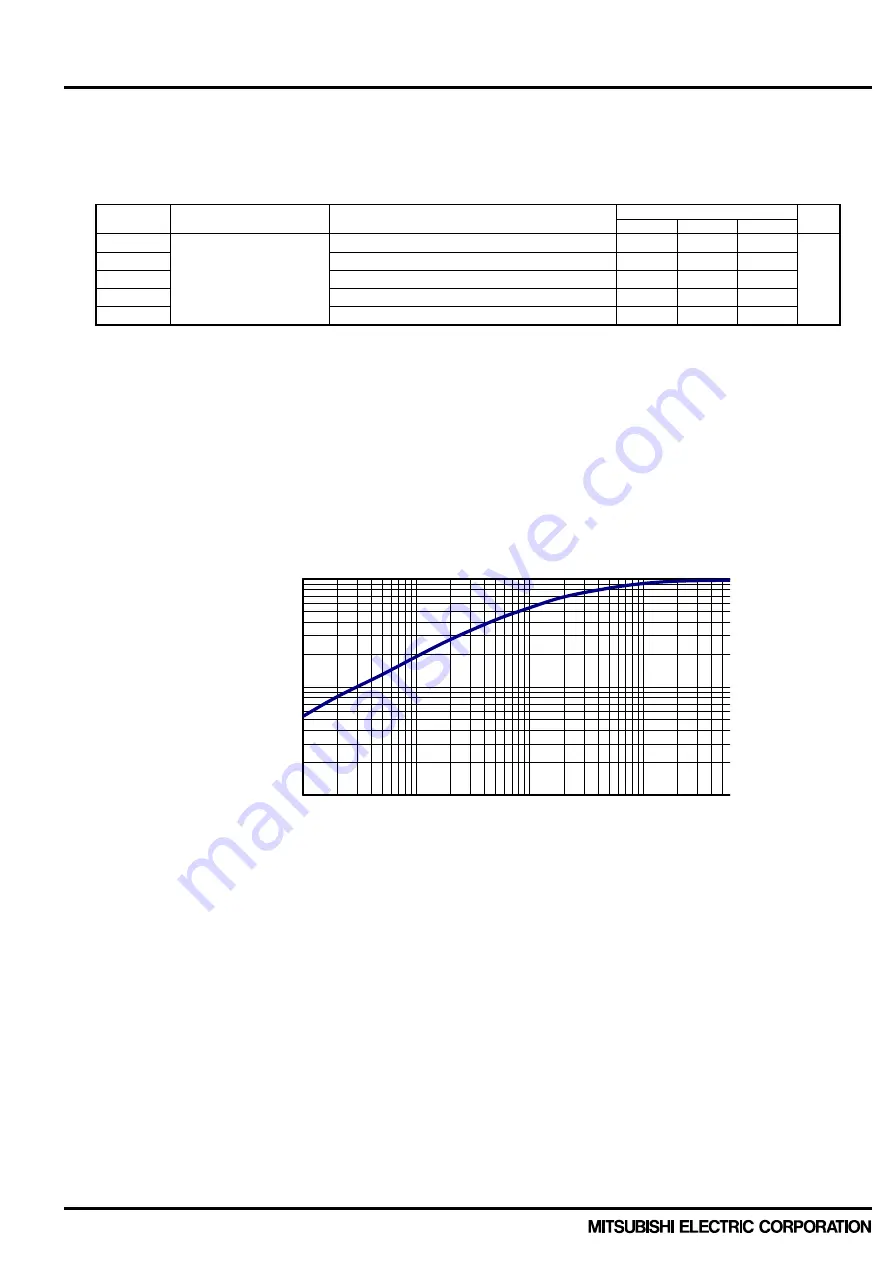
< Dual-In-Line Package Intelligent Power Module >
Series Application note
Publication Date: September 2016
8
2.1.2 Thermal Resistance
Table 2-1-2 shows the thermal resistance between its chip junction and case.
Table 2-1-2. Thermal resistance of PSS25MC1FT (25A/1200V, CIB type)
Symbol
Parameter
Condition
Limits
Unit
Min.
Typ.
Max.
R
th(j-c)Q
Junction to case thermal
resistance
(Note 3)
Inverter IGBT part (per 1/6 module)
-
-
1.15
K/W
R
th(j-c)F
Inverter FWD part (per 1/6 module)
-
-
1.65
R
th(j-c)Q
Brake IGBT part (per 1module)
-
-
1.45
R
th(j-c)F
Brake Di part (per 1module)
-
-
1.65
R
th(j-c)R
Converter part (per 1/6module)
-
-
1.10
Note 3: Grease with good thermal conductivity and long-term endurance should be applied evenly with about
+100μm~
+200μm on the contacting surface of DIPIPM and heat sink. The contacting thermal resistance between DIPIPM
case and heat sink Rth(c-f) is determined by the thickness and the thermal conductivity of the applied grease.
For reference, Rth(c-f) is about 0.25K/W (per 1chip
, grease thickness: 20μm, thermal conductivity: 1.0W/m•K).
The above data shows static state thermal resistance. The thermal resistance goes into saturation in about 10
seconds. The unsaturated thermal resistance is called as transient thermal impedance which is shown in
Fig.2-1-2. Zth(j-c)* is the normalized transient thermal impedance and formulation is described as Zth(j-c)*=
Zth(j-c) / Rth(j-c)max. For example, the IGBT transient thermal impedance at 0.2s is 1.15×0.7=0.81K/W. The
transient thermal impedance isn’t used for constantly current, but for short period current as millisecond order.
(e.g. motor starting, motor lock
・・・
e.t.c)
0.01
0.10
1.00
0.001
0.01
0.1
1
N
or
m
al
iz
ed
tr
ans
ient
ther
m
al
i
m
pedanc
e
Z
th(
j-
c
)*
Time (s)
Fig. 2-1-2. Normalized transient thermal impedance