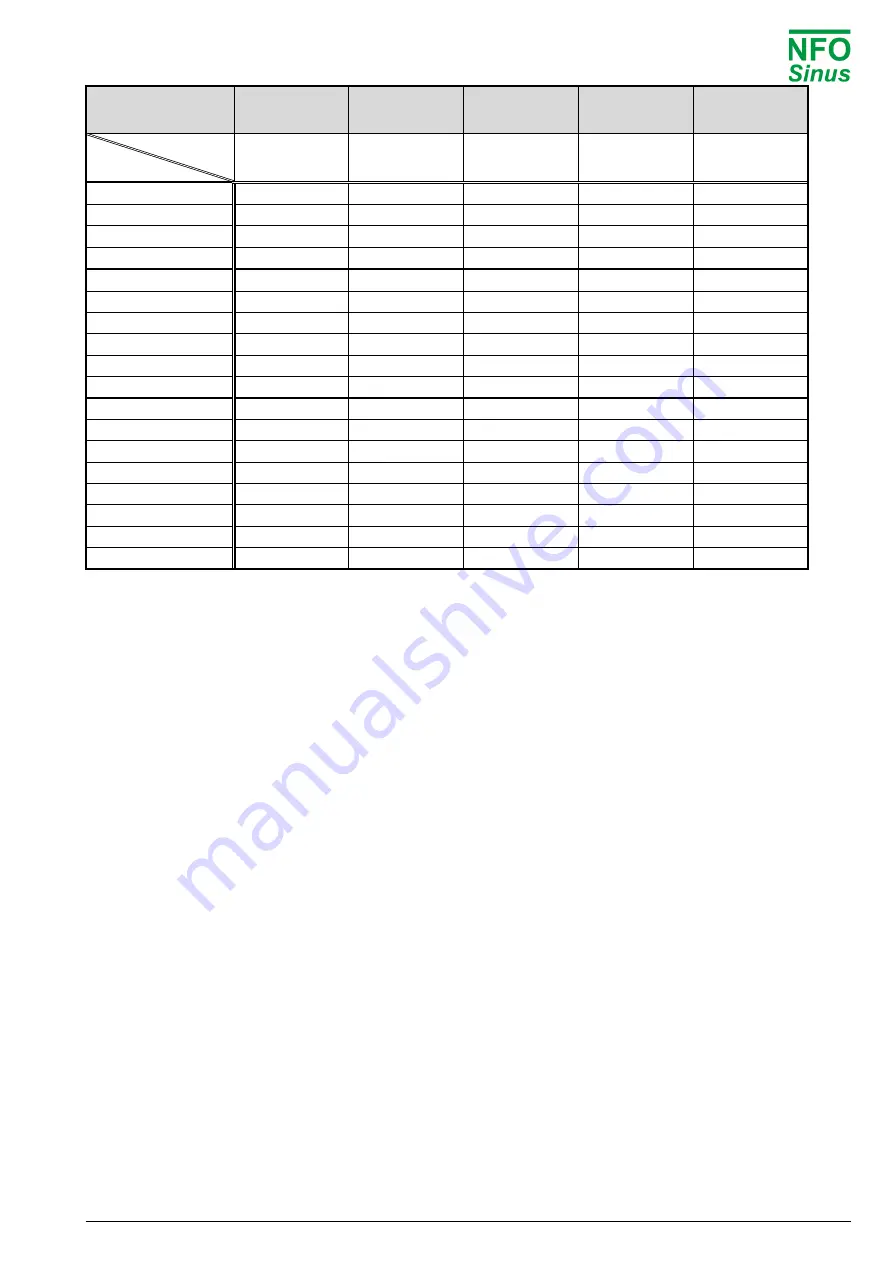
NFO
Drives
AB
2021
201013
‐
2
Operating
and
Installation
Manual
34
Function Analog select
Direction
Select A
Select B
Select C
Terminal
Function
DIN2 DIN3 DIN5 DIN6 DIN7
Analog 1 Forward
0
0
0
0
0
Analog 1 Reverse
0
1
0
0
0
Analog 2 Forward
1
0
0
0
0
Analog 2 Reverse
1
1
0
0
0
Fix Reg 1 Forward
x
0
1
0
0
Fix Reg 1 Reverse
x
1
1
0
0
Fix Reg 2 Forward
x
0
0
1
0
Fix Reg 2 Reverse
x
1
0
1
0
Fix Reg 3 Forward
x
0
1
1
0
Fix Reg 3 Reverse
x
1
1
1
0
Fix Reg 4 Forward
x
0
0
0
1
Fix Reg 4 Reverse
x
1
0
0
1
Fix Reg 5 Forward
x
0
1
0
1
Fix Reg 5 Reverse
x
1
1
0
1
Fix Reg 6 Forward
x
0
0
1
1
Fix Reg 6 Reverse
x
1
0
1
1
Fix Reg 7 Forward
x
0
1
1
1
Fix Reg 7 Reverse
x
1
1
1
1
Table 17. Selected setpoint source for
PI Reg / Op Mode (Setp Source)
=
Terminal
There are seven parameters available for fixed regulator setpoints,
R-fix1
to
R-fix7
. These can be set in the range
-2000.0 – 2000.0. Units are selected via the parameter
Unit
.
5.11.2 Regulator setting, Reg Amp, Reg Kp and Reg Ti
The process control error, which is calculated as setpoint minus actual value, is converted from process regulator
unit to the actual control mode (Frequency or Speed) with the factor
Reg Amp * Max Ain / Act Max
.
Reg Amp
can
be set to 1 (a positive or increasing value of the output signal if the regulator setpoint is greater than the current
actual value) or -1 (a negative or decreasing value of the output signal if the regulator setpoint is greater than the
current actual value).
The proportional regulator component affects the output signal directly.
Reg Kp
amplifies the proportional regulator
component and can be set within the range 0.00 to 1.00. Setting
Reg Kp
= 0 eliminates the proportional component
completely, giving a purely integrative regulator.
The regulator integration time
Reg Ti
is a time constant which governs the rate at which the regulator output signal
changes at a given control error.
RegTi
can be set in the range 1.0 to 200.0 seconds, where the value 200.0
eliminates the integrator component completely, giving a purely proportional regulator.
5.12 Motor safety functions
The NFO Sinus is fitted with two different motor safety functions: a thermistor sensor input and electronic motor
overload protection which calculates the motor's approximate winding temperature continuously.
5.12.1 PTC input
If the motor is fitted with PTC thermistor(s) or thermo-contact (Klixon), these can be connected directly to the
inverter. This is done between terminal 8 (DIN8) and terminal 11, 12, 30 or 31 (0V) as in Fig.1. Jumper J802 (PTC)
must be mounted in position “ON” to enable the function.
3006469-2022-04