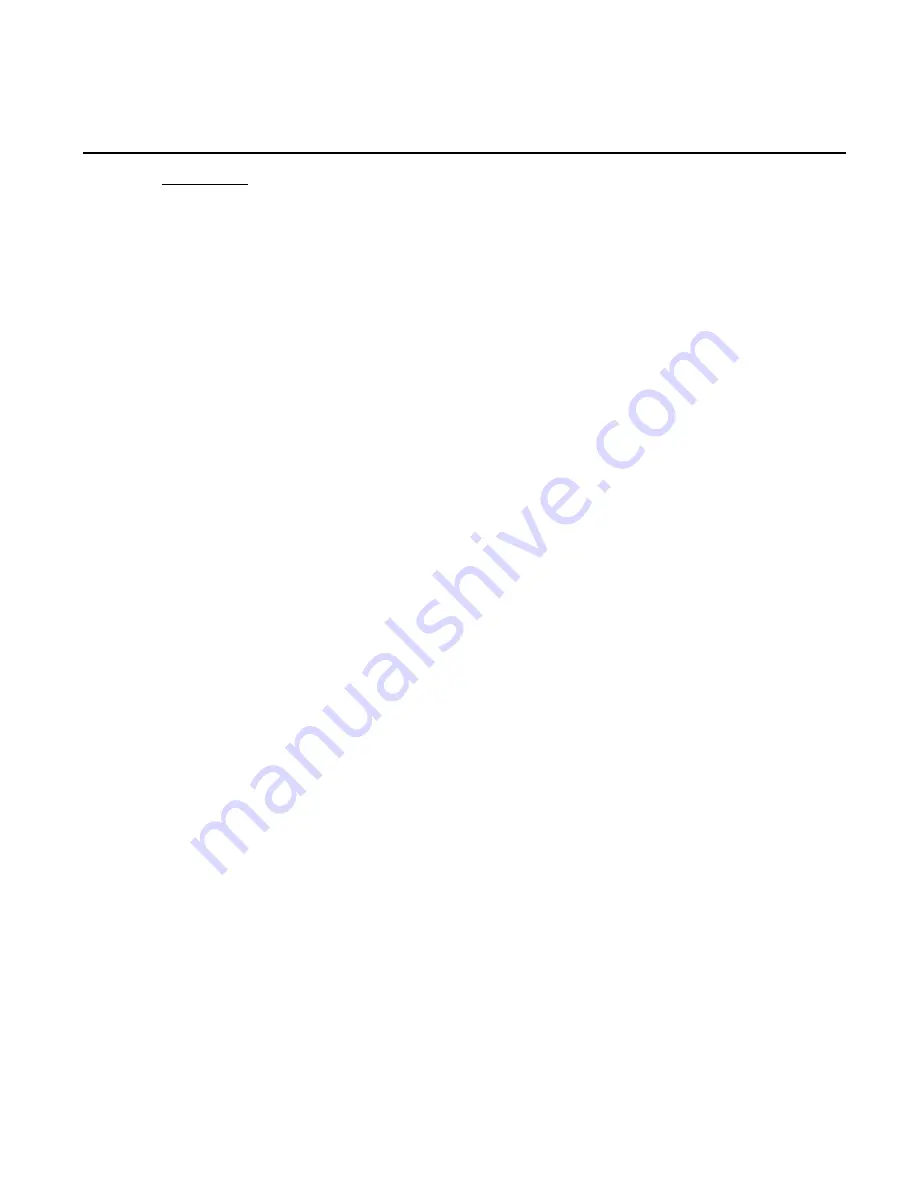
OPERATING & MAINTENANCE INSTRUCTION MANUAL
MODELS 427A (R-1), 428A (R-2), AND 429A (R-3) WELD HEADS
REV. AB
MODEL 514 TUBEMASTER OR 515/516 PIPEMASTER POWER SUPPLY
42
THESE DOCUMENTS, AND THE CONTAINED INFORMATION HEREIN, ARE PROPRIETARY AND ARE NOT TO BE REPRODUCED, USED OR DISCLOSED TO
OTHERS FOR MANUFACTURE OR FOR ANY OTHER PURPOSE, EXCEPT AS SPECIFICALLY AUTHORIZED, IN WRITING, BY MAGNATECH, LLC
For Example:
Carbon Steel, land thickness of .080" (2mm)
80 * 1.3 amps = 104 amps
104 + (104/3) = 135.5 amps High-Pulse
104 - (104/3) = 69.5 amps Low-Pulse
As a starting point, keep the high and low pulse times equal (0.3 seconds on, 0.3 seconds off).
Low Pulse current is always programmed as a percentage of High Pulse (rather than an actual value). If the
weld current is reduced to compensate for heat buildup in the pipe, both High and Low Pulse levels will go
down proportionally.
If the ID bead is too fluid, reduce low pulse heat input by changing one or more of the following:
Reduce Low Pulse Current (reduce % of High Pulse)
Increase Low Pulse time
If there is insufficient penetration on the ID, observe the chill marks on the weld surface. If chill mark spacing
is adequate, check that Low Pulse weld current is approximately one-third of the High Pulse level. Increase
High Pulse weld current. (Be sure to record all changes.)
12.5
Setting Filler Wire Speed
Filler wire speeds for the root pass are determined by prep geometry. For a square butt or a "J" Prep, 10 -
30ipm (25-76cmpm) are typical values. As the land thickness increases, wire speed should decreases. Fill
pass wire speeds range from 30 - 75ipm (76-190cmpm). For 360
°
orbital welding, the higher the wire
speed, the more it becomes necessary to use pulsillation to control the weld puddle size. Lead and lag
angles of the tungsten may also be used to control the weld puddle, but only when using a double-up or
double-down welding technique (T-Head only).
Wire feed can be continuous, or STEP MODE can be selected. In STEP MODE, two levels of wire feed are
synchronized with pulsed current. Wire feed during the Low current pulse time period is set as a percentage
(0-99%) of High Pulse wire feed speed. This feature is useful to control weld puddle size and to maximize
fill rate. It may not be possible to use the same wire feed speed for both High and Low current pulse
periods, but the amount of wire fed during Low pulse can be tailored to optimize solidification rate and
puddle control.
12.6
Root Pass Procedure
Filler wire to tungsten gap should be approximately 1/16" (1.5mm) (rule of thumb is 2/3 the diameter of the
tungsten). When welding a "J" prep, the wire entry into the weld puddle is correct when it appears that the
wire is standing still. Wire should feed smoothly into the front edge of the weld puddle. There should be no
drip or drag of the wire. When welding a 37-1/2 degree bevel, the wire should push slightly into the work.
The wire should enter the weld puddle directly under the tungsten. Arc length should be adjusted so wire
entry is correct. As the weld puddle partially solidifies during low current, the edge of the puddle freezes,
forming a circular "chill mark". Observe the chill marks on weld bead surface. If the chill marks are closer
than .8 * root land thickness, increase travel speed by 1/8ipm (3mmpm) until the desired reinforcement is
achieved. If the ID bead is almost solidified between current pulses, increase high pulse heat input
changing one or more of the following: