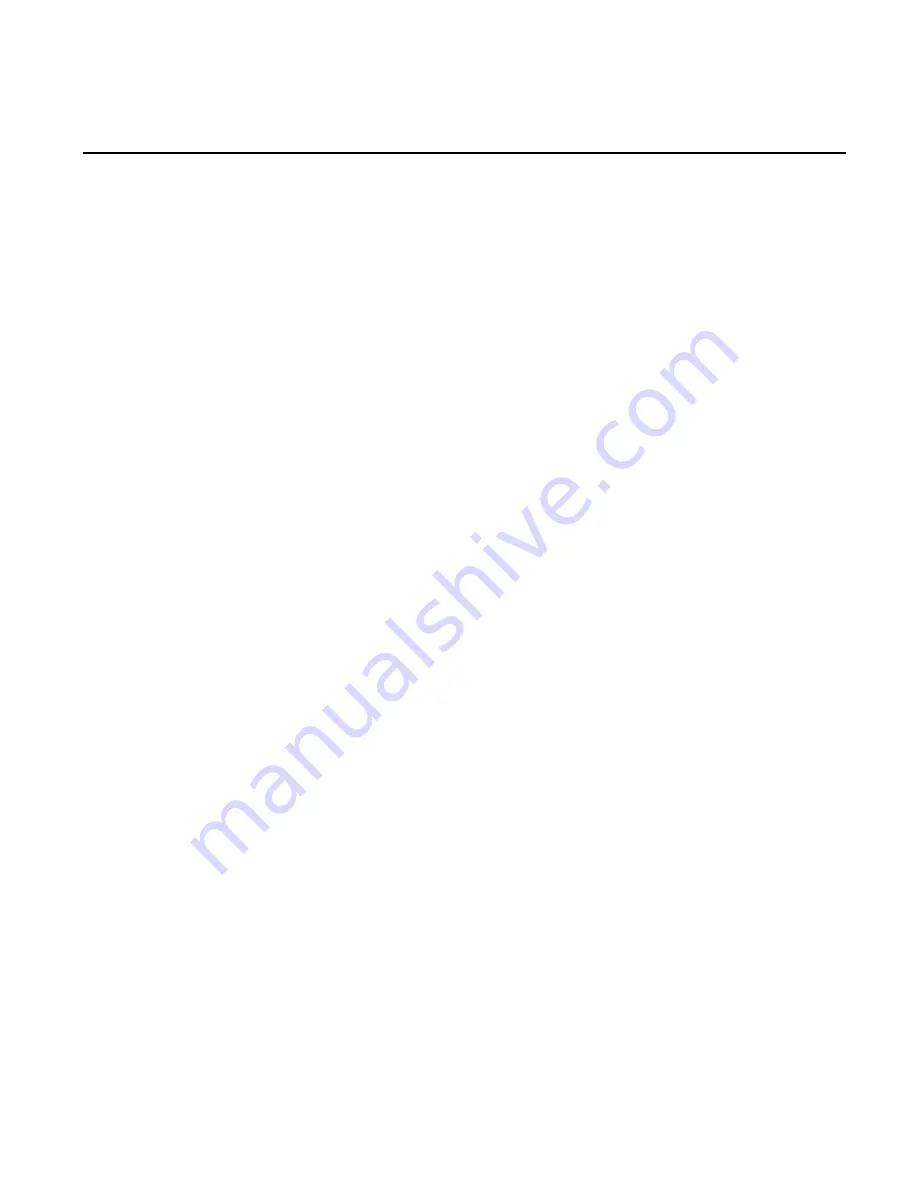
OPERATING & MAINTENANCE INSTRUCTION MANUAL
MODELS 427A (R-1), 428A (R-2), AND 429A (R-3) WELD HEADS
REV. AB
MODEL 514 TUBEMASTER OR 515/516 PIPEMASTER POWER SUPPLY
32
THESE DOCUMENTS, AND THE CONTAINED INFORMATION HEREIN, ARE PROPRIETARY AND ARE NOT TO BE REPRODUCED, USED OR DISCLOSED TO
OTHERS FOR MANUFACTURE OR FOR ANY OTHER PURPOSE, EXCEPT AS SPECIFICALLY AUTHORIZED, IN WRITING, BY MAGNATECH, LLC
9.7
Preparing the Workpiece
For successful mechanized welding it is necessary to ensure that the tube ends (or fittings) are machined
(beveled) square relative to their axis. The two ends are butt tightly together (or with a consistent gap,
depending on procedure). Magnatech can supply appropriate pipe beveling equipment to machine pipe
ends.
After the tube has been machined it must be properly cleaned using the following procedure:
1.
The tube end should be wiped with a lint free towel dipped in a solvent such as acetone or Freon and
immediately dried with a second clean cloth before the solvent has a chance to dry. On stainless
materials an abrasive cloth such as Scotchbrite™ should then be used to remove any surface oxides or
contaminants. Clean the tube end back to approximately 12mm (0.5").
2.
Repeat the solvent cleaning operation. Ensure that the pipe I.D. is similarly cleaned.
9.8
Clamp Head on Pipe
With the rotary plate in "open throat" position, slip the Head over the workpiece. This operation will be
simplified with the clamp in the fully retracted position. Once the Head has been slipped over the pipe,
rotate the clamp lever. This will extend the actuated jaw outward. The Weld Head need only be clamped
with sufficient force to prevent the weight of the cables from moving it during welding.
9.9
Adjust the Tension on the Torch Pivoting Arm
The torch pivoting arm should still be loose at this point. Rotate the Arc Gap adjustment screw (see
Torch Lead/Lag Adjustments for ALL Redheads
) to set a distance between the tungsten and pipe O.D.
Now adjust the spring tensioning screw (see
Torch Lead/Lag Adjustments for ALL Redheads
) by
rotating clockwise with the 2mm driver. Tighten until adequate spring force is achieved, testing periodically
by lifting the arm assembly off the pipe surface.
NOTE:
Do not over tension the leaf spring. The spring must be sufficiently tensioned to guarantee that the
arc gap adjustment screw is held against the pipe surface as it rotates. If the spring tensioning screw is
rotated clockwise to its limit, the leaf-spring will be “bottomed”. At this point it will be impossible for the
pivoting arm to move outward should this be required by an out-of-round workpiece.
9.10
Install the Wire Spool
If filler wire is required, install the wire spool on the spool mount assembly (
Note:
be certain that the wire
feed rolls and wire nozzle is appropriate for the wire size to be used. The Weld Head is equipped to feed
0.8mm [.035"] as a standard). Unscrew the knurled stainless steel retainer cover off of the wire spool
mounting spindle. Install the wire spool. The side of the spool that retains the end of the filler wire should
face upward. Reinstall the knurled retainer cover by screwing it down on the spool mount spindle unit it
bottoms. Once the spool is mounted the wire must be threaded through the drive system. Carefully unhook
the end of the wire from the retaining hole without losing control of the wire end. Using wire cutters remove
the bend end of the wire. File the end of the wire to remove any sharp edges or burrs and manually feed
the wire through the conduit from the spool to the feeder. The wire should feed directly to the V groove in
the wire feed rolls. Holding the wire in place with one hand, jog the wire feed motor using the switch on the
pendant. If the wire is jogged at low speed it should be possible to feed the wire through the outlet conduit
and out of the wire nozzle. If the sharp end of the wire catches in the radius of the conduit it may be
necessary to remove the nozzle to allow the conduit to be straightened. Run out of short length of wire to
eliminate any kinks or bends and cut it off at the nozzle.