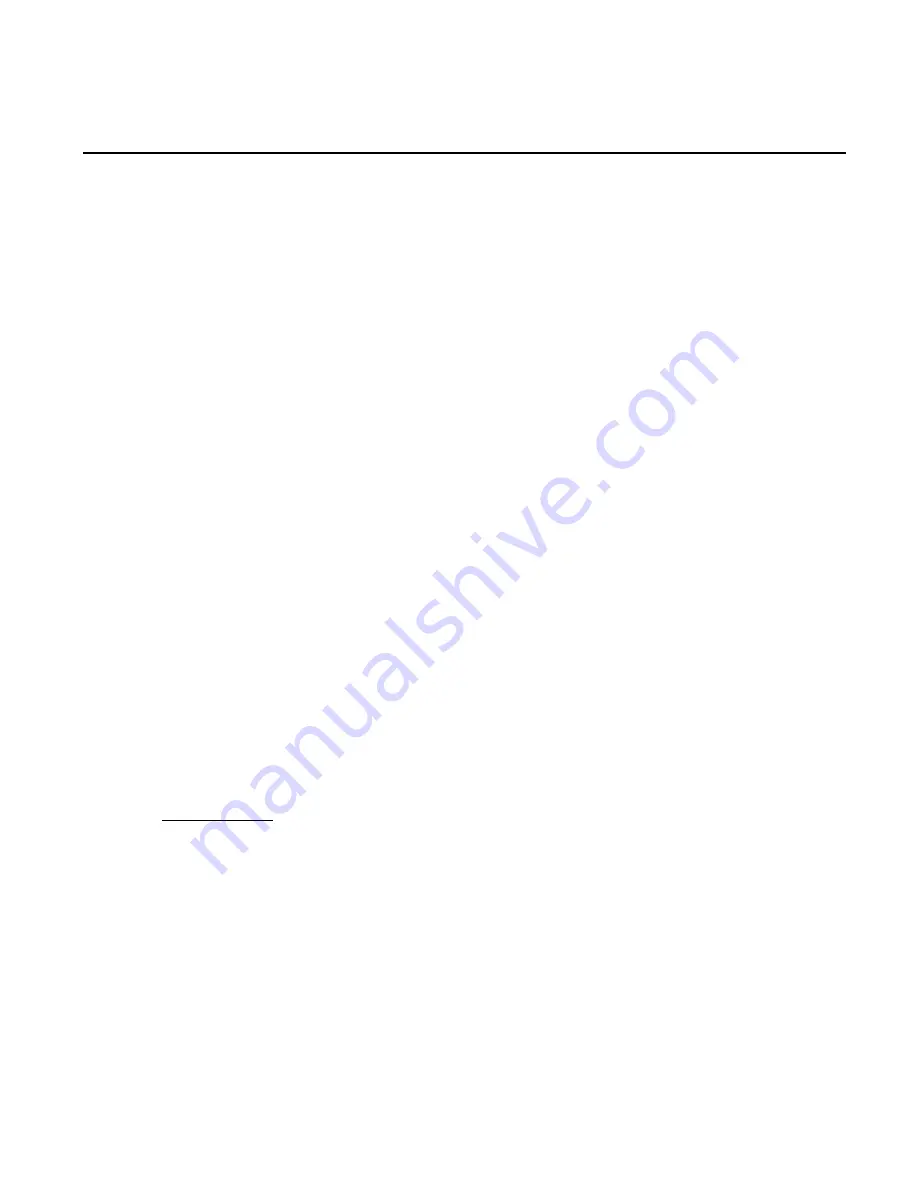
OPERATING & MAINTENANCE INSTRUCTION MANUAL
MODELS 427A (R-1), 428A (R-2), AND 429A (R-3) WELD HEADS
REV. AB
MODEL 514 TUBEMASTER OR 515/516 PIPEMASTER POWER SUPPLY
43
THESE DOCUMENTS, AND THE CONTAINED INFORMATION HEREIN, ARE PROPRIETARY AND ARE NOT TO BE REPRODUCED, USED OR DISCLOSED TO
OTHERS FOR MANUFACTURE OR FOR ANY OTHER PURPOSE, EXCEPT AS SPECIFICALLY AUTHORIZED, IN WRITING, BY MAGNATECH, LLC
Increase the High Pulse current
Increase high pulse time (0.2 minimum)
Decrease wire speed
Decrease travel speed
If the ID bead is too fluid, reduce low pulse heat input by changing one or more of the following:
Reduce Low Pulse Current (reduce % of High Pulse)
Increase Low Pulse time
Increase wire speed
If there is insufficient penetration on the ID, observe the chill marks on the weld surface. If chill mark
spacing is adequate, check that Low Pulse weld current is at least 50% of the High Pulse level. Increase
High Pulse weld current. (Be sure to record all changes.)
12.7
Hot Pass Procedure
Set wire to tungsten distance and insure the wire is aimed laterally directly under the tungsten. Ensure that
the hot pass is not causing the root bead to remelt, as this may result in "suckback" or concavity of a
previously acceptable root bead. If the root pass is being remelted, reduce weld current. Be sure weld
puddle is fusing the side wall. Check centering and correct if necessary. If the puddle runs ahead of the
tungsten on the downhill side, reduce wire speed. If the puddle is making "wagon tracks" on the side walls
reduce travel speed.
12.8
Fill Passes
Fill passes are typically run at higher wire speeds. Typical wire speeds are 30 - 75ipm (76-190cmmm).
Stringer beads should be run using continuous travel mode and continuous wire speed.
The Travel Step and Wire Step function are commonly used for single pass square butt joints. Travel step
can also be used with consumable inserts to control ID bead reinforcement in the 5G position.
If the weld bead is flat on the downhill side and convex on the uphill side, the Wire Step in conjunction with
the Travel Step function may be used to flatten the uphill side (wire speed 30 - 40"ipm (76-102cmpm).
12.8.1
Shield Gas Effects
100% argon is normally used for TIG welding. In certain cases a mixed gas can be used to advantage,
such as 95% argon, 5% hydrogen. This mixed gas is used for better control of the weld puddle and lower
heat input. (The addition of hydrogen or helium increases the arc voltage and creates a "stiffer" more
focused arc column.) Recommended for single pass welds only (stainless steel), mixed gases also increase
the chance of cold cracking on multi-pass welds. To reduce the possibility of a cold cracking a mixture of
argon/helium may be used (65/35%) for stainless steels and even higher amounts of helium for carbon
steel. (Increasing amounts of helium in the mixture will degrade arc starting.)