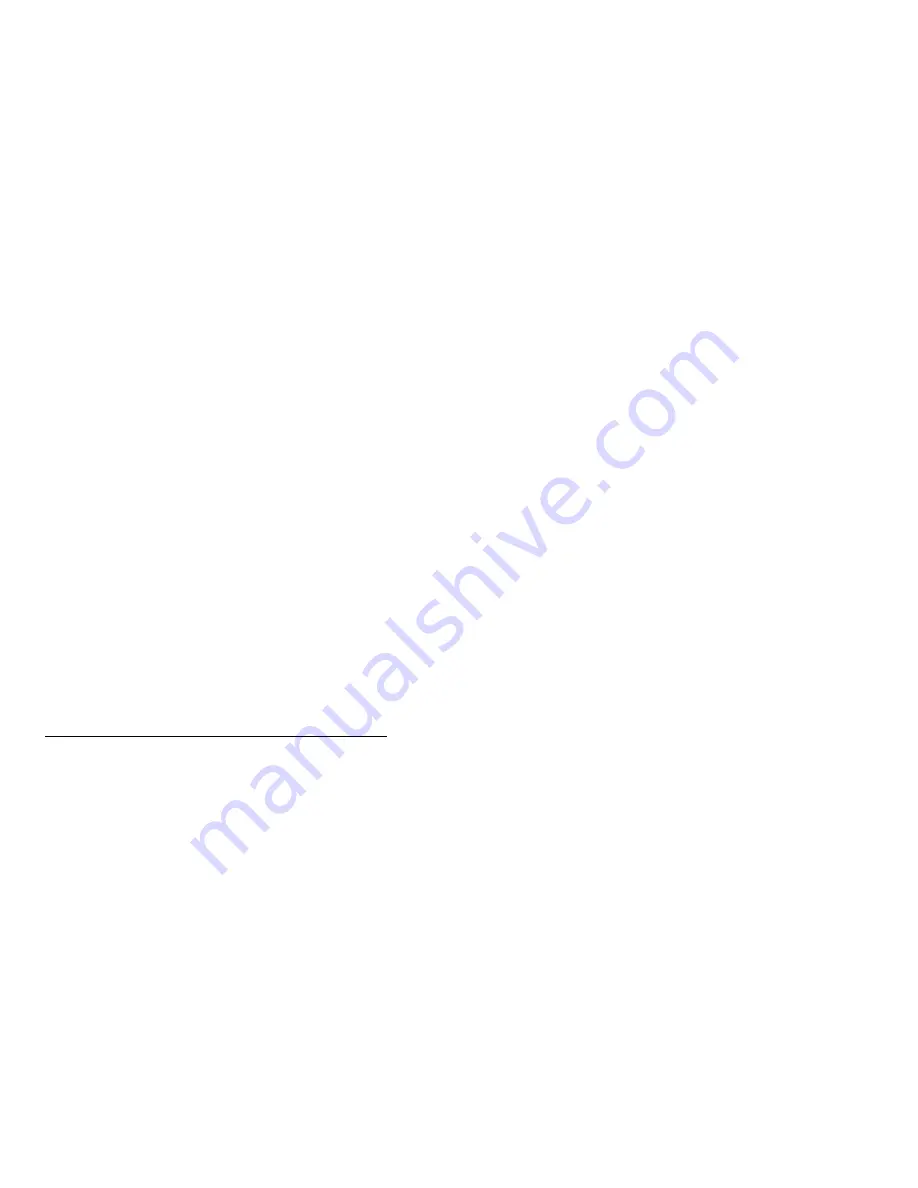
Battery Care/Maintenance
A-6
Removing a Battery Pack
Use the following procedure to remove a battery pack:
1.
Before removing a battery pack, turn off the
calibrator and disconnect the charger.
2.
Loosen the two captive screws on the back of the
battery pack.
3.
Pull the top of the battery pack away from the
calibrator, lifting up and out.
Содержание BetaGauge II
Страница 1: ...BetaGauge II Pressure Calibrator User Guide ...
Страница 8: ...viii Specifying Post Test Status Information 7 23 ...
Страница 11: ...xi ...
Страница 15: ...xiv ...
Страница 27: ...General Description 1 12 ...
Страница 35: ...Input Modules 2 8 ...
Страница 141: ...Application Notes 6 56 ...
Страница 165: ...Doc Cal Mode 7 24 ...
Страница 183: ...Specifications B 8 ...
Страница 189: ...Service Information D 4 ...
Страница 197: ...Index I 8 ...