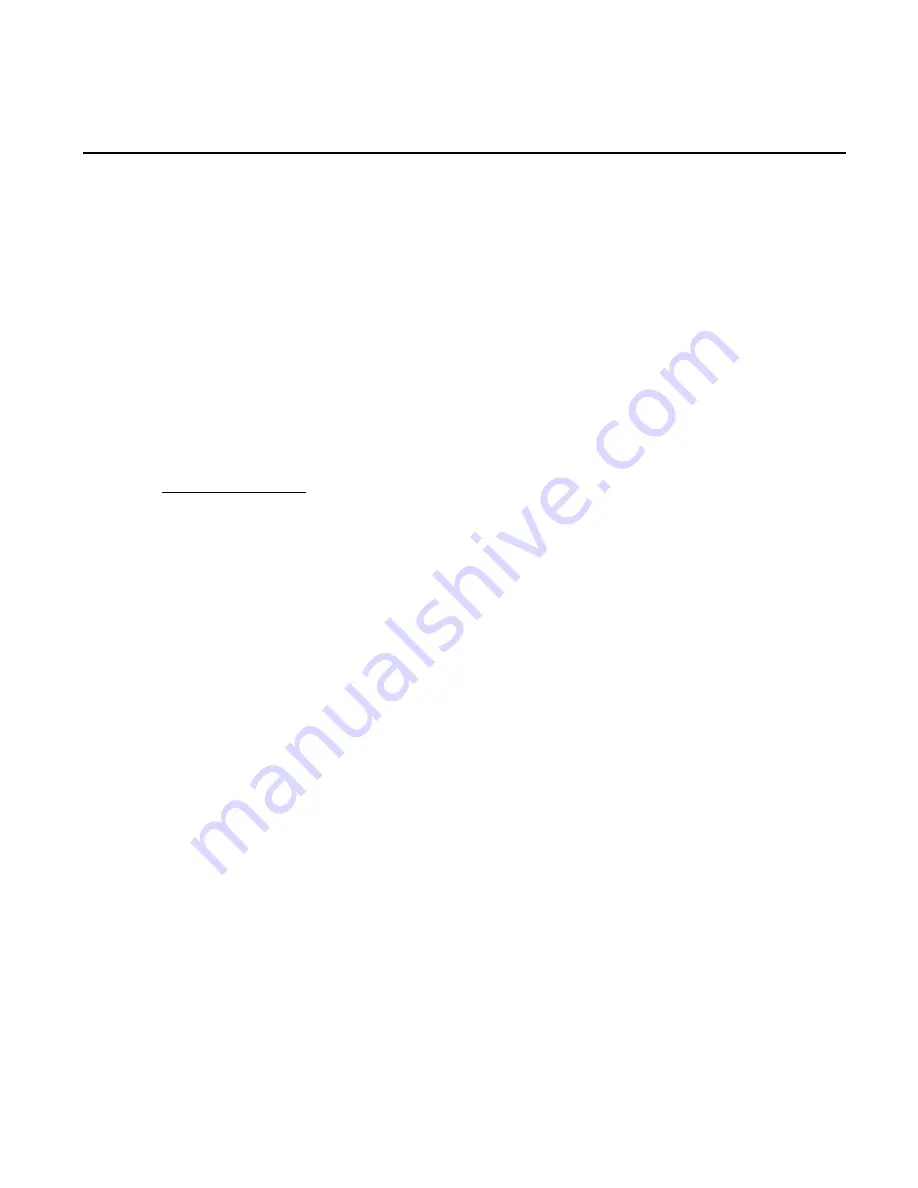
OPERATING & MAINTENANCE INSTRUCTION MANUAL
MODELS 427A (R-1), 428A (R-2), AND 429A (R-3) WELD HEADS
REV. AB
MODEL 514 TUBEMASTER OR 515/516 PIPEMASTER POWER SUPPLY
45
THESE DOCUMENTS, AND THE CONTAINED INFORMATION HEREIN, ARE PROPRIETARY AND ARE NOT TO BE REPRODUCED, USED OR DISCLOSED TO
OTHERS FOR MANUFACTURE OR FOR ANY OTHER PURPOSE, EXCEPT AS SPECIFICALLY AUTHORIZED, IN WRITING, BY MAGNATECH, LLC
The preceding information is meant only as a general guideline for the inexperienced operator. These
guidelines will allow the operator to become familiar with the equipment and do limited weld development
while developing his or her own technique. It is important to remember to record any and all changes made
to the weld procedure. Make only one change at a time. By making only one change at a time you will be
able to see the effect it has on the weld puddle and the ID reinforcement. One important thing to remember
is that it will take time to become proficient with this equipment. You will make mistakes - don't become
discouraged. Understanding what went wrong and being able to correct the mistake is the most important
thing. The learning curve varies, but generally is about two or three weeks long, depending on how much
hand on time is available. Also be aware that automatic welding (mechanized welding) is not a cure all for
all job problems.
Problems with the operation of this system most often are caused by to little training ("not enough hands on
time"), and bad fit up. When using automatic welding for repetitive welds, consistency is the name of the
game. Bevel geometry, pipe end fit up, tungsten angle, must be consistent. Any change in these may
result in a weld defect. A consistent fit up and bevel will produce consistently perfect welds with the right
procedure.
12.8.3
Tack Welding Programs
Generally, tube and pipe joints are tack welded together manually. Care must be taken when making the
manual tack welds in terms of appropriate gas coverage and lack of oxidation, and sufficient penetration to
hold the two tube ends during welding operations. The goal is that the tack welds will be consumed by the
weld bead and be undetectable in the finished weld.
It is possible to use the Weld Heads to tack two tubes together or tube-to-fittings. Even if the weldment is
fixtured, tack welding may be necessary to prevent distortion during welding and possible unacceptable fit
up during the final half of the welding program.
To use the Tubemaster Power Source for tack welding, use the Autotack Program (see
, Example
of Tack Weld Programs
).
Two programs are enclosed to create four tack welds around the circumference or 24 tack welds around the
circumference of the joint. Amperage levels and time duration may have to be altered for a different wall
thickness and materials. The RPM, however, should be suitable for any size tube.
Generally, an amperage of 10 amps or higher would have to be used on low pulse current to sustain the arc
as it is being moved to the next high pulse or tack position. The low pulse amperage should not be enough
to melt metal.