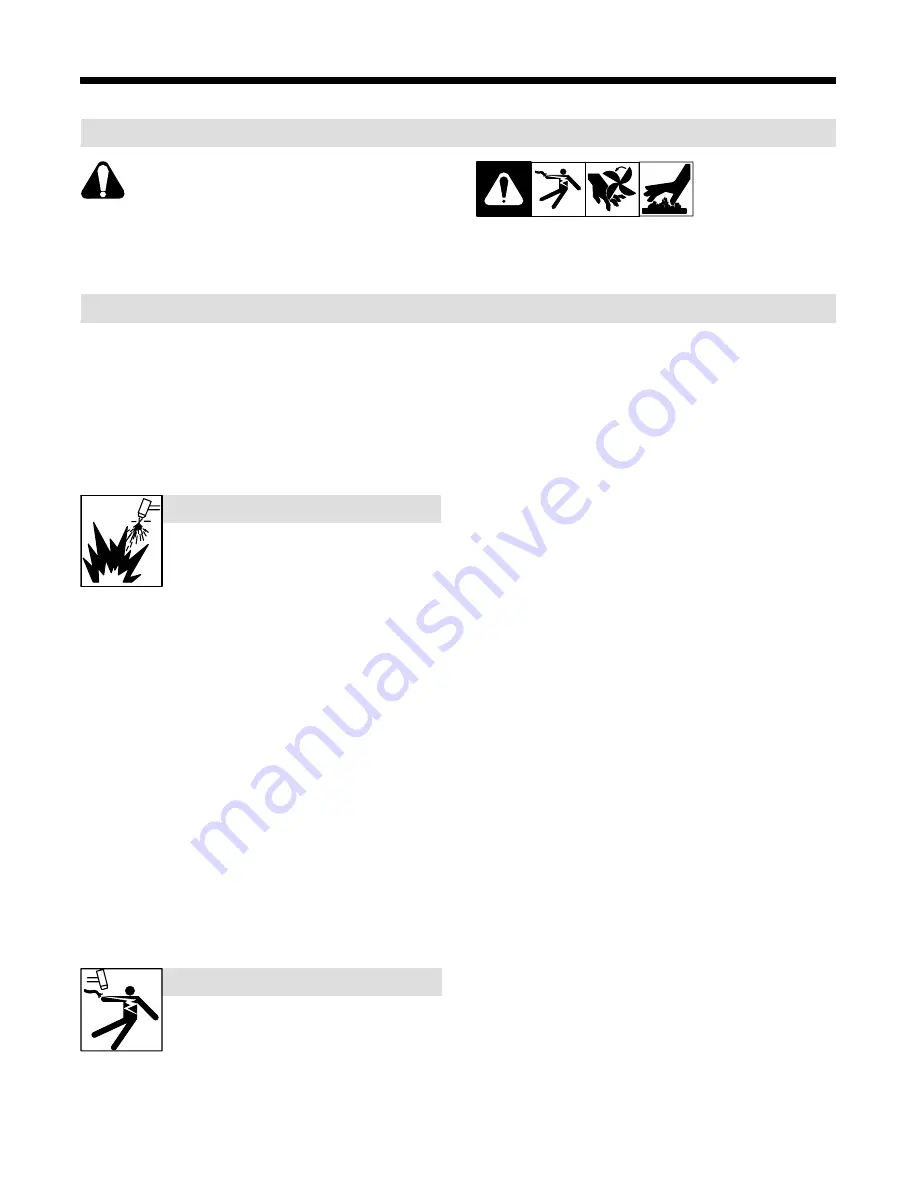
OM-219 Page 1
SECTION 1 – SAFETY PRECAUTIONS - READ BEFORE USING
pom _nd_5/97
1-1.
Symbol Usage
Means Warning! Watch Out! There are possible hazards
with this procedure! The possible hazards are shown in
the adjoining symbols.
Y
Marks a special safety message.
.
Means “Note”; not safety related.
This group of symbols means Warning! Watch Out! possible
ELECTRIC SHOCK, MOVING PARTS, and HOT PARTS hazards.
Consult symbols and related instructions below for necessary actions
to avoid the hazards.
1-2.
Plasma Arc Cutting Hazards
Y
The symbols shown below are used throughout this manual to
call attention to and identify possible hazards. When you see
the symbol, watch out, and follow the related instructions to
avoid the hazard. The safety information given below is only
a summary of the more complete safety information found in
the Safety Standards listed in Section 1-4. Read and follow all
Safety Standards.
Y
Only qualified persons should install, operate, maintain, and
repair this unit.
Y
During operation, keep everybody, especially children, away.
CUTTING can cause fire or explosion.
Hot metal and sparks blow out from the cutting arc.
The flying sparks and hot metal, hot workpiece, and
hot equipment can cause fires and burns. Check
and be sure the area is safe before doing any cutting.
D
Protect yourself and others from flying sparks and hot metal.
D
Do not cut where flying sparks can strike flammable material.
D
Remove all flammables within 35 ft (10.7 m) of the cutting arc. If this
is not possible, tightly cover them with approved covers.
D
Be alert that sparks and hot materials from cutting can easily go
through small cracks and openings to adjacent areas.
D
Watch for fire, and keep a fire extinguisher nearby.
D
Be aware that cutting on a ceiling, floor, bulkhead, or partition can
cause fire on the hidden side.
D
Do not cut on closed containers such as tanks or drums.
D
Connect work cable to the work as close to the cutting area as prac-
tical to prevent cutting current from traveling long, possibly
unknown paths and causing electric shock and fire hazards.
D
Never cut containers with potentially flammable materials inside –
they must be emptied and properly cleaned first.
D
Do not cut in atmospheres containing explosive dust or vapors.
D
Do not cut pressurized cylinders, pipes, or vessels.
D
Do not cut containers that have held combustibles.
D
Wear oil-free protective garments such as leather gloves, heavy
shirt, cuffless trousers, high shoes, and a cap.
D
Do not locate unit on or over combustible surfaces.
D
Remove any combustibles, such as a butane lighter or matches,
from your person before doing any cutting.
Touching live electrical parts can cause fatal shocks
or severe burns. The torch and work circuit are
electrically live whenever the output is on. The input
power circuit and machine internal circuits are also
live when power is on. Plasma arc cutting requires
higher voltages than welding to start and maintain the arc (200 to 400
volts dc are common), but also uses torches designed with safety
interlock systems which turn off the machine when the shield cup is
loosened or if tip touches electrode inside the nozzle. Incorrectly
installed or improperly grounded equipment is a hazard.
ELECTRIC SHOCK can kill.
D
Do not touch live electrical parts.
D
Wear dry, hole-free insulating gloves and body protection.
D
Insulate yourself from work and ground using dry insulating mats or
covers big enough to prevent any physical contact with the work or
ground.
D
Do not touch torch parts if in contact with the work or ground.
D
Turn off power before checking, cleaning, or changing torch parts.
D
Disconnect input power before installing or servicing this equip-
ment. Lockout/tagout input power according to OSHA CFR
1910.147 (see Safety Standards).
D
Properly install and ground this equipment according to its Owner’s
Manual and national, state, and local codes.
D
Check and be sure that input power cord ground wire is properly
connected to ground terminal in disconnect box or that cord plug is
connected to a properly grounded receptacle outlet – always verify
the supply ground.
D
When making input connections, attach proper grounding conduc-
tor first.
D
Frequently inspect input power cord for damage or bare wiring – re-
place cord immediately if damaged – bare wiring can kill.
D
Turn off all equipment when not in use.
D
Inspect and replace any worn or damaged torch cable leads.
D
Do not wrap torch cable around your body.
D
Ground the workpiece to a good electrical (earth) ground if required
by codes.
D
Use only well-maintained equipment. Repair or replace damaged
parts at once.
D
Wear a safety harness if working above floor level.
D
Keep all panels and covers securely in place.
D
Do not bypass or try to defeat the safety interlock systems.
D
Use only torch(es) specified in Owner’s Manual.
D
Keep away from torch tip and pilot arc when trigger is pressed.
D
Clamp work cable with good metal-to-metal contact to workpiece
(not piece that will fall away) or worktable as near the cut as
practical.
D
Insulate work clamp when not connected to workpiece to prevent
contact with any metal object.
SIGNIFICANT DC VOLTAGE exists after removal
of input power on inverters.
D
Turn OFF inverter, disconnect input power, and discharge input
capacitors according to instructions in Maintenance Section
before touching any parts.
Содержание Spectrum Plus
Страница 4: ......
Страница 30: ...OM 222 Page 26 SECTION 5 ELECTRICAL DIAGRAMS Figure 5 1 Circuit Diagram For Cutter SC 171 596 A...
Страница 33: ...OM 219 Page 29 Notes...
Страница 35: ...OM 219 Page 31 ST 800 867 A 6 7 8 9 10 11 12 13 15 16 17 18 14 19 20 21 22 23 24 25 26 27 28 29 30 31 32 33 34...
Страница 40: ...OM 219 Page 36 ST 800 889 1 2 3 4 5 6 7 8 9 10 11 12 13 14 15 16 17 18 Figure 7 3 Arc Starter Assembly...