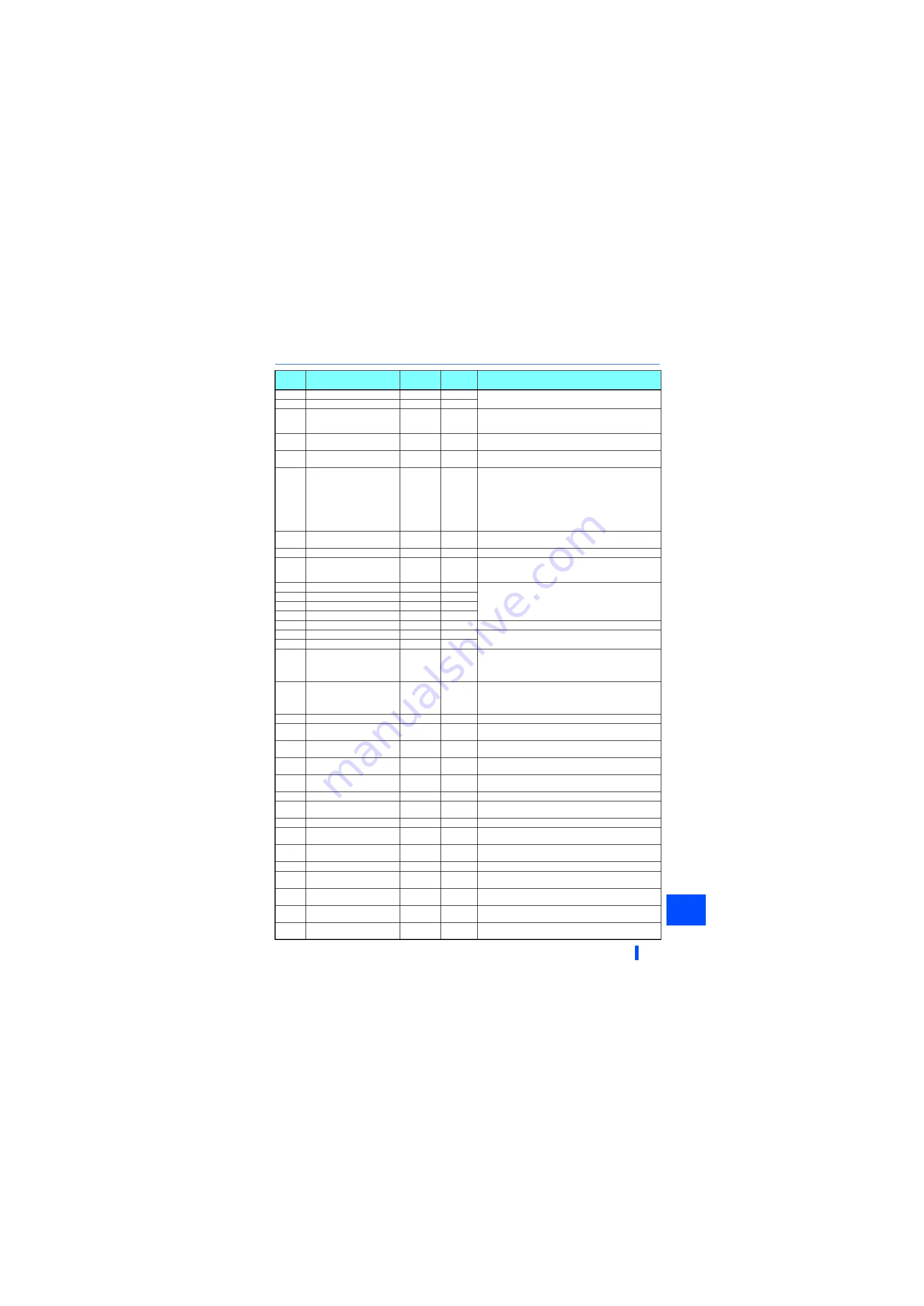
Application examples
201
10
7
Acceleration time
15 s
0 s
Use these parameters to improve trackability of the dancer
feedback speed control.
8
Deceleration time
15 s
0 s
9
Electronic thermal O/L relay
Inverter
rated
current
0 A
Setting for a specific motor for Vector control (motor with built-in
thermal protector).
DC injection brake operation
frequency
3 Hz
0.5 Hz
18
High speed maximum
frequency
120 Hz
70 Hz
52
Operation panel main monitor
selection
0
22
Set "22" (Roll diameter) for monitoring.
Or use any of
Pr.774 to Pr.776
when using the 3-line monitor
screen on the PU.
Other monitor items related to this application and their setting
values are as follows:
26 (Line speed command), 27 (Actual line speed), 28 (Dancer
compensation speed), 29 (Winding length), 52 (PID set point), 53
(PID measured value), and 54 (PID deviation).
71
Applied motor
0
30
30: Setting for the Mitsubishi Electric Vector control dedicated
motor SF-V5RU.
72
PWM frequency selection
2
15
73
Analog input selection
1
10
10: Terminal 2 input between 0 to 10 V for the line speed and
terminal 1 input between 0 to 10 V for the dancer signal with
reversible polarity.
80
Motor capacity
9999
15 kW
Set these parameters according to the motor.
81
Number of motor poles
9999
4 (poles)
83
Rated motor voltage
200 V
164 V
84
Rated motor frequency
9999
51
128
PID action selection
0
40
40: Dancer control enabled (reverse action)
129
PID proportional band
100%
100%
Performing tension PI gain tuning allows setting these
parameters.
130
PID integral time
1 s
10 s
133
PID action set point
500%
550%
Set
Pr.52
= "86" (Terminal 1 input after calibration in %) to check
the upper and lower limit of the dancer roll position. Set the target
position (neutral position) in this parameter according to the
check result.
134
PID differential time
9999
9999
To improve trackability of a mechanical extraneous disturbance
(variation), set 0.01 seconds at first, and change the setting to a
slightly larger value as required. (Set the minimum possible
value because setting a too large value causes hunting.)
158
AM terminal function selection
1
19
19: Analog output signal for dancer tension control
180
RL terminal function selection
0
114
114: Tension control selection (X114) signal ON (Setting "114" is
required for tension control.)
181
RM terminal function selection
1
109
109: Stored winding diameter clear (X109) signal ON (Setting
"109" clears the stored roll diameter.)
186
CS terminal function selection
6
7
7: External thermal relay input (OH) signal (Setting "7" is required
for signals input from the SF-V5RU thermal protector.)
190
RUN terminal function selection
0
232
232: Winding diameter calculation completion at start (Y232)
signal (positive logic)
267
Terminal 4 input selection
0
2
2: Terminal 4 input between 0 to 10 V for the taper ratio setting
350
Line speed command voltage/
current bias
0%
0%
351
Line speed command bias
0 m/min
0 m/min
Use
Pr.358
to set the increment.
352
Line speed command voltage/
current gain
50%
100%
353
Line speed command gain
1000 m/min
200 m/min
Use
Pr.358
to set the increment. Maximum line speed (200 m/
min) is set.
358
Line speed unit
0
0
0: m/min (increment of the maximum line speed)
360
Line speed command value
0 m/min
0 m/min
If setting
Pr.361
to "8", set a line speed command value in this
parameter.
361
Line speed command input
selection
9999
0
362
Actual line speed input
selection
0
0
0: Signals for the actual line speed are not input (the actual line
speed is determined by calculating from the line speed setting).
363
Dancer / tension sensor
feedback input selection
9999
5
5: Dancer signals input via terminal 1.
Pr.
Parameter name
Initial
value
Setting
value
Remarks
Содержание A800 Plus Series
Страница 240: ...239 MEMO ...