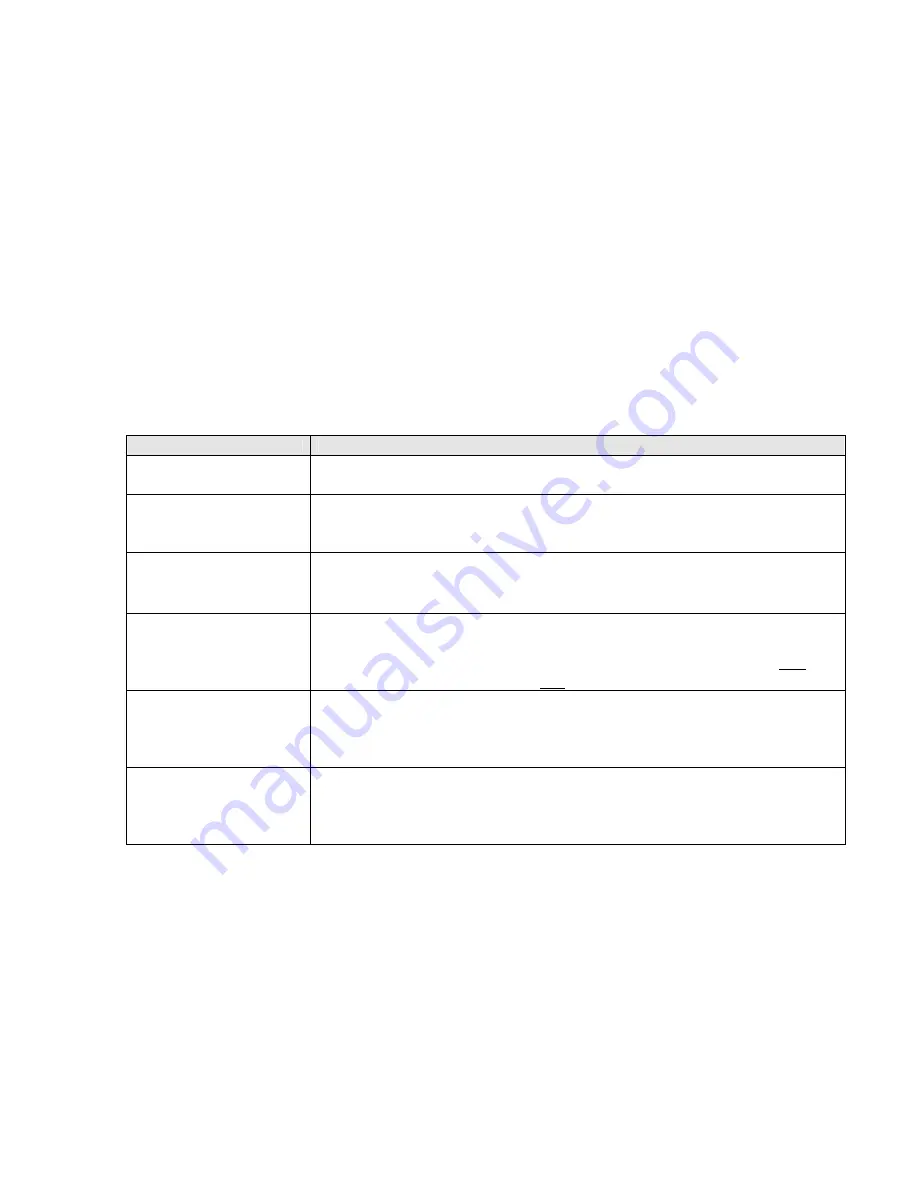
17
Mounting of Switch Modules in a Redundancy Chain
Brackets and associated hardware are provided such that a converter can be removed
from the rack without disconnecting the Switch Module from the redundancy chain. See
Figures 3-1 and 3-2 below for the proper arrangement for the supplied hardware. Each
successive Switch Module must be no more than one rack unit (1RU, 1.75”) from the
unit that precedes it. If additional space is required between Switch Modules, consult
the factory for an accessory package of hardware and cables to accommodate your
physical arrangement.
2.3 TURN-ON PROCEDURE
After mounting, make all external connections per Tables 1-1, 1-2, 1-3 and 2-1.
Apply power to the equipment using the power On/Off switches.
System is now operational.
DESIGNATION
DESCRIPTION
Ground Lug
Connect the Ground Lug on the rear panel of the equipment to the
Protective Earth connection of the building.
Power Cords
Attach the power cords to the rear panel AC power inlet. Connect the
other end to the power source. Refer to national wiring standards for
the correct connection to the power source.
Converter Monitor and
Control Connectors
(J1 to J13)
This connector accepts form-c contacts from Backup and Primary
Units 1 through 12 and provides a means of converter control from the
control unit. See Paragraph 1.2.3 for wiring information.
Switch Module Monitor
and Control
Connectors
(J14, J15 NSUN Only)
The Switch Module Bus Interface connectors are daisy-chained
internally for added reliability. This is the communication link to the
Switch Modules for redundancy operation. Connect J14 to the first
Switch Module and J15 to the last Switch Module.
NSU Monitor and
Control Connector
(J16)
This is an optional connection allowing the operator to monitor and
control the equipment from a remote location. This connector also
provides form-c contacts that indicate the active fault state of the
Control Unit. See Paragraph 1.2.3 for wiring information.
Ethernet Interface
Connector (J17)
The Ethernet Interface connector is an optional connection. This
allows the operator to monitor and control the equipment via an
Ethernet network connection. See Paragraph 1.2.2 for wiring
information.
Table 2-1. External Connections