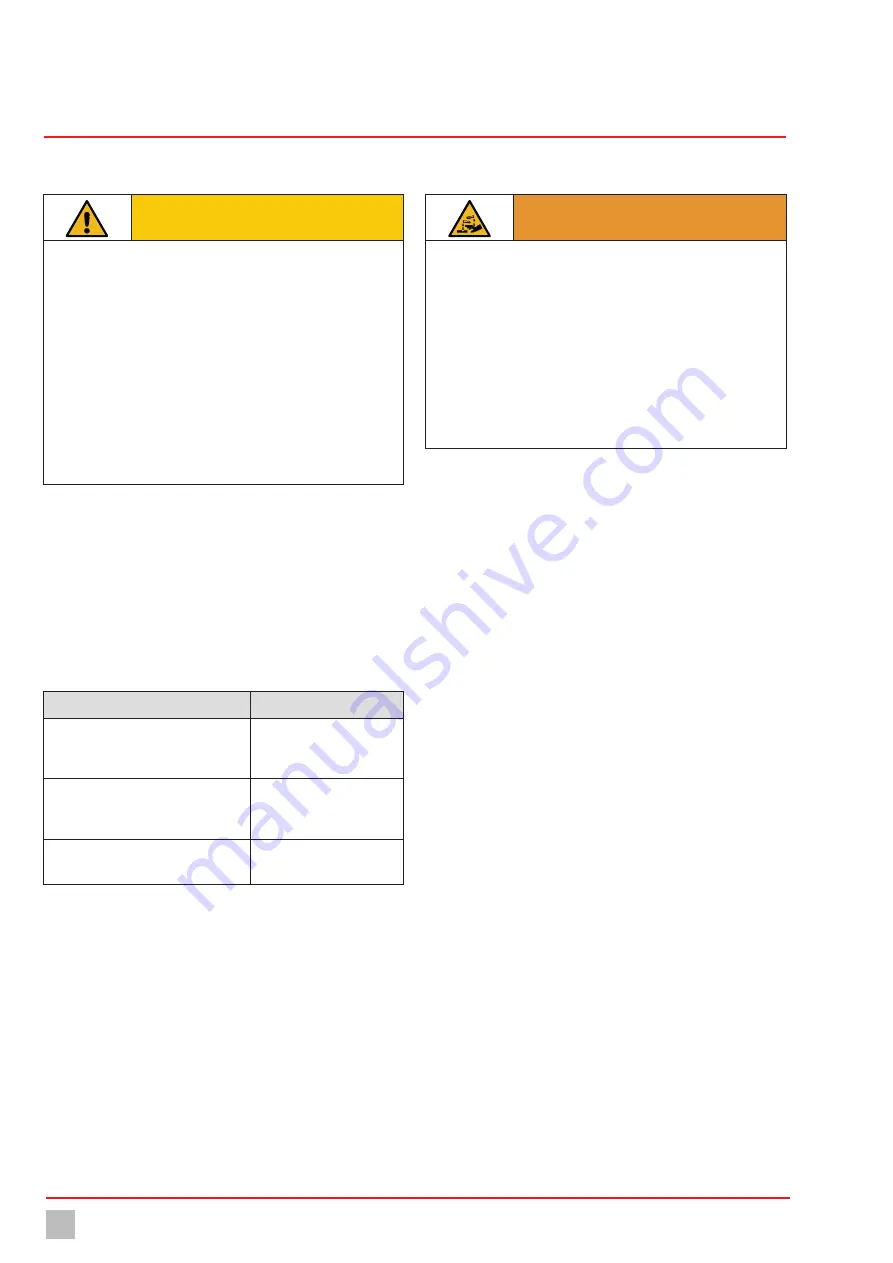
Disassembling
32
© Lutz-Jesco GmbH 2020
BA-62010-01-V01
Chlorine Dioxide System
EASYZON Dd
Operating Instructions
13 Disassembling
WARNING
Danger of injury when working on the components.
You may come into contact with dosing media when working on the
system components.
ð
Secure the system to prevent it from being turned on accidentally.
ð
Use sufficient personal protective equipment.
ð
Rinse the system before working on individual components so as to
remove dosing medium residue. Only use water.
ð
Release pressure in hydraulic parts.
ð
Never look into open ends of plugged pipelines and valves.
All the operations described herebelow as well as any action on the ma-
chine not merely consisting in setting parameters or adjusting the stroke
of the pumps shall be carried out wearing personal protective equipment,
such as anti-acid gloves, mask with activated carbon filter specific for
chlorine dioxide and anti-acid clothing.
Before disassembling the producer for transfer, repair or disposal rea-
sons, empty the chlorine dioxide in the reactor with the utmost care.
If the machine is still working, just pump water instead of chemical pro-
ducts for a few hours until the reactor is properly rinsed.
If the machine is faulty, let some water in by force, e.g. by means of a
pressurized rubber pipe at the inlet of the pumps or the reactor. The outlet
of the producer shall be diverted into a container that shall be closed at
the end of the operation and given to specialized firms for its disposal.
In both cases, the reactor outlet shall be plugged (just close the two ball
valves if the pre-dilution section is foreseen) before disassembling the
producer. In fact, if moved or placed horizontally the machine might leak
some dioxide residues.
Since the machine is to be classified as “special waste”, please contact
specialized firms or the supplier for its disposal.
12 Maintenance
CAUTION
Increased risk of accidents due to insufficient qualifica-
tion of personnel!
Chlorine dioxide systems and their accessories must only be installed,
operated and maintained by personnel with sufficient qualifications.
Insufficient qualification will increase the risk of accidents.
ð
Ensure that all action is taken only by personnel with sufficient and
corresponding qualifications. Comply with Chapter 2.5 „Personnel
qualification“ on page 7.
ð
Those performing system settings require an exact understanding
of their effects on the production process and operating behaviour.
Settings may only be performed by qualified service personnel.
ð
Prevent access to the system for unauthorised persons.
All routine and/or extraordinary maintenance operations shall be carried
out on the plant by skilled technical personnel only.
Power off the plant before carrying out any operation that may involve the
disassembling of hydraulic components of the plant. While performing
these operations always wear personal protective equipment, such as
anti-acid gloves, splash guard protection goggles and clothing made of
anti-acid material (e.g. PVC).
The main checks or routine maintenance operations that shall be carried
out at regular intervals are listed herebelow.
Maintenance
Intervals
Check the tightness of all pipings, joints,
valves and hydraulic components of the
installation at regular intervals.
regularly
Replace the dosing membranes and the
sets of seals of the dosing pumps and
reactor valves.
recommended: every six
months
max.: annually
Check that the flow sensors are properly
positioned
recommended: every week
max.: monthly
Tab. 17: Maintenance