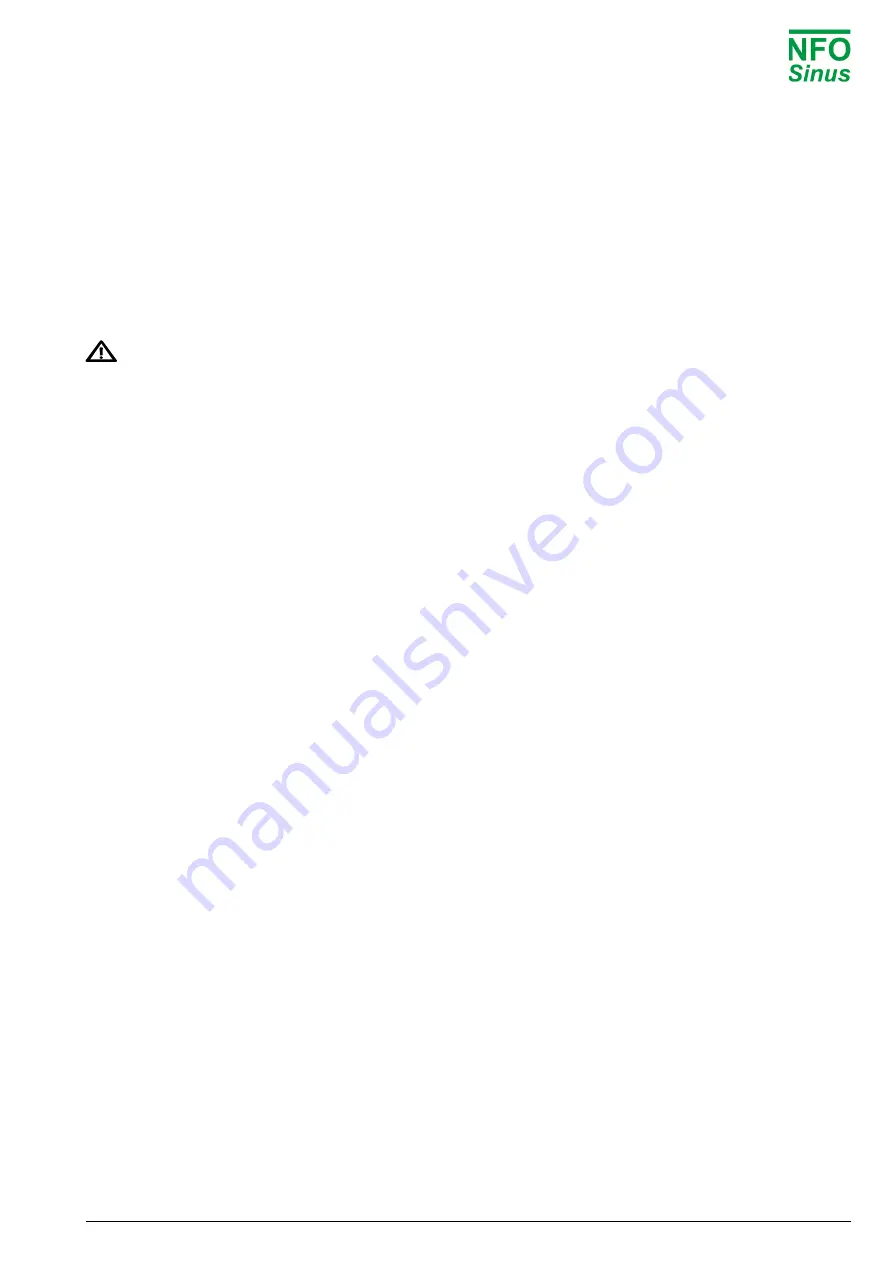
NFO
Drives
AB
2021
201013
‐
2
Operating
and
Installation
Manual
27
5.8.3 Stop
mode
The NFO Sinus has two different stop modes,
Brake
and
Release
.
With the
Stop Mode
parameter set to
Brake
(default setting) and issuing the stop command, the inverter will slow
the motor down to a stop using the set deceleration ramp.
With the
Stop Mode
parameter set to
Release
, the stop command will release the motor immediately, letting it run
down to an uncontrolled stop. The motor will also be released in the event of a detected fault.
After releasing the motor, the NFO Sinus will wait a certain minimum time before accepting a new RUN signal. The
time is proportional to the frequency at which the motor was released. This function is used to minimize the risk of
restarting with a rotating load, which could lead to output current surges and failure of the drive.
Avoid allowing a load with high inertial torque to run down uncontrolled as this could destroy the
inverter through a large voltage surge generated by the motor.
5.8.4 Energy save function
The energy save function optimizes the energy consumption of the motor by lowering the magnetizing current at
low loads.
It is mainly used for applications at low loads, e.g. fans that sometimes run at low speed. The
magnetizing current is at maximum lowered to 25% of I-magn. The time for the function to adjust optimal
magnetizing current is approx. 5s at a change in setpoint or load. As a result of this, the function should only be
used in applications not requiring high dynamics.
5.8.5 Power On, Start and Stop delay
PowerOn Delay
sets the time from when inverter is powered until it accepts a start command.
PowerOn Delay
can
be useful to handle short time power failures (interrupts) and restarting when operating with large inertial torque,
such as a fan rotor.
Start Delay
can be used to supress short pulses of the RUN signal, thereby requiring a minimum duration of the
RUN signal before actually starting the motor.
Stop Delay
can be used to setup a minimum required stand-off time between the point when the motor has come to
a stop, and when the inverter accepts a new RUN signal. This may be used for heavy rotating loads or when the
driven system requires a minimum stop time before it may be restarted.
5.8.6 Motor
brake,
DC-Brake
When starting a rotary load (such as a fan rotor with natural draught), it may happen that the inverter cannot get
control of the motor, and indicates a
Run Fail
alarm. To handle such starts, the inverter is equipped with a DC
brake function. This function slows the motor down with the help of a DC current for a set period of time, after which
the motor will then start. The parameter
DC-Brake
is set to the time needed to stop the motor when it is rotating at
its fastest. The size of the brake current is adjusted to the motor's nominal current.
5.8.7 Speed
regulator,
Kp-speed
and
Ti-speed
The inverter is equipped with a PI-type speed or frequency regulator to ensure the rotor is at the desired rpm (mode
Speed
) or frequency (mode
Freque
) at all times and under all loads (up to maximum torque). The regulator
performance can be set via parameters
Kp-speed
and
Ti-speed
if required. The proportional amplification (
Kp-
speed
) handles fast control inputs changes (rapid changes in speed), while the I amplifier (
Ti-speed
) is responsible
for fine-tuning the final speed.
3006469-2022-04