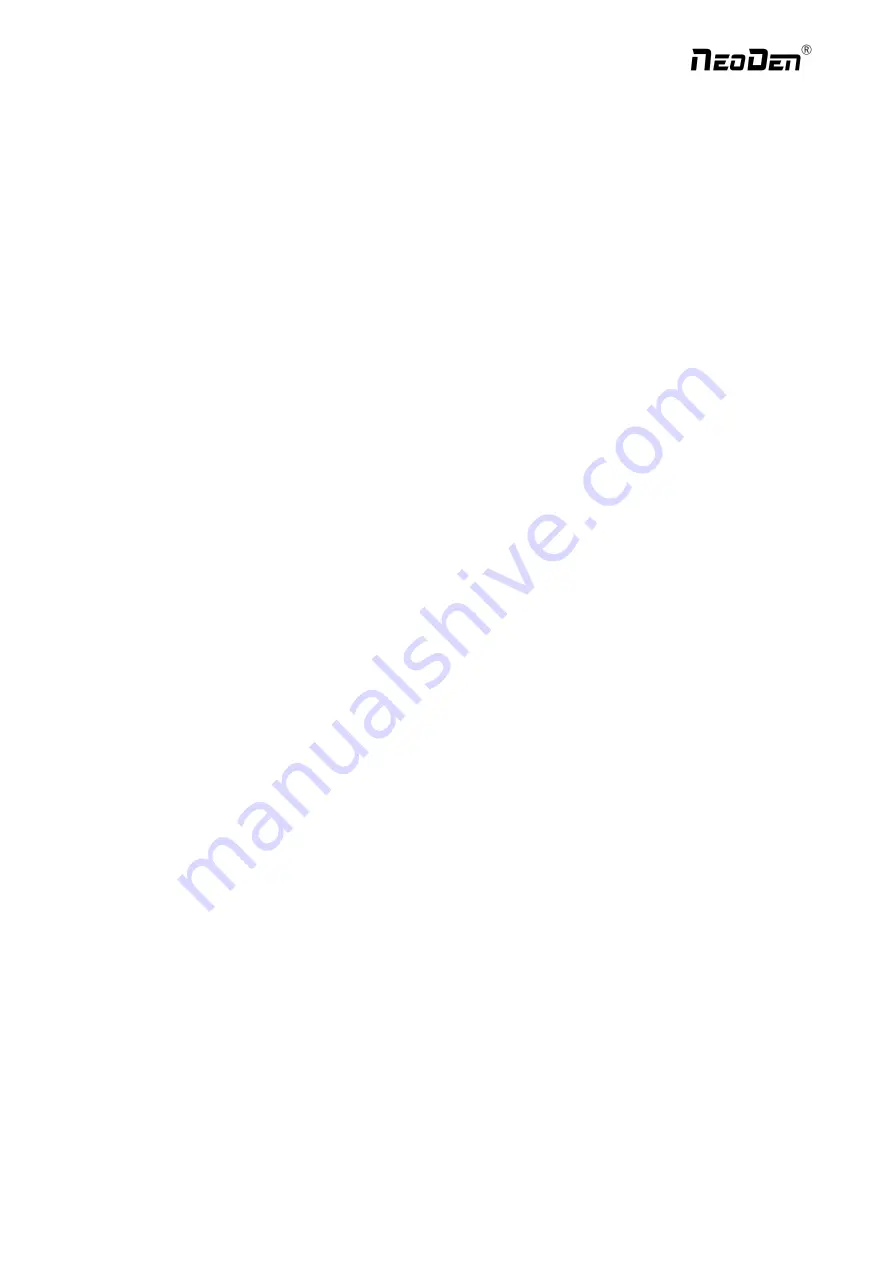
2.1.2 Tracks:
Select the “Tracks”on PCB Feed Setting interface:
Tracks width setting:Set correct PCB width value until the PCB can move smoothly
PCB Feed Test:Put PCB to “Tracks Section 1”,Click “forward”, PCB will move to “Tracks section 2” and stop at the
cylinder thimble position through the sensor,cylinder will raise the PCB, then thimble will go down, PCB feeding complete.
The adjustment method of the tracks width:Put the PCB on the front conveyor,feed the PCB to the tracks of pick and place
machine, gently push the PCB back and forth by hand to leave a tiny gap of about 1mm in the rail(add extra 1mm from PCB
width), click”Width set” and follow the prompt window to check whether meet the zero return condition. After zero return,
it will be adjusted to setted width.
2.1.3 Long Tracks:
Select the “Long Tracks”on PCB Feed Setting interface,then all track sections start work simultaneously.
Tracks width setting:Set correct PCB width value until the PCB can move smoothly
PCB Feed Test:The long tracks sends feed signal to the front conveyor, and feed PCB to cylinder thimble 1 position,
cylinder will raise the PCB,then thimble 1 will go down,PCB feeding phase 1 is completed.After above placement is
completed, the PCB in the waiting area is released, feed to cylinder thimble 2 position, cylinder will raise the PCB,then
thimble 2 will go down,PCB feeding phase 2 is completed.After above placement is completed, the PCB in the waiting area
is released, feed to cylinder thimble 3 position, cylinder will raise the PCB,then thimble 3 will go down,PCB feeding phase
3 is completed.
2.2 PCB Eject setting
After click “Eject”no matter under Mag fixture or Rail mode,the thimble will go down in “track section 2”,”track section
3”begin to work and PCB will feed to back conveyor
2.3 PCB Forward Position Setting
Need set the PCB forward position before click “forward”
Step:Click “Align”and enter the “align”interface,set the forward position according to the photo took by mark camera,and
select “align method-nozzle 1”,then click “save”to save the forward position information.
13
Zhejiang
NeoDen Technology Co.,Ltd.
Содержание K1830
Страница 6: ...1 3Working Area Structure Figure 3 Top view of main mounting area 6 Zhejiang NeoDen Technology Co Ltd ...
Страница 7: ...Figure 4 X axis Beam Figure 5 Main Placement Head Camera 7 Zhejiang NeoDen Technology Co Ltd ...
Страница 35: ...8 2 Component Positions Setup 35 Zhejiang NeoDen Technology Co Ltd ...
Страница 44: ...11 Structure and maintenance instruction 11 1 Feeder Brief Introduction 44 Zhejiang NeoDen Technology Co Ltd ...