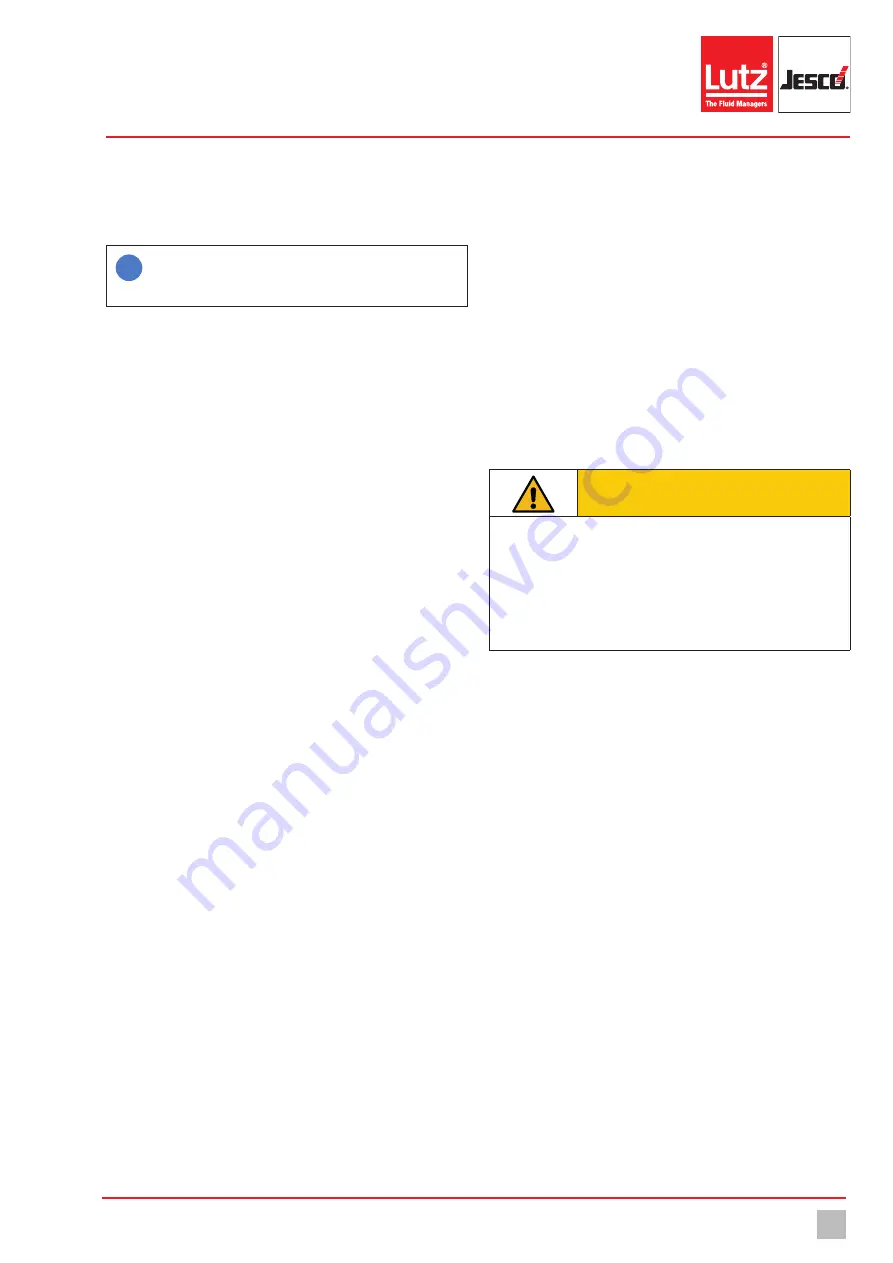
Installation
17
© Lutz-Jesco GmbH 2020
Subject to technical changes.
200922
BA-62010-01-V01
Chlorine Dioxide System
EASYZON Dd
Operating Instructions
7 Installation
7.1 General Notes
i
For installation, the local directions and regulations have to be
adhered to. This applies to the choice of suitable materials, the
handling of chemicals, the hydraulic and electrical installation.
The designer and operating company are responsible for ensuring that
the entire system, including the integrated equipment, are designed in
such a way that neither system equipment nor buildings are damaged in
the case of chemical leakage due to the failure of wearing parts (e.g.
pump hose) or burst hoses. The installation must be arranged in such a
way that even if the device breaks down no disproportionally high conse-
quential damages can arise. We therefore recommend installing leakage
monitors and collecting pans.
The functional security requires, depending on the application, the use of
suitable accessories, for example: injection nozzle and static mixer.
7.2 Installation location
The installation room of the production and dosing system must satisfy
the following requirements and specifications:
n
The room must be lockable and the chemicals must be stored in a
lockable room.
n
People are not permitted to remain in the room. An exception is pro-
vided by the presence in the room of only those chemicals required for
the continuation of works.
n
The room must be secured against access by unauthorised persons.
n
The room air temperature must lie between 5 °C and 40 °C.
n
It must be possible to ventilate the room.
n
It must be possible to dispose of chemicals safely (recommendation:
water connection, sink, water hose, floor drain with odour trap).
n
The room is to be marked with warning signs (hazard warnings and
safety precautions).
n
The installation location must be separated from other spaces by fire-
proof equipment.
The following must also be observed:
n
Install the system in such a way that permits easy access from all
sides. A minimum of a half a metre clearance to other objects from all
sides must be maintained. If the chemical containers are placed in di-
rect proximity to the system, space requirements can increase ac-
cordingly.
n
The device is to be mounted vertically. The underside of the unit
should be approx. 1 m above the ground.
n
The system is not intended for outdoor use.
n
Fluid, dust and other foreign objects may not be permitted to Enter the
components.
n
Avoid exposure to direct sunlight.
n
Relative humidity may not be permitted to exceed 92 %.
n
The atmosphere may not be condensing or corrosive.
n
An escape route must be present.
n
It must be possible to mount a gas warning device.
n
It must be possible to mount an emergency-stop switch outside the
room in which the chlorine dioxide system is located.
7.3 Mechanical installation
The mechanical installation of the producer consists in positioning the
panel on the wall where the cabinet containing the reactor and the dosing
pumps are installed; for large plants, we suggest you to lay the panel on
the floor and arrange a supporting kerb at least 10 cm high, and to secu-
rely fasten it to the wall.
The bottom panel of the production plant shall be fastened by means of
the four/six holes (d. 10 mm) at the top and bottom of the structure itself.
For small plants the height from the floor may vary from 40 to 70 cm
compared to the base of the dosing pumps, for larger plants from 10 to
30 cm.
7.4 Pre-dilution circuit
CAUTION
Siphoning risk of the chemicals!
Siphoning risks occur when – while using the pre-dilution circuit - the
dosage is executed in an open system (e.g. a tub), in a point that is
lower than the base of the reagents storage tanks.
ð
Always foresee a hydraulic rupture of the siphon also when using
special anti-siphon valves.
Before being put into the water to be treated, chlorine dioxide shall be
dosed in a derived pre-dilution circuit, whose aim is to favour and accele-
rate its dilution as well as to avoid conveying the concentrated solution up
to the point of dosage.
The pre-dilution water (ca. 500 – 1000 l/h) can be drawn from a piping, a
tub or a pressurized network by means of a recirculation pump. The flow
of pre-dilution water shall then be conveyed as far as the producer and
from there to the point of dosage.
The pipings used for the circuit above may be made of rigid PV-U, PVC-C
or PVDF, or black polyethylene with PVDF inside covering. The piping dia-
meter shall be the same of the connections placed on the machine.
7.5 Additional connections
n
Foot valves are placed into the storage tanks and are connected to the
suction of the dosing pumps by means of a soft PVC pipe (see tTab. 9
„Dimensions“ on page 16 for its diameter).
n
Minimum level switches are placed into the storage tanks and are
connected to the electronic control unit.