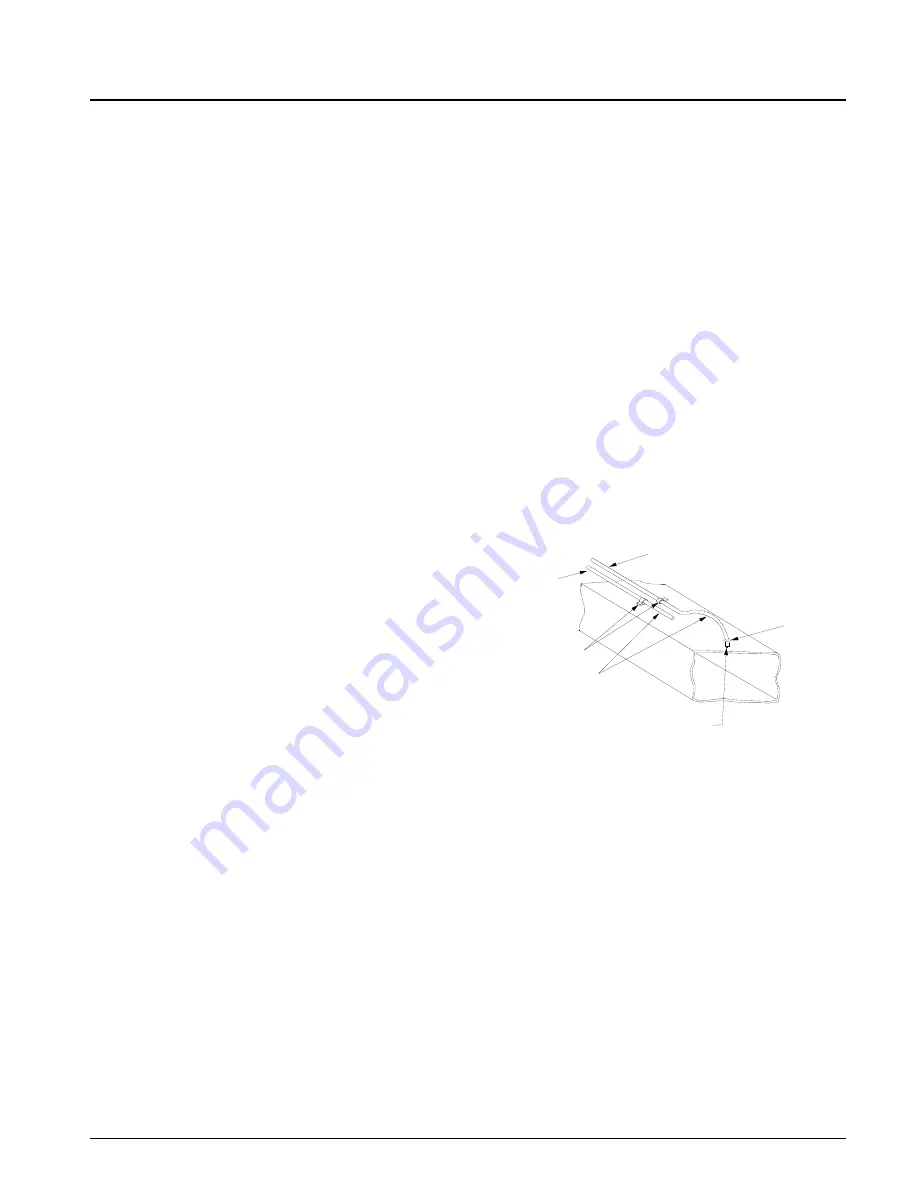
IM709
31
Unit Options
Duct High Limit
A duct high limit (DHL) pressure control is provided as stan-
dard with all units having variable air volume control. The
duct high limit is intended to protect the ductwork, etc. from
over pressurization caused by tripped fire dampers or a con-
trol failure. When the duct pressure exceeds the setting of the
control, the unit is de-energized via the MicroTech II con-
troller and an alarm condition indicated. After the reason for
trip has been identified and corrected, the control can be
reset via the MicroTech II keypad/display interface.
The duct high limit is preset for a 3.0" w.c. trip point. The
control can be readjusted in the field to match the specific
ductwork of a project. The switch has a field adjustable set
point range of 0.17 to 5.0 inches of H
2
O. Turn adjustment
screw clockwise to decrease differential pressure setting.
Turn adjustment screw counterclockwise to increase differ-
ential pressure setting. The DHL is located in the coil section
on the back side of the control panel.
Phase Fail/Under Voltage Protection
The monitor is a microprocessor controlled device which
provides protection against three-phase electrical motor loss
due to low voltage, phase loss, voltage unbalance and phase
reversal. The microprocessor constantly monitors the three-
phase line voltages and detects these harmful power line
conditions. Whenever any of these conditions occur, the
SWT controls are deactivated and remain deactivated until
power line conditions return to an acceptable level. Trip and
reset delays have been provided to prevent nuisance tripping
due to rapid power fluctuations. The trip and reset delays are
field adjustable. The monitor also provides a variable line
voltage adjustment.
Duct Static Pressure Sensor
All units provided with variable air volume control include a
factory mounted static pressure sensor (SPS1). The unit can
also have an optional second static pressure sensor, SPS2.
The sensor is factory wired and requires field installation of
1/4" l.D. sensor tubing to the selected duct location. Note: Be
sure that tubing complies with local code requirements.
Flame retardant plastic or metal tubing may be required.
Carefully select the ductwork sensing point for the pressure
sensor. Improper location of the sensing point will result in
unsatisfactory operation of the entire variable air volume
system. Follow these guidelines:
1.
Sense near the end of long duct runs to ensure that all
terminal box take-offs along the run will have adequate
static pressure to operate.
2.
The end of the sensing tube must be perpendicular to the
airflow in order to sense only static pressure.
3.
The sensing tube should be located in a non-turbulent
flow area of the duct. Keep several duct widths away
from take-off points, bends or neck downs.
Mounting instructions (see Figure 26)
1.
Drill hole in duct at remote sensing point and install a
rubber grommet. Insert sensing tube 1/8" into the duct
and securely clamp tubing to the duct, being sure not to
stress or kink the tubing. The end of the sensing tube
must be smooth and cut straight across. An angle cut
will affect operation.
2.
Clamp a second tube to the outside of the duct at the
location of the sensing point.
3.
Run both tubes along the ductwork and back to the unit.
The tubing may be routed to the pressure sensor (SPS1)
by drilling two holes through the unit upright post. A
grommet must be used at each hole to protect the tubing
and seal the cabinet. Note: To avoid confusion between
"high" and "low" tubing, it is recommended that two
different tubing colors be used and that this information
be recorded, along with the sensing point location, on
the master building blueprints.
4.
Connect tubing to the high and low ports on the sensor.
Figure 26
Building Static Pressure Sensor
If a unit has direct building static pressure control capability,
static pressure taps must be field installed and connected to
pressure sensor SPS1 in the unit. This sensor is located on
the control panel.
The two static pressure sensing taps must be carefully
located and installed. Improper location or installation of the
sensing taps will cause unsatisfactory operation. Following
are pressure tap location and installation recommendations
for both building envelope and lab, or "space within a space':
pressure control applications. The installation must comply
with local code requirements.
TO SENSOR
"HI" INPUT
TO SENSOR
"LO" INPUT
TUBE CLAMPS
PRESSURE
SENSING
TUBING
RUBBER
GROMMET
TUBING EXTENDS
THRU APPROX. 1/8"
Содержание SWT C Series
Страница 23: ...IM709 23 Typical Wiring Schematics Figure 19 Power Schematic...
Страница 24: ...24 IM709 Figure 20 Input Schematic Discharge Air Control DAC...
Страница 25: ...IM709 25 Figure 21 Input Schematic Zone or Space Comfort Control SCC...
Страница 26: ...26 IM709 Figure 22 Output Schematic Actuator Control...
Страница 27: ...IM709 27 Figure 23 Output Schematic Auxiliary Fan Start Stop Control...
Страница 28: ...28 IM709 Figure 24 Output Schematic Actuator Control...
Страница 29: ...IM709 29 Figure 25 Output Schematic Compressor Control 4 Compressors 4 5 or 6 Stage...
Страница 44: ...13600 Industrial Park Boulevard Minneapolis MN 55441 USA 763 553 5330...