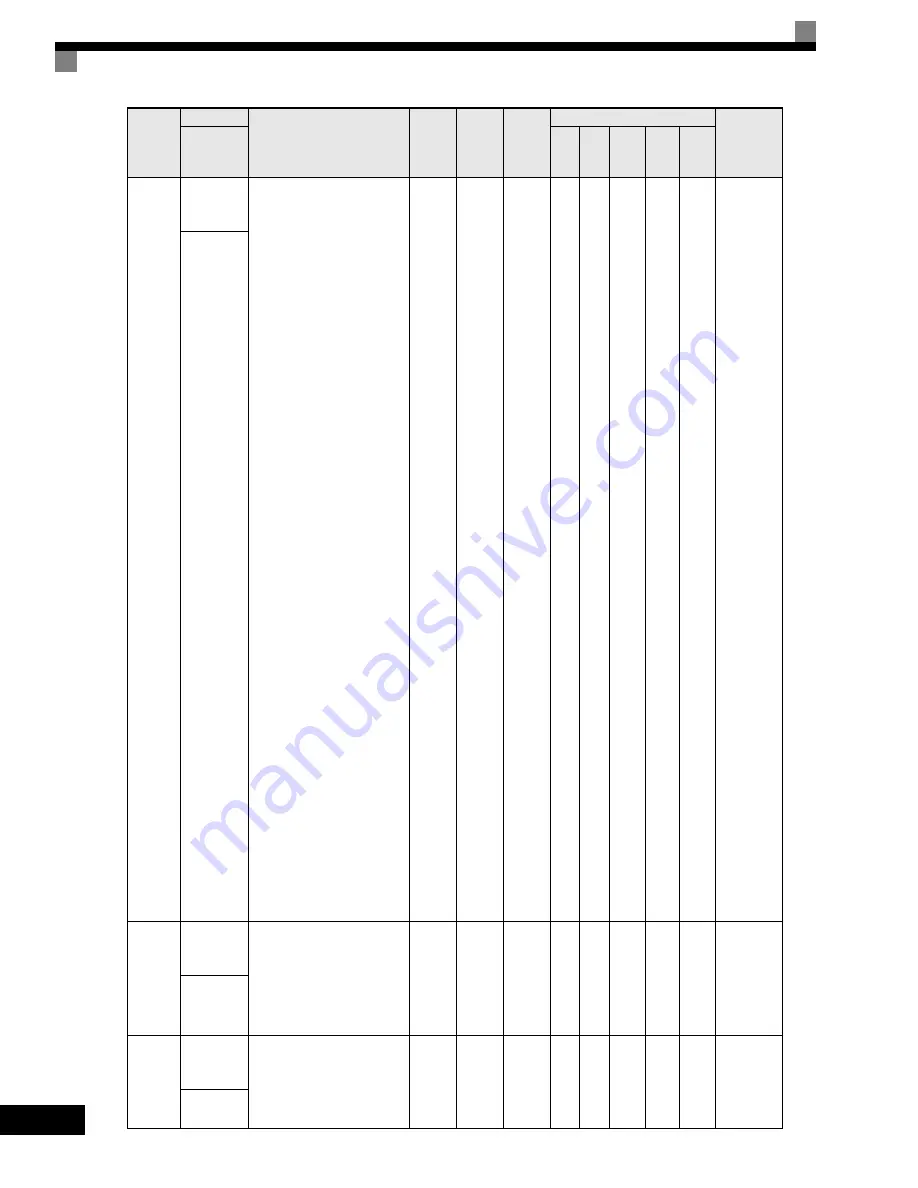
5
-70
L6-04
Torque
Detection
Selection 2
Determines the Drive's
response to an Overtorque/
Undertorque condition.
Overtorque and Undertorque
are determined by the settings
in parameters L6-05 and L6-06.
The multi-function output
settings "18" and "19" in the
H2-oo parameter group are also
active if programmed.
0: Disabled
1: OL4 at Speed Agree - Alarm
(Overtorque Detection only
active during Speed Agree
and Operation continues after
detection).
2: OL4 at RUN - Alarm
(Overtorque Detection is
always active and operation
continues after detection).
3: OL4 at Speed Agree - Fault
(Overtorque Detection only
active during Speed Agree
and Drive output will shut
down on an OL4 fault).
4: OL4 at RUN - Fault
(Overtorque Detection is
always active and Drive
output will shut down on an
OL4 fault).
5: UL4 at Speed Agree - Alarm
(Undertorque Detection is
only active during Speed
Agree and operation
continues after detection).
6: UL4 at RUN - Alarm
(Undertorque Detection is
always active and operation
continues after detection).
7: UL4 at Speed Agree - Fault
(Undertorque Detection only
active during Speed Agree
and Drive output will shut
down on an OL4 fault).
8: UL4 at RUN - Fault
(Undertorque Detection is
always active and Drive
output will shut down on an
OL4 fault).
0 to 8
0
No
A
A
A
A
A
4A4H
Torq Det 2
Sel
L6-05
Torque
Detection
Level 2
Sets the Overtorque/
Undertorque detection level as
a percentage of Drive rated
current or torque for Torque
Detection 2. Current detection
for A1-02 = 0 or 1. Torque
detection for A1-02 = 2 or 3.
0
to
300
150%
No
A
A
A
A
A
4A5H
Torq Det 2
Lvl
L6-06
Torque
Detection
Time 2
Sets the length of time an
Overtorque/Undertorque
condition must exist before
torque detection 2 is recognized
by the Drive.
0.0
to
10.0
0.1sec
No
A
A
A
A
A
4A6H
Torq Det 2
Time
Parameter
Number
Name
Description
Setting
Range
Factory
Setting
Change
during
Operation
Control Methods
MODBUS
Register
Display
V/f
V/f
with
PG
Open
Loop
Vector
1
Flux
Vector
Open
Loop
Vector
2