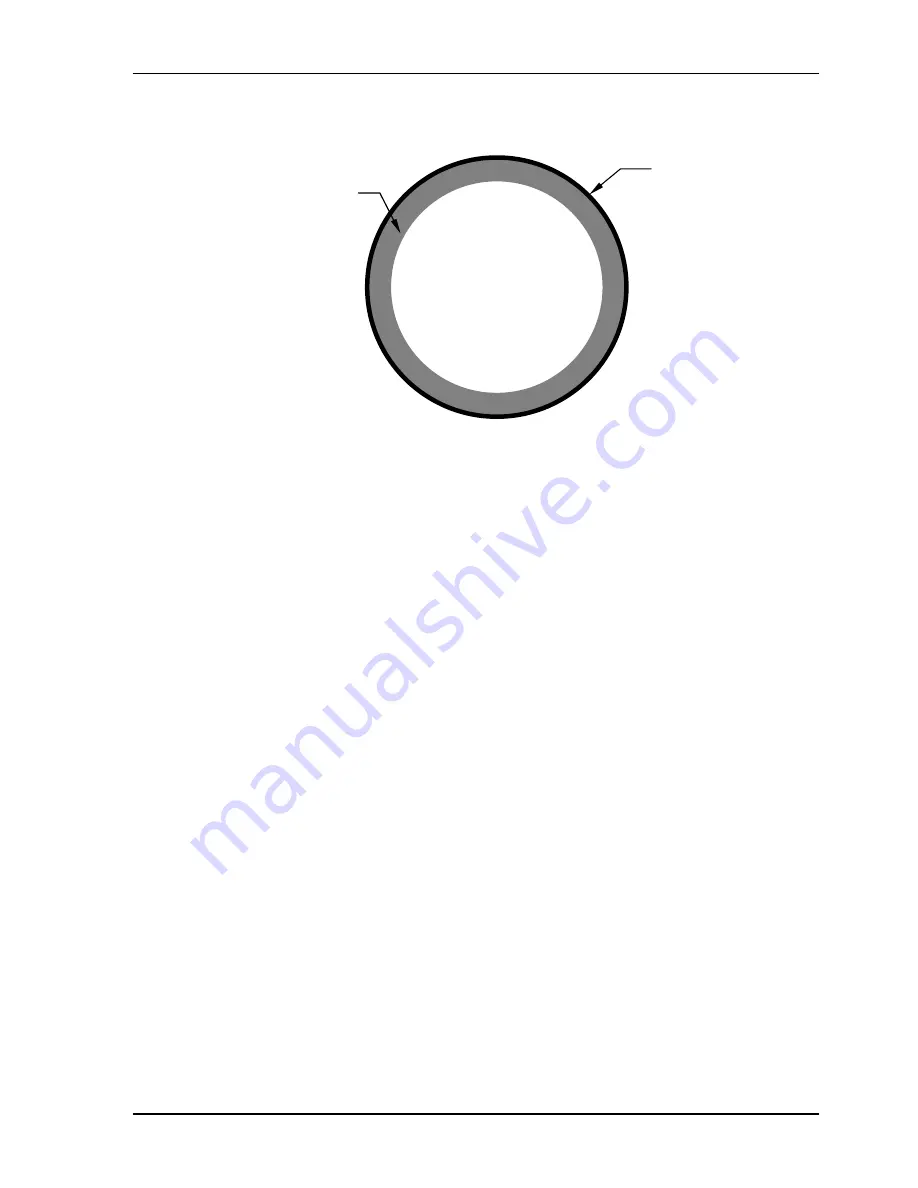
29
New Brunswick Scientific
User’s Guide
Figure 10: Water Jacket Guard Installation (top view)
5.
With the gradations marked on the glass facing front (toward the user),
slide the vessel into the bottom clamping ring, until it rests securely against
the base plate.
Make sure the water inlet tube stands free
(not kinked)
inside the water jacket.
6.
Finger tighten the six knurled thumb screws, to securely attach the
clamping ring to the base plate. This seals the water jacket.
4.8.3
Filling the Water Jacket
To fill the water jacket:
1.
After the tubing and water supply are connected, make sure the solenoid
valve cable and the RTD cable are plugged into the Power Controller.
2.
Set the temperature control mode to
Off
.
3.
Check that the temperature reading is higher than 5ºC.
4.
Allow water to enter the piping system; it will stop at the solenoid valve.
5.
Set the temperature loop control mode to
Auto
.
6.
Enter a temperature setpoint (
SP
) that is at least 12ºC below the current
value (
CV
). The controller will respond to the call for cooling by
opening the solenoid valve, filling the jacket with water.
4.8.4
Install Baffle (14.0L Fermentation Vessels ONLY)
For installation of the 1.3L, 3.0L & 7.5L vessel baffle, see Section 4.8.21.
If you are using a 14.0L vessel
, install the baffle assembly inside the glass
vessel:
Bottom
Vessel
Flange
Rubber Gasket
M1155-9902 (1.3L & 3.0L)
M1227-9903 (7.5L & 14.0L)
Содержание BioFlo CelliGen 115
Страница 2: ...ii BioFlo CelliGen 115 M1369 0050 User s Guide...
Страница 61: ...49 New Brunswick Scientific User s Guide...
Страница 154: ...142 BioFlo CelliGen 115 y M1369 0050 User s Guide...