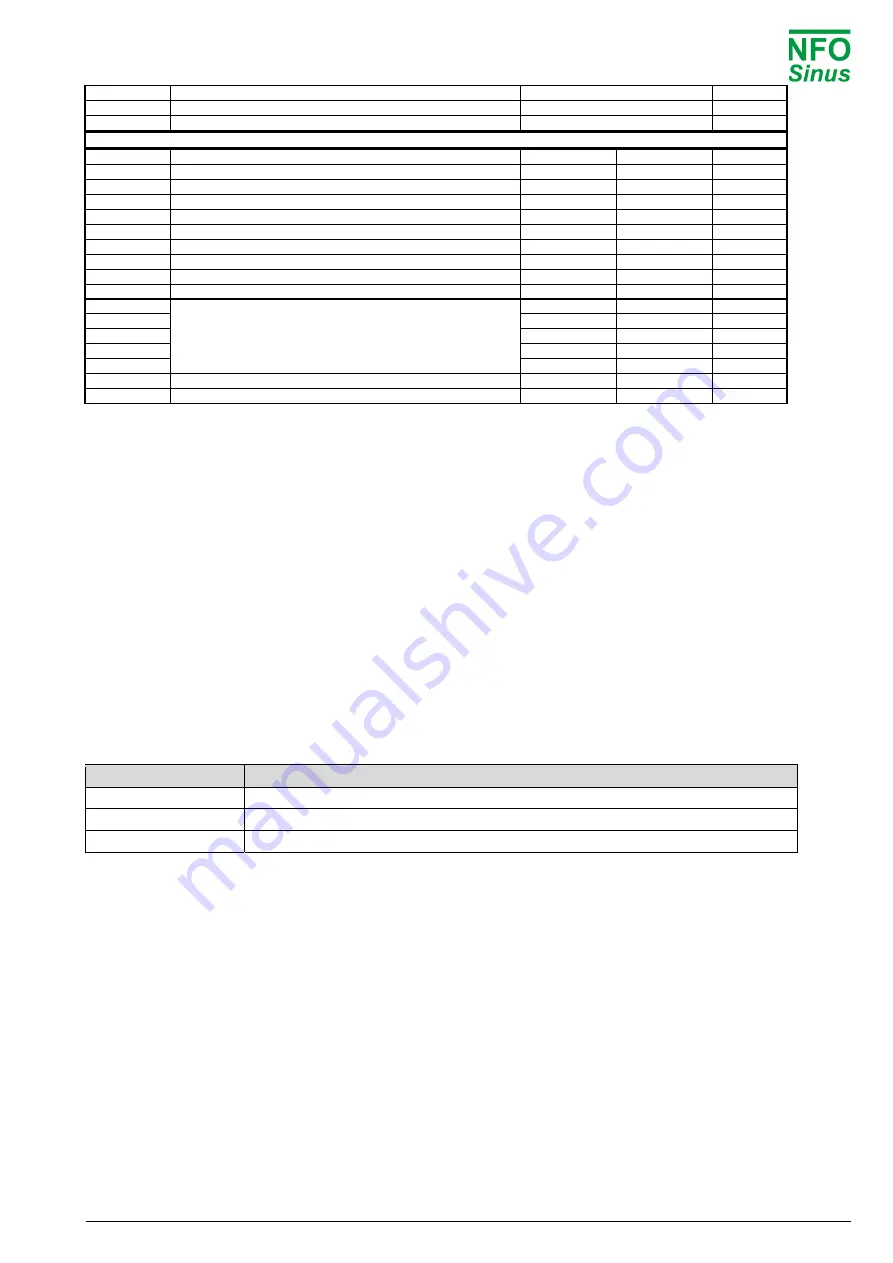
NFO
Drives
AB
2021
201013
‐
2
Operating
and
Installation
Manual
24
GUI version Firmware version of user interface
-
Read
Prod.date
Production date and time
YYMMDDHHMM
Read
Serial nbr Serial
number [10
digits]
Read
Error
Error log
Internal log of faults and alarms
Read
Restart Delay Time from when fault disappears to restart
10 sec
0 – 3600 sec
Stby/Run
Reset Time Time inverter must run fault free to reset individual error counters
600 sec
0 – 3600 sec
Stby/Run
AC Fail
Phase error
Temp Hi
Heatsink overheating
PTC Temp Motor overheating
Overload
Electronic motor overload protection
Ain Fail
Analogue setpoint input signal out of range
DC Low
Voltage in DC link too low
DC High
Voltage in DC link too high
GND Fail
Fault in motor or motor wiring
Short Circuit
IMagn Low
Current Low
Current High
Current Limit Motor overcurrent
Run Fail
Rotor locked, start failure
Table 10. Parameters available, sorted by parameter group
Notes:
[1]
Type = Standby parameters can only be changed when motor is standby (not running).
Type = Stby/Run parameters can be changed in both standby and run.
Type = Read
parameters are read-only.
[2]
Other combinations of default values for Acceleration, Deceleration, Kp-speed and Ti-speed are available.
[3]
Available in future versions.
[4]
Value for indicative purpose only as measurement has limited accuracy.
5.6 Select
application
First time powered up after installation, or after performing a factory reset of parameters, the installer will be
prompted to select application type for the inverter. The purpose of selecting application is to preset acceleration
and deceleration ramps to a value suitable for the application in question. Please note that the preset values are a
merely suggested general values. Depending on other operating conditions, the installer may have to further adjust
the accel/decel ramps.
Application
Description
Pump
Set acceleration and deceleration ramps suitable for general pump applications
Ventilation / other
Set acceleration and deceleration ramps suitable for ventilation fan applications
OEM vacuum pump
To be used
only
with OEM vacuum pump application
5.7 Autotuning and motor parameters
There are three alternatives for autotuning the motor parameters: Full tuning, Basic tuning or Calculated tuning. Full
tuning is preferred whenever possible.
Before running autotuning, the nominal motor data has to be entered. It consists of parameters
P-nom, U-Nom,
f-Nom, N-Nom, I-Nom
and
cos
. These are shown on the motor plate and must be entered according to the
connection used; i.e. Y (star) or D (delta), including any possible 50 / 60Hz option for the motor. The default
nominal data settings as supplied are shown in Table 11.
To achieve optimal motor control, the inverter must have a correct set of parameters
R-stat, R-rot, L-main, Sigma,
I-magn
and
I-limit
. The autotuning functionality measures and calculates these motor parameters, taking into
account the cables, etc. between inverter and motor, and ensures best possible control of the motor. Autotuning
shall
always
be performed, even if a standard motor is used.
3006469-2022-04