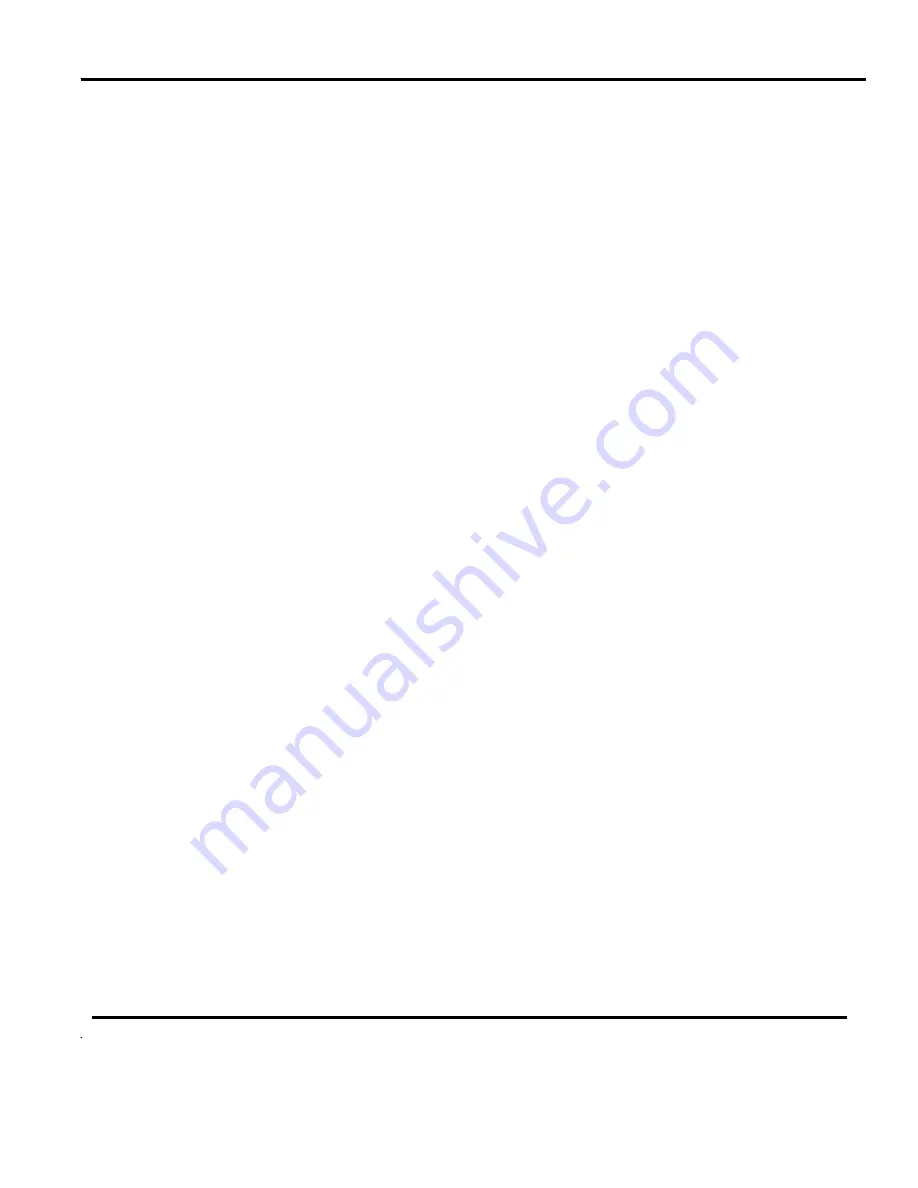
CHAPTER 2: INSTALLATION
MODEL 250DP DUAL PULSE
RESISTANCE WELDING POWER SUPPLY
990-280
2-5
Air Actuated Weld Head Connections
Solenoid valve/regulator assemblies which are not mounted on the weld head should be located as close as
possible to the weld head. Use the
shortest
air lines possible to obtain the fastest mechanical response.
Connect the inlet port on the air valve (solenoid) to a
properly filtered air supply
(100 psig maximum). Use
0.25-inch OD plastic hose with a rated burst pressure of 250 psi to connect the outlet ports of the
solenoid/regulator assembly to the flow controls on the air cylinders. Figure 2-4 illustrates a typical single
regulator installation for a Unitek Peco Series 80 Weld Head. Turn the regulator(s) fully counter-clockwise
to ensure minimum air pressure. Turn on the air supply. Repair leaks if necessary.
All Thinline weld heads are capable of cycling at a rate of 1 weld per second,
provided that the tubing
between pressure regulators and the air cylinder is kept as short as possible.
Increasing the length of the
tubing produces very sluggish mechanical motion.
Do not use lubrication on the input air line
because, as
the internal seals on the air cylinder wear, lubricating oil will leak past these seals and contaminate the
electrode and the workpiece with a fine oil mist. Once every six months or every 1 million operations,
whichever occurs first, remove the top flow control valve and place two drops of light machine oil in the top
of the air cylinder.