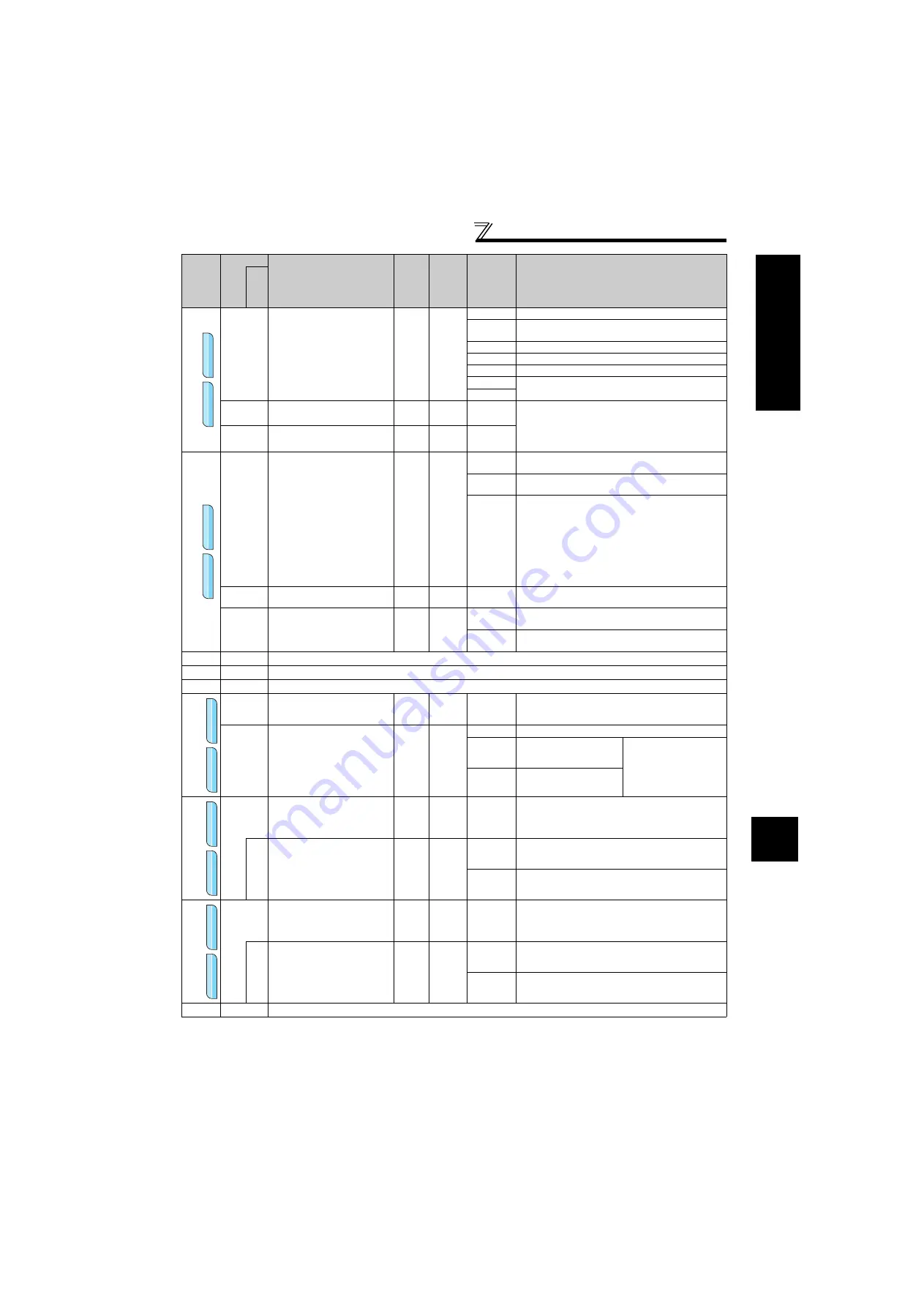
135
To
rque com
m
and sourc
e
s
e
le
ct
ion
804
Torque command source
selection
1
0
0
Torque command by terminal 1 analog input
1
Torque command by parameter
Pr.805
or
Pr.806
setting (-400% to 400%)
2
Torque command using pulse train input (FR-A7AL)
3
Torque command by using CC-Link (FR-A7NC)
4
Digital input from the option (FR-A7AX)
5
Torque command by using CC-Link (FR-A7NC)
6
805
Torque command value
(RAM)
1%
1000%
600 to
1400%
Digital setting of the torque command can be made
by setting
Pr. 805
or
Pr. 806
. (Setting from
communication option, etc. can be made.)
In this case, set the speed limit value to an
appropriate value to prevent overspeed.
806
Torque command value
(RAM,EEPROM)
1%
1000%
600 to
1400%
S
peed l
im
it
807
Speed limit selection
1
0
0
Use the speed command value during speed control
as speed limit.
1
According to
Pr. 808
and
Pr. 809
, set the speed limit in
forward and reverse rotation directions individually.
2
The analog voltage of the terminal 1 input is used to
make speed limit. For 0 to 10V input, set the forward
rotation speed limit. (The reverse rotation speed limit
is
Pr. 1
Maximum frequency
)
For -10 to 0V input, set the reverse rotation speed
limit. (The forward rotation speed limit is
Pr. 1
Maximum frequency
.) The maximum frequency of both
the forward and reverse rotations is
Pr. 1
Maximum
frequency
.
808
Forward rotation speed limit
0.01Hz
60Hz
0 to 120Hz
Set the speed limit level during forward rotation.
(valid when
Pr. 807
= 1)
809
Reverse rotation speed limit
0.01Hz
9999
0 to 120Hz
Set the speed limit level during reverse rotation.
(valid when
Pr. 807
= 1)
9999
The setting is the same as that of the torque limit in
the forward rotation direction.
—
810
Refer to
Pr. 22
.
—
811
Refer to
Pr. 22
and
Pr. 37
.
—
812 to 817
Refer to
Pr. 22
.
E
a
sy gai
n
tuning selec
tion
818
Easy gain tuning response
level setting
1
2
1 to 15
1 : Slow response
↓
15 : Fast response
819
Easy gain tuning selection
1
0
0
No tuning
1
With load estimation
(only under vector control)
The optimum gain is
automatically set from the
torque command and
speed during motor
operation.
2
Manual input of load (
Pr.
880
)
S
peed
loop
proport
ion
al
gain s
e
tt
ing
820
Speed control P gain 1
1%
60%
0 to 1000%
Set the proportional gain for speed control.
(Increasing the value improves trackability in
response to a speed command change and reduces
speed variation with disturbance.)
830
Speed control P gain 2
1%
9999
0 to 1000%
Second function of
Pr. 820
(valid when RT signal is
on)
9999
No function
S
peed cont
rol
int
egr
al
t
im
e
s
e
tt
ing
821
Speed control integral time
1
0.001s
0.333s 0 to 20s
Set the integral time during speed control. (Decrease
the value to shorten the time taken for returning to
the original speed if speed variation with disturbance
occurs.)
831
Speed control integral time
2
0.001s
9999
0 to 20s
Second function of
Pr. 821
(valid when the RT
terminal is on)
9999
No function
—
822
Refer to
Pr. 74
.
Func
tio
n
Parameter
Name
Incre
ments
Initial
Value
Range
Description
Re
la
te
d
p
ara
m
e
te
rs
SensorlessS
e
n
s
o
rl
e
s
s
Sensorless
VectorV
e
c
to
r
Vector
SensorlessS
e
n
s
o
rl
e
s
s
Sensorless
VectorV
e
c
to
r
Vector
SensorlessS
e
n
s
o
rl
e
s
s
Sensorless
VectorV
e
c
to
r
Vector
SensorlessS
e
n
s
o
rl
e
s
s
Sensorless
VectorV
e
c
to
r
Vector
SensorlessS
e
n
s
o
rl
e
s
s
Sensorless
VectorV
e
c
to
r
Vector