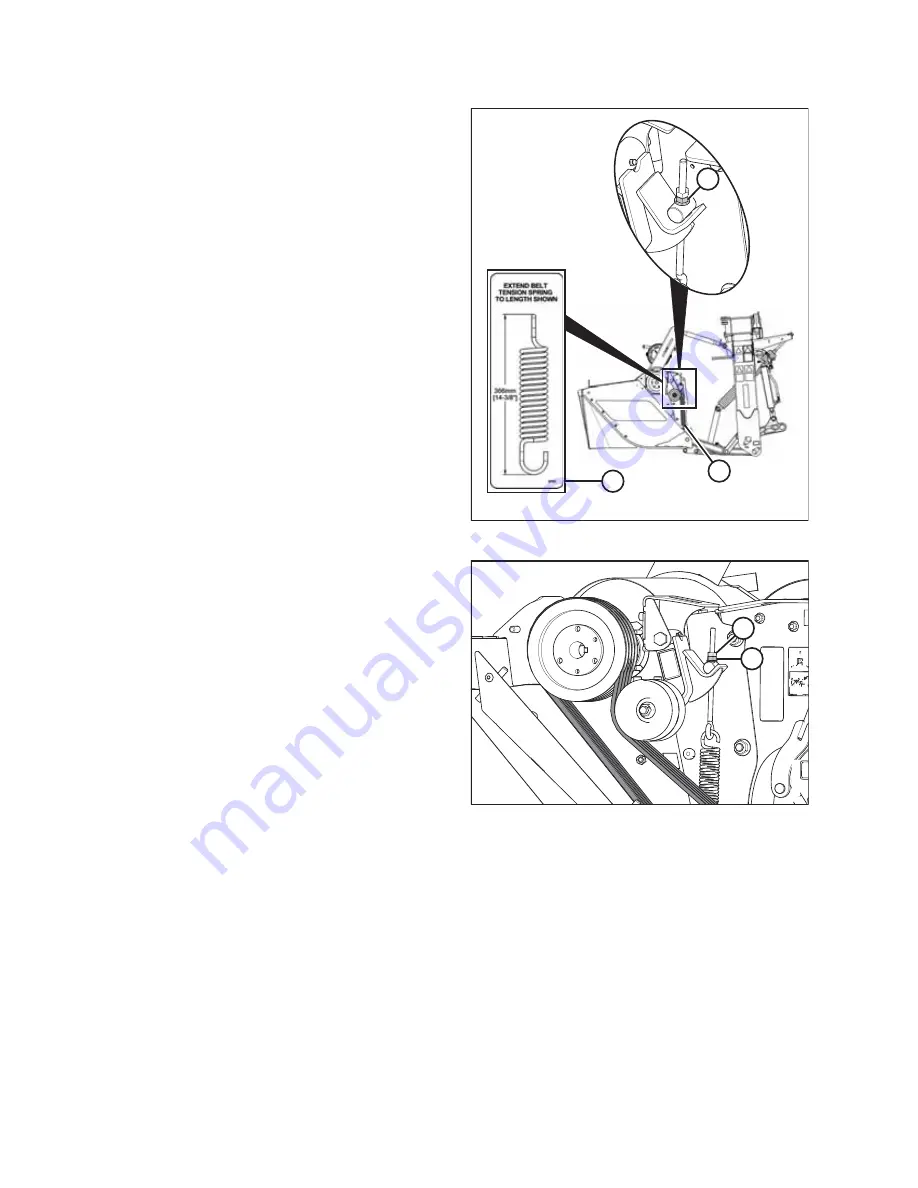
215333
110
Revision A
1022666
A
C
B
Figure 3.138: Spring Tension Decal
15. Measure the length of tensioner spring (A), and turn
adjuster nut (B) to adjust spring length to 36.5 cm
(14 3/8 in.) to conform with spring tension decal (C).
1033160
A
B
Figure 3.139: Conditioner Drive
16. Install jam nut (A).
17. Hold a wrench on adjuster nut (B) and turn jam nut (A)
clockwise into adjuster nut to lock the tension adjustment.
18. Verify that the pulleys run true and if any of the pulleys
wobble, return to Step
and repeat the
procedure to reinstall the taper locks on the affected
pulleys.