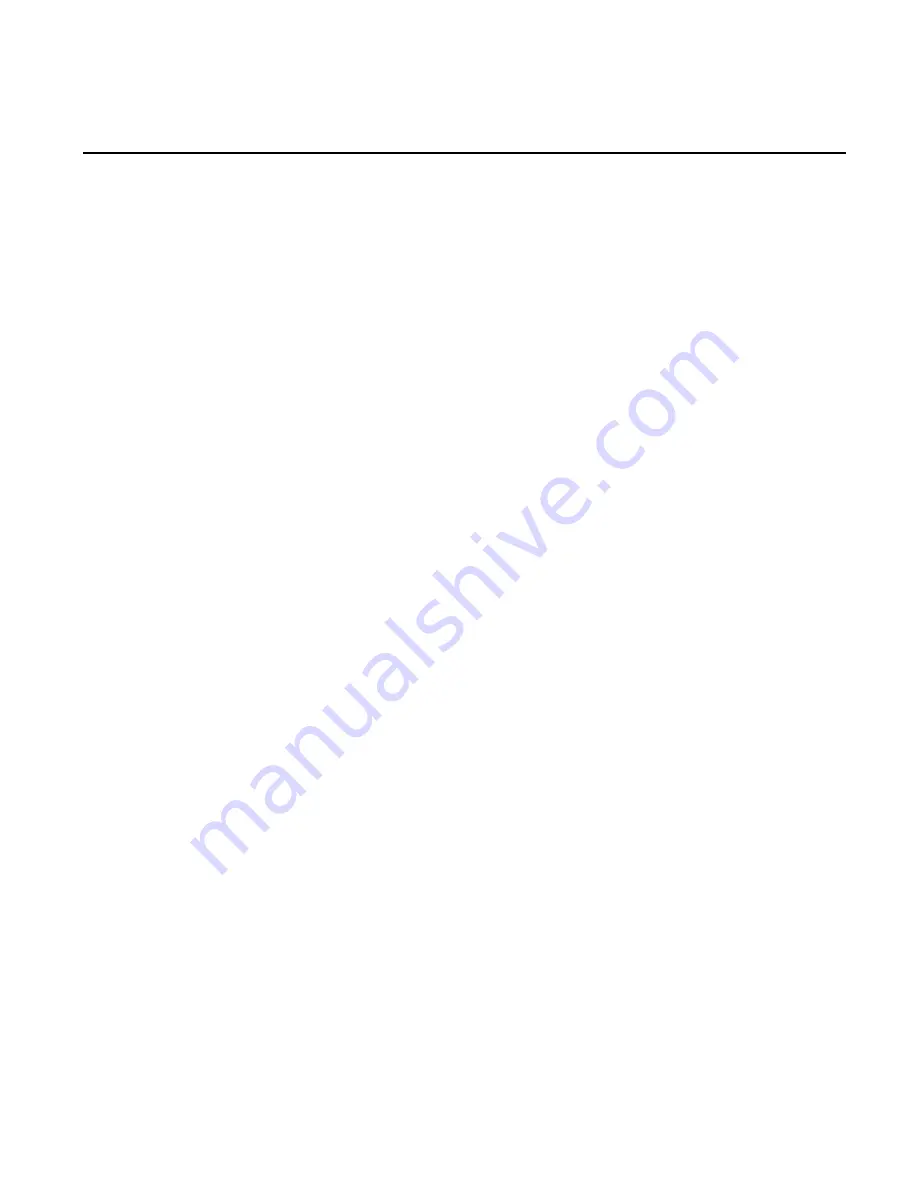
OPERATING & MAINTENANCE INSTRUCTION MANUAL
MODELS 427A (R-1), 428A (R-2), AND 429A (R-3) WELD HEADS
REV. AB
MODEL 514 TUBEMASTER OR 515/516 PIPEMASTER POWER SUPPLY
33
THESE DOCUMENTS, AND THE CONTAINED INFORMATION HEREIN, ARE PROPRIETARY AND ARE NOT TO BE REPRODUCED, USED OR DISCLOSED TO
OTHERS FOR MANUFACTURE OR FOR ANY OTHER PURPOSE, EXCEPT AS SPECIFICALLY AUTHORIZED, IN WRITING, BY MAGNATECH, LLC
The Redhead uses a special spool size. Empty spools (P/N 8831) are inexpensive and may be purchased
from Magnatech. Magnatech can also provide spools with all available alloys of filler wire. Wire is provided
with typical "Mill" certs suitably labeled and packaged.
The wire feed drive rollers are spring loaded together and do not require adjustment. If wire slippage is
observed it is caused by one of three problems:
1.
Wrong size filler wire for drive rolls.
2.
Something is preventing free rotation of the wire spool.
3.
V groove rolls are worn out and the V rolls must be replaced.
NOTE:
The wire spool mounting spindle has a factory preset friction device to provide "drag" and prevent
the wire from unspooling. Do not change this adjustment
9.11
Adjust Filler Wire Nozzle Position
Aim the filler wire with respect to the tungsten electrode using the following procedure (Refer to
Filler Wire Aiming Adjustments
):
1.
Set the cam (2) that serves as the fine vertical adjustment to its mid-stroke position. Loosen the "turret"
(3a) that holds the nozzle by loosening the screw (3). This turret serves as a gross vertical adjustment
of tungsten to wire and also allows the wire entry angle (A) to be set (this step presumes that the
tungsten stick-out (B) has already been properly adjusted). Rotate the turret until the proper angle and
tungsten-to-wire gap (C) is achieved and tighten the clamping screw (3).
2.
Adjust the wire nozzle stickout (D) by loosening the clamp screw (4) and sliding the nozzle in or out as
required. Retighten the clamp screw (4) when complete.
NOTE: DO NOT OVER TIGHTEN THE
CLAMP SCREW (4). YOU WILL CRUSH THE NOZZLE.
3.
Make the fine vertical adjustment using a 2.5mm hex driver in the cam screw (2). A tungsten to wire
gap of approximately 1/16" (1.5mm) is suitable.
NOTE
: A 180-degree rotation of the cam (2) produces the full range of adjustment.
4.
Using a 2.5mm hex driver adjust the lateral adjustment screw (1) to align the filler wire underneath the
tungsten electrode.
5.
Retract the wire using the jog switch so that it is at least 1/4" (6mm) away from the tungsten prior to
starting. The wire ends should not be close enough to the tungsten to either pickup or interfere with the
high frequency arc starting.
9.12
Check Torch Cross-Seam Adjustment
Position the torch over the center of the seam using the cross seam adjustment knob (see
Torch
Lead/Lag Adjustments for all Redheads
). If the cross seam adjustment device must be run to one extreme
end of its travel to center the torch, unclamp the Head and repeat the operation. It is necessary to allow
some cross seam adjustment in either direction to allow for out-of-square pipe ends and poor fit up.