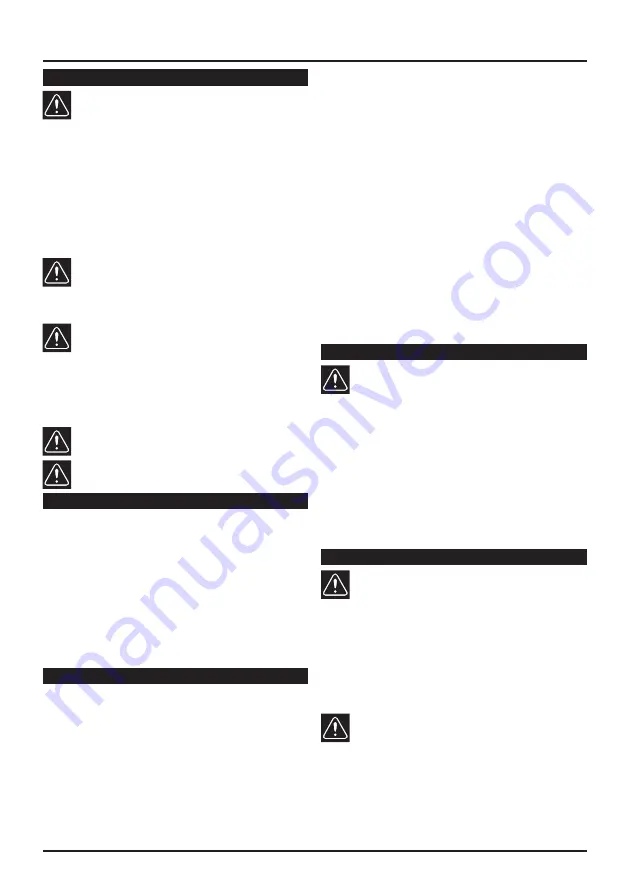
English
17
Grinding or cutting wheel fixing
Attention! Prior to handling the accessories, the pow-
er supply cable has always to be disconnected from
the power source socket!
Mounting with the standard clamping nut
Clean the bottom flange (13) and the clamping nut (16) as well as
the clamping surfaces of the grinding or cutting wheel. Place the
bottom flange (13) (by the recess out) on the spindle (7). Place the
grinding (14) or cutting wheel (15). The bottom flange recess (16)
must be inserted precisely into the grinding wheel (14) or the cut-
ting wheel (15) hole. Then put the clamping nut (16) on the spindle
(7) so that when fixing the grinding wheel (14), the clamping nut
recess (19) must be faced towards the wheel and when fixing the
cutting wheel (15), the clamping nut recess (19) must be directed
from the wheel!
Depress the lock spindle pin (4).
Attention! Use the lock spindle pin only if the spindle
is at rest and the grinder is de-energized.
Swivel the wheel /spindle, until the lock spindle pin (4) is engaged.
Tighten the clamping nut (16) firmly, using the wrench (17). Prior
to start the grinder verify that the wheel does not rotate freely.
Attention! Prior to starting the grinder, verify that the
wheel does not rotate freely between the bottom
flange/the autobalancer and the clamping nut.
Mounting with quick-clamping nut
The quick-clamping nut must be tightened or loosened by hand
only (never use any additional tool!). Mounting of the grinding or
cutting wheel is the same like for the grinder without the quick-
clamping nut, with the sole difference, that after spindle locking
the quick-clamping nut (18) may be tightened by hand only.
Attention! Do not tighten the quick-clamping nut
without the wheel not to damage its mechanism!
Attention! Prior to starting the grinder, verify that the
wheel does not rotate freely between the bottom
flange/the autobalancer and the clamping nut.
Putting into operation
Check whether the data on the rating plate match with the real
power supply voltage. The tool intended for 230 V~ may be also
connected to 220/240 V~. Check whether the plug type corre-
sponds to the socket type.
Switching on- off
Push the safety lock-off lever (2) forwards to release the On/Off
switch lever (1). At the same time, press the on-off switch lever (1)
to start the grinder and release it to stop.
Continuous operation
Push the safety lock-off lever (2) forwards to release the On/Off
switch lever (1). At the same time, press the on-off switch lever (1)
and push the safety lock-off lever (2) forwards. To turn off continu-
ous operation, press and release the on-off switch (1) again.
Motor electronics
Increases productivity, service life of the grinding machine, com-
fort at work, quality and safety of labour. Its features are as follows:
Restart protection
If power supply is interrupted at work (disconnection of the supply
cable plug, tripping, cutout, etc.) and the switch remains arrested
in the ON position, after resumption of power supply the machine
will not be restarted automatically. To start the grinding machine,
the switch has to be switched OFF at first and ON afterwards.
Smooth starting
After the grinding machine is switched ON, the control electron-
ics guarantees smooth start and running up to the working speed
without unnecessary shocks. This way service life of the grinding
machine may be extended and wear of the gear reduced.
Constant speed
Speed of this grinding machine is constant under the standard
load (under absolute load relief alike); this way productivity of la-
bour under load does not drop. Note: Thanks to speed reduction
during no-load operation the noise exposure is reduced as well.
Motor protection from burnout
The control electronics measures motor temperature continuously,
thus preventing its burnout. If the motor temperature is danger-
ously high, the machine will be switched to the cooling mode au-
tomatically. Do not work with the grinding machine in this state.
If you work with the overloaded grinding machine, the control
electronics will switch the motor OFF. If you switch the overloaded
grinding machine OFF and ON immediately afterwards, the ma-
chine will at first be started to the full operating load and after ca
2 seconds it will be switched to the cooling mode again. Let motor
cool at the “cooling” speed. Cooling lasts ca 1 minute as a rule. The
machine then returns back to the full working speed and you can
continue working.
Protection from wheel lock
When cutting, the wheel can be locked in the cut. To eliminate the
risk of operator’s injury or machine burnout, the electronics reacts
to steep load rise by switching the motor OFF. The stopped motor
cannot be rotated and a quiet droning can be heard. To restart the
machine, switch it OFF and ON afterwards.
Grinding and cutting discs
Check that the label on the disc shows the permissible
peripheral speed or permissible revolution speed. If
the permissible revolution speed is given on the disc,
it must not be lower than the highest no-load speed of the
grinder.
Discs with a permissible peripheral speed of 80 m/s and higher
may be used.
Test new cutting discs by letting them run for about one min-
ute with no load.
Unbalanced or vibrating discs should not be used and should be
discarded.
Protect grinding discs from shock, impact and lubricants.
If the grinding and cutting wheels are worn down to the mark on
the wheel guard (see the arrow sign), they should be replaced with
new ones. This maintains the optimum grinding and cutting per-
formance of the machine (peripheral speed of the grinding and
cutting wheels).
Maintenance and service
Attention! Risk of el. shock. Prior to start any opera-
tion, pull the plug out of the socket!
Vent holes (3) of the motor guard may not be covered.
Cable replacement must be carried out by a specialized service sta-
tion authorized correspondingly.
After ca 200 hours of operation the following activities and
works have to be carried out:
Check of brush length. The brushes shorter than 5 mm have to be
replaced for new ones.
The grinder will be stopped automatically if the brushes are worn.
The grinder is sent to the service station for maintenance.
Grease replacement in gearbox and bearings.
Attention! With respect to protection from el. shock
and preservation of the class of protection, all mainte-
nance and service operations requesting jig saw case
removal must be performed by the authorized service centre
only!
The current list of authorized service centres can be found at our
website
www.narex.cz
, section
“Service Centres”
.
Содержание EBU 23-24
Страница 3: ...3 EBU 23 24 EBU 23 26 A 1 2 3 4 5 6 7 8 9a 10 13 14 15 9b 10 11 11 12 16 17 18 19 20 21 22...
Страница 29: ...29 1 2 a RCD RCD 3 a 4 a 5 a...
Страница 30: ...o 30 a a...
Страница 31: ...31...
Страница 33: ...33 21 22 13 16 13 7 14 15 16 14 15 16 7 14 19 15 19 4 4 16 17 18 230 220 240 2 1 1 2 1 1 2 1 2 1 80 1...
Страница 45: ...45...
Страница 46: ...46...
Страница 47: ...47...