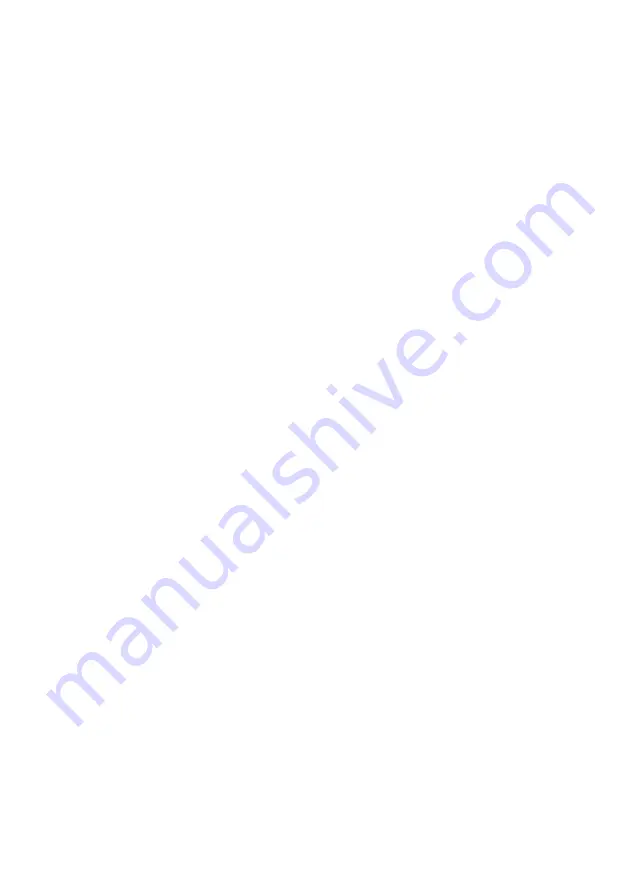
Chapter 5 - Electrical Control Cabinets
Medha Servo Drives Pvt Ltd.
26
5.4 Driver Accessible Panels
These are the various Driver Accessible Panels:
1. Circuit Breaker Panel
2. Engine Control Panel
3. Ground Relay Cutout switch and Test panel
4. MDS 737 Display Unit for TM Cutout, viewing of Crew messages and
Fault Archive and to Enter Driver ID, Train no. Section name, Train
Load, etc.
5. Auxiliary Generator (250 A) CB in the ECC#2
6. Auxiliary Generator (250 A) CB in the ECC#2
5.5 Circuit Breaker Panel
ECC#1 cabinet Circuit Breaker panel has approximately 33 Circuit Breakers
that are used in the control and protection of Diesel Engine and Electrical
systems. These Breakers can operate as switches but get trip open when an
overload occurs.
1.
LIGHTS Circuit Breaker:
This 30A Circuit Breaker must be switched
ON (liver up) to power the locomotive lights switches.
2.
HDLTS Breaker:
This 35A Circuit Breaker provides power and
protection to the cab end and hood end Head Light circuits.
3.
CAB FANS Circuit Breaker:
This 30A Circuit Breaker provides
power and protection for Cab Air Circulating Fan motors and their
control circuits.
4.
AIR DRYER Circuit Breaker:
This 15A Circuit Breaker provides
power and protection to the main Reservoir Air Filter Dryer and
associated circuit.
5.
AC CONTROL Circuit Breaker:
This 15A Circuit Breaker Provides
CA Power supply to ZCD circuit, to detect zero crossing and control
Excitation for Main Alternator.
6.
CONTROL Circuit Breaker:
This 40A Circuit Breaker sets up the
Fuel Pump and control circuits for engine starting. It supplies Battery
Power through Battery Knife switch before an Engine starts. Once
the Engine is running, the Auxiliary Generator Supplies Power
through this breaker to main operating control.
7.
LOCAL CONTROL Circuit Breaker:
This 30A Circuit Breaker
establishes Local control with power from the Locomotive Battery or
Auxiliary Generator to operate heavy duty switch gear, Magnetic
valves, contactors, Blowers and Relays etc.