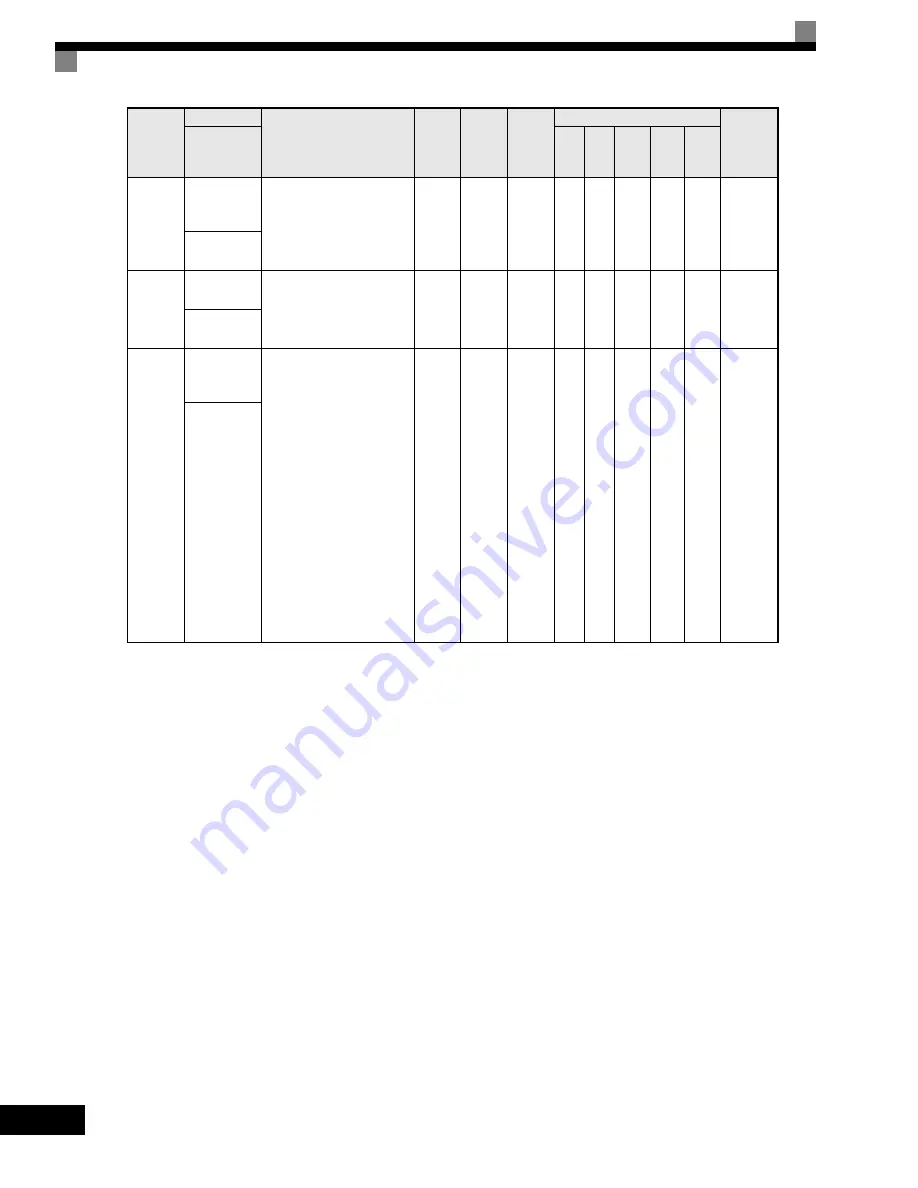
5
-40
* 1. The factory setting depends upon the Drive capacity. The value for a 200-240V class Drive of 0.4 kW is given.
* 2. The setting range is 10% to 200% of the Drive's rated output current. The values for a 200-240V class Drive of 0.4 kW is given.
* 3. If a multi-function input is set for motor 2 (H1-
= 16), the factory setting will depend upon the Drive capacity. The value for a 200-240V class
Drive of 0.4 kW is given.
E4-09
ASR
Proportional
Gain - Motor 2 Sets the proportional gain for
the speed control loop (ASR.)
0.00
to
300.00
*2
20.00
*
3
Yes
No
A
No
A
A
33FH
ASR P Gain
Mtr2
E4-10
ASR Integral
Time - Motor 2 Sets the speed control loop
(ASR) integral time in seconds.
0.000
to
10.000
0.500s
*
3
Yes
No
A
No
A
A
340H
ASR I Time
Mtr2
E4-11
Torque
Compensation
Gain – Motor 2
Magnifies the torque
compensation gain.
Normally this parameter does
not require change, however
adjustments can be made as
follows:
- When the motor cable is
long, increase the setting.
- When using a motor with a
smaller capacity than the
drive (the largest motor
being used), increase this
setting.
If the motor begins to
vibrate, adjust the value set
so that the output current
doesn't exceed the drive's
rated output current when
operating at low speeds.
0.00
to
2.50
1
Yes
A
A
A
No
No
341H
TrqCmp Gain
Mtr2
Parameter
Number
Name
Description
Setting
Range
Factory
Setting
Change
during
Operation
Control Methods
MODBUS
Register
Display
V/f
V/f
with
PG
Open
Loop
Vector
1
Flux
Vector
Open
Loop
Vector
2