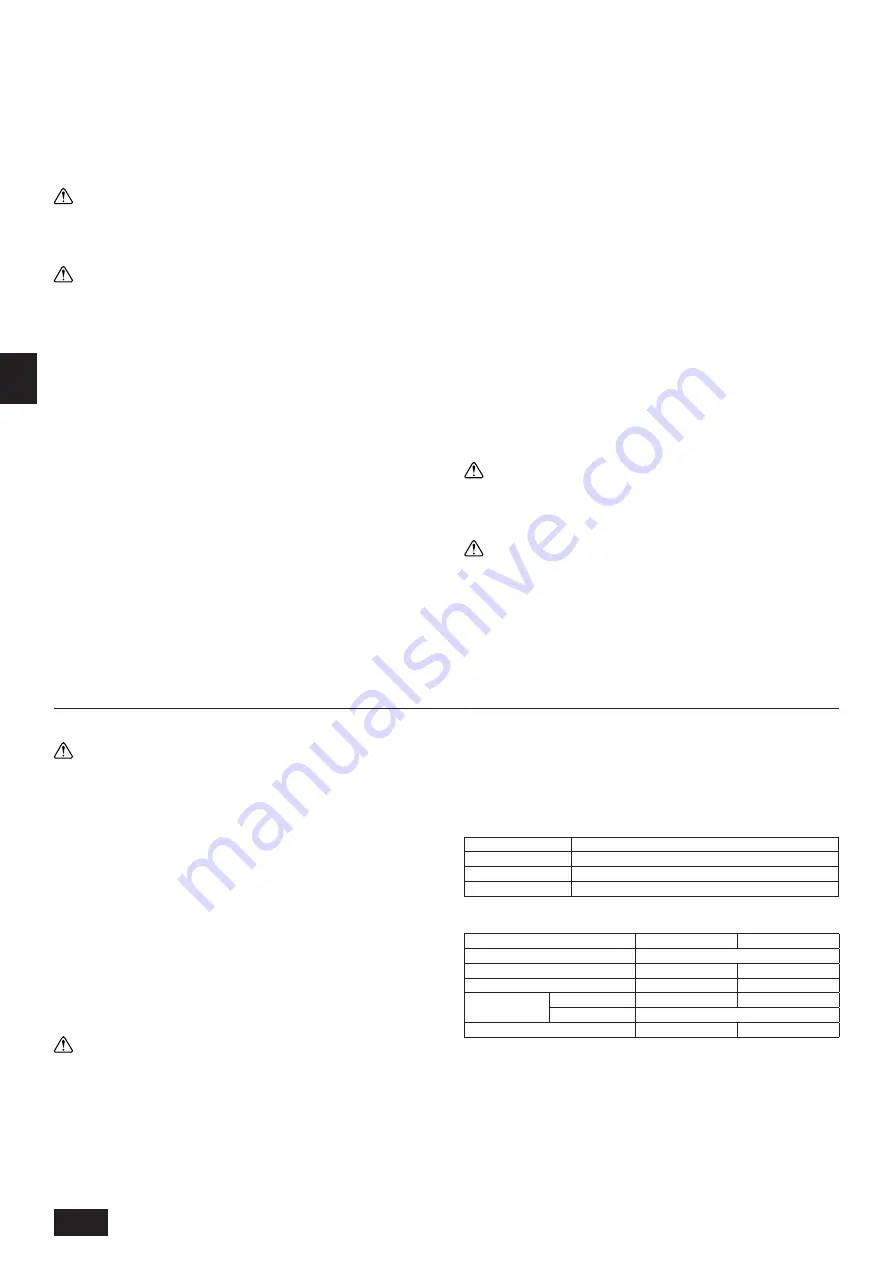
12
GB
Cautions on refrigerant piping
u
Be sure to use non-oxidative brazing for brazing to ensure that no for-
eign matter or moisture enter into the pipe.
u
Be sure to apply refrigerating machine oil over the flare connection
seating surface and tighten the connection using a double spanner.
u
Provide a metal brace to support the refrigerant pipe so that no load is
imparted to the indoor unit end pipe. This metal brace should be pro-
vided 50 cm away from the indoor unit’s flare connection.
Warning:
When installing and moving the unit, do not charge it with refrigerant other
than the refrigerant specified on the unit.
- Mixing of a different refrigerant, air, etc. may cause the refrigerant cycle to mal-
function and result in severe damage.
Caution:
• Use refrigerant piping made of phosphorus deoxidized copper and
copper alloy seamless pipes and tubes”. In addition, be sure that the
inner and outer surfaces of the pipes are clean and free of hazardous
sulphur, oxides, dust/dirt, shaving particles, oils, moisture, or any other
contaminant.
• Never use existing refrigerant piping.
- The large amount of chlorine in conventional refrigerant and refrigerator oil
in the existing piping will cause the new refrigerant to deteriorate.
• Store the piping to be used during installation indoors and keep both
ends of the piping sealed until just before brazing.
- If dust, dirt, or water gets into the refrigerant cycle, the oil will deteriorate
and the compressor may fail.
[Fig. 6.1.1] (P.3)
A
Piping on site
Expand the end of the pipe and braze it to the connecting pipe (non-oxidizing
brazing).
B
Piping on site
Expand the end of the pipe and braze it to the connecting pipe (non-oxidizing
brazing).
[Fig. 6.1.2] (P.3)
A
Pipe cover
B
Pipe mounting plate
C
Refrigerant piping (gas)
D
Refrigerant piping (liquid)
<Preparation of the pipes in a 2-refrigerant-circuit>
• Remove the pipe mounting plate.
• Peel off the pipe cover.
• Cut off both pipes at the specified location.
6.2. Drain piping work
[Fig. 6.2.1] (P.3)
A
Drain pan
B
Drain hose
C
As seen from front of unit
D
Main drain piping on site
E
Emergency drain piping on site
F
Trap (on-site piping work)
G
Drain piping on site (for humid filter)
1. Ensure that the drain piping is downward (pitch of more than 1/100) to the
outdoor (discharge) side. Do not provide any trap or irregularity on the way.
2. Ensure that any cross-wise drain piping is less than 20 m (excluding the dif
-
ference of elevation). If the drain piping is long, provide metal braces to pre
-
vent it from waving. Never provide any air vent pipe. Otherwise drain may be
ejected.
3. Do not provide any odor trap at the drain discharge port.
4. Put the end of the drain piping in a position where no odor is generated.
5. Do not put the end of the drain piping in any drain where ionic gases are
generated.
6. Check drainage by pouring water into the drain pan and check to see that it
drains properly.
7. Check for ease of operation of the fault detection float switch in the drain
pan, and breakage of leads.
8. Provide a drain trap to the drain piping installed on site.
* The loop on the drain hose provided with the unit does not function as a
trap; it is only used to drain water to the main drain pan at the bottom of
the product.
Note:
If the rise portion is long, there will be a lot of returned water in an opera-
tion stop, generating slime or odor during off-season. Ensure that the rise
portion is at a minimum.
Caution:
Always prepare the water seal by filling the trap with water from the drain
pan during test operation. Inject water into the drain trap during the peri-
odic check (six-monthly) to check water-sealing. If the trap is not filled with
water, it will cease to function and this may result in leaks.
Caution:
Pipe the drain piping to ensure that it discharges drain, and insulate it to
prevent dew condensation. A failure to the piping work may cause water
leakage and so wet your property.
Precautions on electrical wiring
Warning:
Electrical work should be done by qualified electrical engineers in accord-
ance with “Engineering Standards For Electrical Installation” and supplied
installation manuals. Special circuits should also be used. If the power
circuit lacks capacity or has an installation failure, it may cause a risk of
electric shock or fire.
1. Be sure to take power from the special branch circuit.
2. Be sure to install an earth leakage breaker to the power.
3. Install the unit to prevent that any of the control circuit cables (remote con
-
troller, transmission cables) is brought in direct contact with the power cable
outside the unit.
4. Ensure that there is no slack on all wire connections.
5. Some cables (power, remote controller, transmission cables) above the ceil
-
ing may be bitten by mouses. Use as many metal pipes as possible to insert
the cables into them for protection.
6. Never connect the power cable to leads for the transmission cables. Other
-
wise the cables would be broken.
7. Be sure to connect control cables to the indoor unit, remote controller, and
the outdoor unit.
8. Put the unit to the ground on the outdoor unit side.
9. Select control cables from the conditions given in below.
Caution:
Be sure to put the unit to the ground on the outdoor unit side. Do not
connect the earth cable to any gas pipe, water pipe, lightening rod, or
telephone earth cable. Incomplete grounding may cause a risk of electric
shock.
Types of control cables
1. Wiring transmission cables
• Types of transmission cables
Shielding wire (2-core)
CVVS, CPEVS or MVVS <max length: 200 m>.
• Cable diameter
More than 1.25 mm
2
2. Remote controller cables
MA remote controller
Types of cables
2-core cable (unshielded)
Cable diameter
0.3 to 1.25 mm
2
Length
Less than 200 m
7.1. Power supply wiring
Model
PFD-P250VM-E
PFD-P500VM-E
Power supply
380 - 415V
Power supply wiring cross-section
2.5 mm
2
4.0 mm
2
Earth wiring cross-section
2.5 mm
2
4.0 mm
2
Earth leakage
breaker
Type <capacity>
20 A
30 A
Rated sensitivity
30 mA less than 0.1 s
Wiring breaker (NFB)
20 A
30 A
Note:
1. Bear in mind ambient conditions (ambient temperature,direct sunlight,
rain water,etc.) when proceeding with the wiring and connections.
2. The wire size is the minimum value for metal conduit wiring. The power
cord size should be 1 rank thicker consideration of voltage drops.
Make sure the power-supply voltage does not drop more than 10 %.
3. Specific wiring requirements should adhere to the wiring regulations of
the region.
7. Electrical wiring