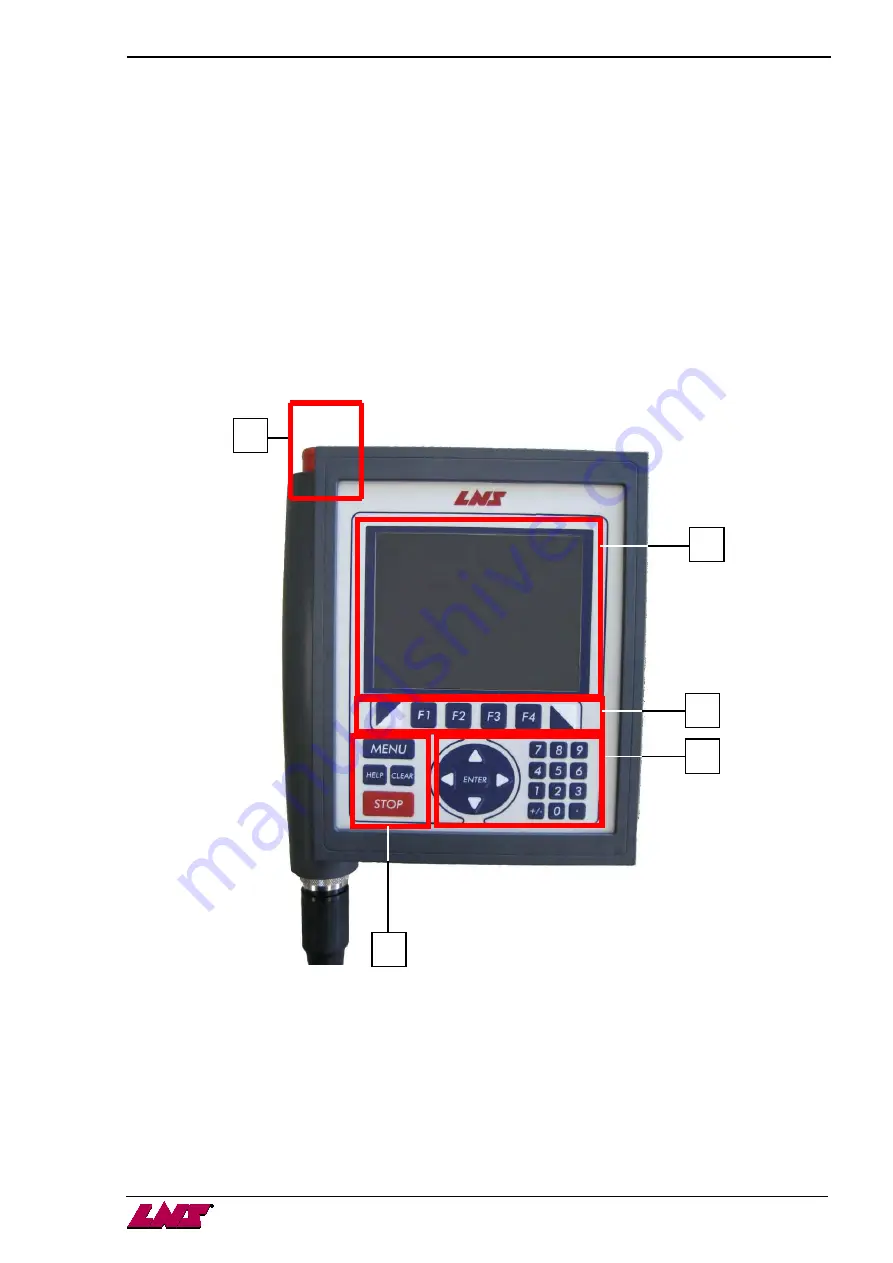
CHAPTER 7: OPERATION
73
QUICK LOAD SERVO S3T
2.
REMOTE CONTROL
The ergonomic and user-friendly remote control with a clear built-in display facilitates the handling of the
bar feeder. Depending on the sequence under way, the bar feeder gives access only to those functions
which are available, thus avoiding any incorrect handling, and reducing the access time to the necessary
functions.
The screen continuously and clearly shows the status of the bar feeder and the production, allowing the
functions, diagnostics and error signals to be checked or analysed at any time.
The most recent error signals are saved in a register and can be recalled to establish diagnostics.
The remote control has five distinct segments, namely: display
(A)
, function keys
(B)
, directional keys and
numeric pad
(C)
, modes keys with STOP, MENU and HELP buttons
(D)
, and the emergency button
(E)
.
A
B
C
E
D
Содержание SERVO S3 T
Страница 2: ......
Страница 5: ...CHAPTER 1 BASIC PRINCIPLES 3 QUICK LOAD SERVO S3T CHAPTER 1 BASIC PRINCIPLES...
Страница 11: ...CHAPTER 2 TECHNICAL DATA 9 QUICK LOAD SERVO S3T CHAPTER 2 TECHNICAL DATA...
Страница 13: ...CHAPTER 2 TECHNICAL DATA 11 QUICK LOAD SERVO S3T 2 1 Loading from the rear left transverse movement...
Страница 14: ...12 CHAPTER 2 TECHNICAL DATA QUICK LOAD SERVO S3T 2 2 Loading from the rear left longitudinal movement...
Страница 15: ...CHAPTER 2 TECHNICAL DATA 13 QUICK LOAD SERVO S3T 2 3 Loading from the front left transverse movement...
Страница 16: ...14 CHAPTER 2 TECHNICAL DATA QUICK LOAD SERVO S3T 2 4 Loading from the front left longitudinal movement...
Страница 18: ...16 CHAPTER 2 TECHNICAL DATA QUICK LOAD SERVO S3T...
Страница 19: ...CHAPTER 3 SYSTEM START UP 17 QUICK LOAD SERVO S3T CHAPTER 3 SYSTEM START UP...
Страница 35: ...CHAPTER 4 ELECTRICS 33 QUICK LOAD SERVO S3T CHAPTER 4 ELECTRICS...
Страница 45: ...CHAPTER 4 ELECTRICS 43 QUICK LOAD SERVO S3T 3 ELECTRIC DIAGRAMS...
Страница 49: ...CHAPTER 5 PNEUMATICS 47 QUICK LOAD SERVO S3T CHAPTER 5 PNEUMATICS...
Страница 54: ...52 CHAPTER 5 PNEUMATICS QUICK LOAD SERVO S3T...
Страница 55: ...CHAPTER 6 GENERAL DESCRIPTION 53 QUICK LOAD SERVO S3T CHAPTER 6 GENERAL DESCRIPTION...
Страница 73: ...CHAPTER 7 OPERATION 71 QUICK LOAD SERVO S3T CHAPTER 7 OPERATION...
Страница 105: ...CHAPTER 8 MALFUNCTIONS MAINTENANCE 103 QUICK LOAD SERVO S3T CHAPTER 8 MALFUNCTIONS MAINTENANCE...
Страница 116: ...114 CHAPTER 8 MALFUNCTIONS MAINTENANCE QUICK LOAD SERVO S3T...
Страница 117: ...CHAPTER 9 APPENDICES 115 QUICK LOAD SERVO S3T CHAPTER 9 APPENDICES...