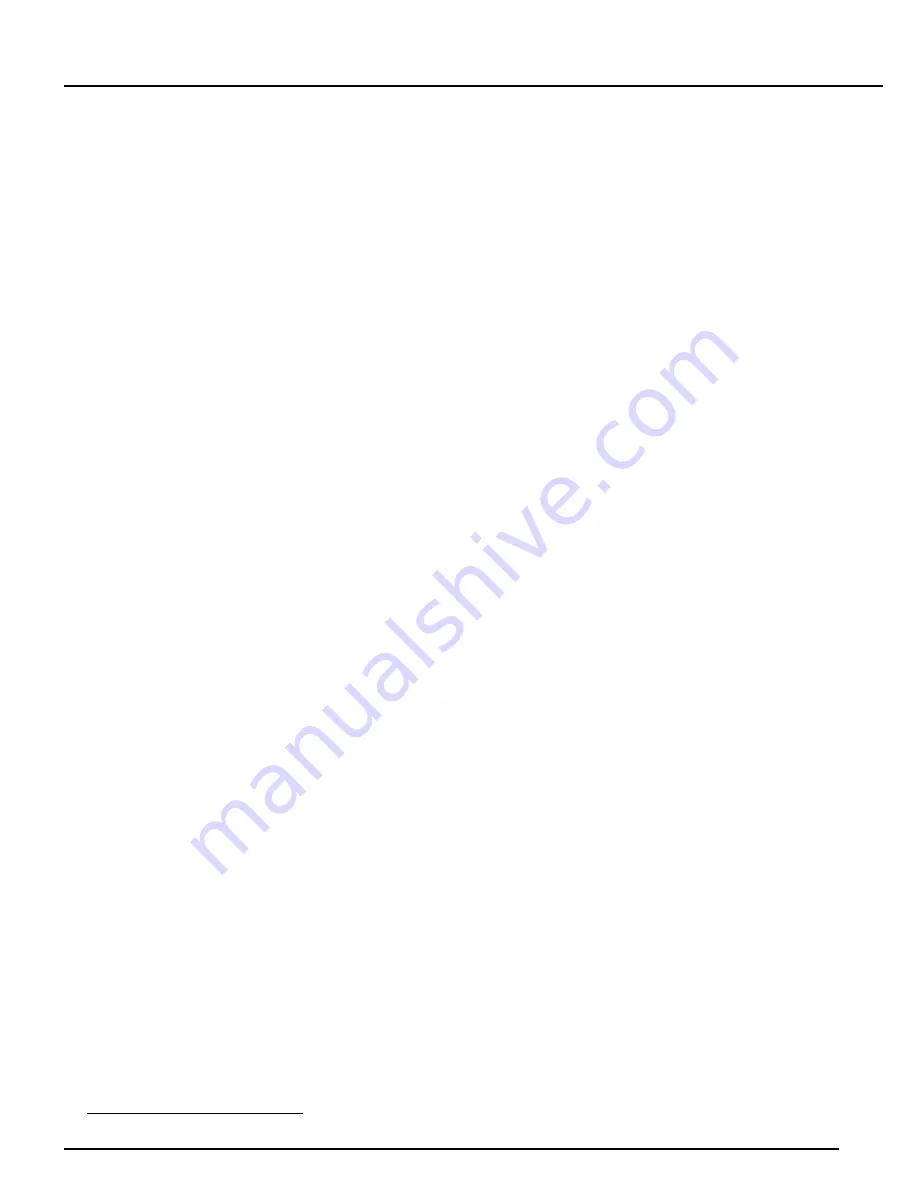
Logosol Multifunctional Servo Drive LS-231g2SB
Doc # 712231006 / Rev. B, 12/26/2017
Logosol, Inc.
•
•
•
•
2833 Junction Ave., Ste. 101
•
•
•
•
San Jose, CA 95134
•
•
•
•
Tel: (408) 744-0974
•
•
•
•
www.logosolinc.com
41
smaller error. In general, accuracy of an approximated path will be a function of the number of path points
used, and the radius of the curve.
Because LS-231g2SB uses a fixed number of points per second, moving more slowly will result in a more
accurate path than moving quickly. Also, a higher frequency path will be more accurate than a lower
frequency path. The main advantages of using a slower path, however, are that fewer path points need to
be calculated, less data needs to be sent to the controllers, and the path point buffer will last longer.
The maximum absolute path error can be approximated by the formula:
Error = R x ( 1 - cos( V / ( 2xFxR ) ) )
*
where
R
is the radius of the curve (in inches),
V
is the velocity of the motion (in inches/sec), and
F
is the
path point frequency. For example, a one-inch diameter circle with a velocity of 1 inch per second and a
path frequency of 30 Hz would have a maximum error of 0.00028 inches.
Timing Errors
If the timing of multiple axes is not perfectly synchronized, there will be a deviation from the desired path
from the fact that one axis will be ahead or behind in time. The exact deviation will depend on the path
geometry.
The first type of timing error results from multiple axes not starting at exactly the same time. When a “start
path” command is issued to a group of controllers, they will all start /- 0.000025 seconds of one
another.
The second type of timing error results from inaccuracies in the frequencies of the oscillators running on
each
LS-231g2SB
controller. (If all Servo Drives are timed from the same oscillator, this error is zero.)
Typical oscillator variations (for the same operating temperature) are about 10 parts per million. Therefore,
after running a path for 10 seconds, for example, the timing error would be about +/-0.0001 seconds.
By adding both of these timing errors together, and then multiplying by the path velocity, we get the total
distance that one axis can be ahead of another axis. For a 10 second motion, while moving at 1 inch per
second, we could have one axis moving ahead of another by at most 0.000125 inches. The actual worst-
case deviation (moving along a 45 degree angle) will produce an error from the ideal path of 0.000125
inches. Over a total distance of 10 inches traveled, this gives a basic accuracy of ±0.0000125 inches per
inch of travel. Other examples, of course, will produce different accuracy figures.
Note that errors due to timing only accumulate during a coordinated motion and are, in essence, reset
with each new move. Therefore, if errors due to timing do become a problem, the paths should be broken
up into shorter moves.
Eliminating those errors is possible by enabling the hardware synchronization mode using
Enable /
Disable hardware synchronization mode
command.
*
The cosine function should be executed for an angle in radians.