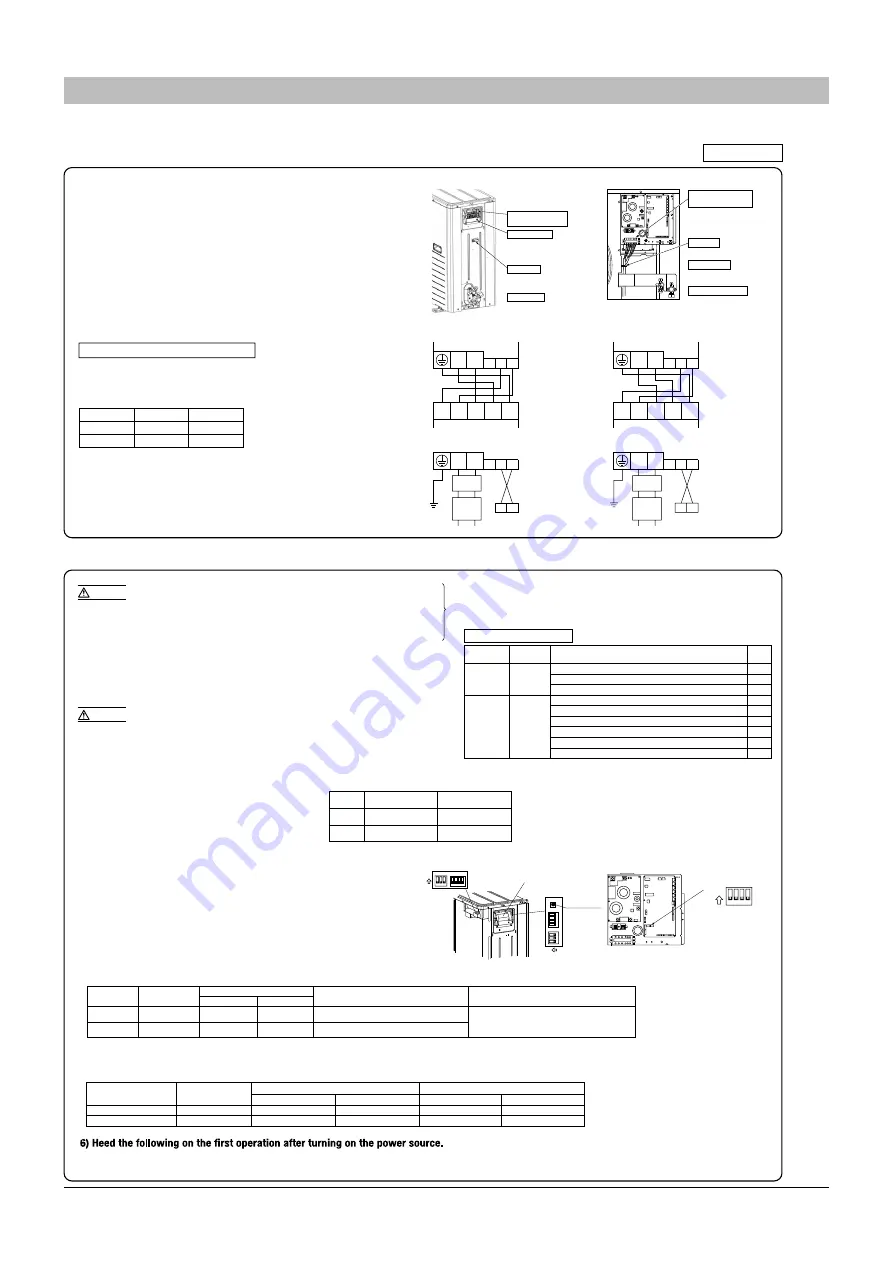
Installation
‘19 • HM-T-340
Outdoor unit installation
L
N
1
2
3
2
3
L
N
PE
Outdoor Unit
Indoor Unit
(X
2 terminal
)
N
L
1
2
3
2
3
L
N
PE
Outdoor Unit
L
N
1
2
3
Outdoor Unit
N
L
1
2
3
1
2
Outdoor Unit
Indoor Unit
(X
100 terminal
)
Indoor Unit
(X
2 terminal
)
1
2
Indoor Unit
(X
100 terminal
)
4. ELECTRICAL WIRING WORK
For details of electrical cabling, refer to the indoor unit installation manual.
5) The state of the electronic expansion valve.
The following table illustrates the steady states of the electronic expansion valve.
Valve for a cooling operation
During a cooling operation
When power is turned on
When the unit comes to a normal stop
When the unit comes to an abnormal stop
Valve for a heating operation
During a heating operation
During a cooling operation
During a heating operation
Complete shut position
Full open position
Full open position
Full open position
Complete shut position
Full open position
Full open position
Complete shut position
Full open position
Full open position
●
Connect a pair bearing a common terminal number with an indoor-outdoor connecting wire.
●
In cabling, fasten cables securely so that no external force may work on terminal connections.
●
Grounding terminals are provided in the control box.
●
Always perform grounding system installation work
with the power cord unplugged.
All set to OFF for shipment
SWITCHES FOR ON-SITE SETTING
SW3
ON
1
2
3
4
Power cable, indoor-outdoor connecting wires
Electrical installation work must be performed by an electrical installation service provider qualified by a power provider of the
country.
Electrical installation work must be executed according to the technical standards and other regulations applicable to
electrical installations in the country.
●
Ground the unit. Do not connect the grounding wire to a gas pipe, water pipe, lightning rod or telephone grounding wire.
If impropery grounded, an electric shock or malfunction may result.
●
A grounding wire must be connected before connecting the power cable. Provide a grounding wire longer than the power
cable.
●
Do not lay electronic control cables (remote control and signaling wires) and other cables together outside the unit. Laying
them together can result in the malfunctioning or a failure of the unit due to electric noises.
●
Fasten cables so that may not touch the piping, etc.
●
When cables are connected, make sure that all electrical components within the electrical component box are free of loose
connector coupling or terminal connection and then attach the cover securely. (Improper cover attachment can result in
malfunctioning or a failure of the unit, if water penetrates into the box.)
○
It is attached on the back side of
the service panel.
○
As like the refrigerant pipe, it can
be let out in any of the following
directions: side right, front, rear
and downward.
Power source, signal line
and ground terminal block
Wiring diagram
Outgoing cable direction
6)
Heed the following on the first operation after turning on the power supply.
This outdoor unit may start in the standby mode (waiting for a compressor startup), which can continue up to 30 minutes, to prevent the oil level
in the compressor from lowering on the first operation after turning on the circuit breaker. If that is the case, do not suspect a unit failure.
5. COMMISSIONING
For details of commissioning, refer to the Indoor unit installation manual
3) Setting SW3-1, SW3-2, on-site
(1) Defrost control switching (SW3-1)
・
When this switch is turned ON, the unit will run in the defrost mode more frequently.
・
Set this switch to ON, when installed in a region where outdoor temperature falls below zero during the
season the unit is run for a heating operation.
(2) Snow guard fan control (SW3-2)
・
When this switch is turned on, the outdoor unit fan will run for 10 seconds in every 10 minutes, when
outdoor temperature falls to 3
℃
or lower and the compressor is not running.
・
When the unit is used in a very snowy country, set this switch to ON.
2) Checking the state of the unit in operation
Use check joints provided on the piping before and after the four-way valve installed
inside the outdoor unit for checking discharge pressure and suction pressure.
As indicated in the table shown on the right, pressure detected at each point will
vary depending on whether a cooling or heating operation has been selected.
●
Before conduct a test run, make sure that the operation valves are open.
●
Turn on power 6 hours prior to a test run to energize the crank case heater.
Do not turn on the power when the ambient temperature is below
−
20
℃
to avoid breakdown of electronic
component.
●
In case of the first operation after turning on power, even if the unit does not operate for 30 minutes, it is
not a breakdown.
●
Always give a 3-minute or longer interval before you start the unit again whenever it is stopped.
●
Removing the service panel will expose high-voltage live parts and high-temperature parts, which are quite
dangerous.
Take utmost care not to incur an electric shock or burns. Do not leave the unit with the service panel open.
●
When you operate switches (SW3) for on-site setting, be careful not to touch a live part.
●
You cannot check discharge pressure from the liquid operation valve charge port.
●
The 4-way valve (20S) is energized during a heating operation.
●
When power supply is cut off to reset the unit, give 3 minutes or more before you turn on power again
after power is cut off. If this procedure is not observed in turning on power again, “Communication
error between outdoor and indoor unit” may occur.
Check item
Check
Item
Electric
wiring
Refrigerant
plumbing
WARNING
CAUTION
1) Test run method
Refer fo the indoor unit installation manual.
Cooling
operation
Heating
operation
Discharge pressure
(High pressure)
Suction pressure
(Low pressure)
Suction pressure
(Low pressure)
Discharge pressure
(High pressure)
Charge port of the
gas operation valve
Check joint of the pipe
●
When you leave the outdoor unit with power supplied to it,
be sure to close the panel.
Were air-tightness test and vacuum extraction surely performed?
Are heat insulation materials installed on both liquid and gas pipes?
Are operation valves surely opened for both liquid and gas systems?
Is the unit free from cabling errors such as uncompleted connection, or reversed phase?
Doesn’t cabling cross-connect between units, where more than one unit are installed?
Do indoor-outdoor connecting cables connect between the same terminal numbers?
Is the unit grounded with a dedicated grounding wire not connected to another unit’s grounding wire?
Are cables free from loose screws at their connection points?
Are cables held down with cable clamps so that no external force works onto terminal connections?
2
4
A failure to observe these instructions can result in a compressor breakdown.
Item No.used in the
installation manual
Items to checkbefore a test run
●
If an error code other than those listed above is indicated, refer to the wiring diagram of the outdoor unit and the indoor unit Installation manual.
Action
Failure event
63H1 actuation or operation with operation valves shut
(occurs mainly during a heating operation)
Low pressure error or operation with operation valves shut
(occurs mainly during a cooling operation)
1. Check whether the operation valves are open.
2. If an error has been canceled when 3 minutes have elapsed since a
compressor stop, you can restart the unit by effecting Check Reset
from the remote control unit.
Printed circuit board LED(The cycles of 5 seconds)
Red LED
Blinking once
Blinking once
4) Failure diagnosis in a test run
E40
E49
High pressure alarm
Low pressure alarm
Green LED
Blinking continuously
Blinking continuously
Error Code in Error Log
Indoor Unit Display
Wiring guide
Indoor unit : HMA100-S
Outdoor unit : 71VNX
Indoor unit : HMA100-S
Outdoor unit : 100VNX
Indoor unit : HSB100
Outdoor unit : 71VNX
Indoor unit : HSB100, 140
Outdoor unit : 100VNX, 140VNX
Circuit
breaker
Power source
Earth
leakage
breaker
Earth
Circuit
breaker
Power source
Earth
leakage
breaker
Earth
Wiring diagram
○
Do not connect to the grounding wire
from another unit, but install a
dedicated wire up to the grounding
wire from the distribution board.
○
It is attached on the back side of
the service panel.
Power source, signal line
and ground terminal block
Grounding terminal
Wiring clamp
○
Fasten cables and protect the
terminal connections from external
force.
Switches for on-site setting
ON
1 2 3
SW7
1 2 3 4
SW3
Power source, signal line and
ground terminal block
Switches for on-site setting
Pump down SW
※
Do not operate SW3-3, SW5, SW8.
4
3
2
1
3
2
1
ON
SW8
SW5
SW9
All set to OFF for
shipment
All set to OFF for shipment
100VNX. 140VNX
71VNX
100VNX. 140VNX
71VNX
Model
71VNX
100VNX,140VNX
Specification
250V 20A
250V 30A
Part No.
SSA564A117
SSA564A161
Main fuse specification
PSC012D066V
- 71 -
Содержание FDCW100VNX-A
Страница 7: ... 5 Technical data 19 HM T 340 Technical data ...
Страница 36: ... 34 Technical data 19 HM T 340 Dimensions FDCW71VNX A Meaning of symbol ...
Страница 38: ... 36 Technical data 19 HM T 340 FDCW140VNX A Meaning of symbol Dimensions ...
Страница 41: ... 39 Technical data 19 HM T 340 Electrical circuit diagram ...
Страница 42: ... 40 Technical data 19 HM T 340 Electrical circuit diagram ...
Страница 43: ... 41 Technical data 19 HM T 340 Electrical circuit diagram ...
Страница 44: ... 42 Technical data 19 HM T 340 Electrical circuit diagram ...
Страница 45: ... 43 Technical data 19 HM T 340 Electrical circuit diagram ...
Страница 46: ... 44 Technical data 19 HM T 340 Electrical circuit diagram ...
Страница 47: ... 45 Technical data 19 HM T 340 Electrical circuit diagram ...
Страница 48: ... 46 Technical data 19 HM T 340 Electrical circuit diagram ...
Страница 49: ... 47 Technical data 19 HM T 340 Electrical circuit diagram Split box HSB60 W ...
Страница 50: ... 48 Technical data 19 HM T 340 HSB100 Electrical circuit diagram ...
Страница 51: ... 49 Technical data 19 HM T 340 HSB140 Electrical circuit diagram ...
Страница 52: ... 50 Technical data 19 HM T 340 Electrical circuit diagram Outdoor units FDCW60VNX A ...
Страница 57: ... 55 Technical data 19 HM T 340 Electrical circuit diagram POWER SOURCE RC HY20 W sheet 3 ...
Страница 58: ... 56 Technical data 19 HM T 340 Electrical circuit diagram RC HY20 W sheet 4 ...
Страница 61: ... 59 Technical data 19 HM T 340 Electrical circuit diagram POWER SOURCE RC HY40 W sheet 3 ...
Страница 62: ... 60 Technical data 19 HM T 340 Electrical circuit diagram RC HY40 W sheet 4 ...
Страница 63: ... 61 Technical data 19 HM T 340 Electrical circuit diagram INDOOR UNIT HSB INDOOR UNIT HSB RC HY40 W sheet 5 ...
Страница 64: ... 62 Technical data 19 HM T 340 Electrical circuit diagram RC HY40 W sheet 6 ...
Страница 65: ...Installation 19 HM T 340 Installation 63 ...
Страница 133: ...Control 19 HM T 340 Control 131 ...
Страница 170: ... 168 Service 19 HM T 340 Service ...
Страница 263: ... 258 Service 19 HM T 340 Outdoor unit FDCW60VNX FDCW71VNX Component replacement ...
Страница 264: ...Service 259 19 HM T 340 FDCW100VNX FDCW140VNX LEK LEK Component replacement ...
Страница 290: ... 285 Components 19 HM T 340 Components ...
Страница 300: ... 295 Components 19 HM T 340 PT300 Component positions ...
Страница 301: ... 296 Components 19 HM T 340 Component positions PT300 PT300 A mm 1634 B mm 743 C mm 673 ...
Страница 302: ... 297 Components 19 HM T 340 PT500 Component positions ...
Страница 303: ... 298 Components 19 HM T 340 PT500 Component positions PT500 A mm 1835 B mm 897 C mm 832 ...
Страница 311: ...THo R THo A THo D Outside units FDCW60VNX 306 Components 19 HM T 340 Piping system ...