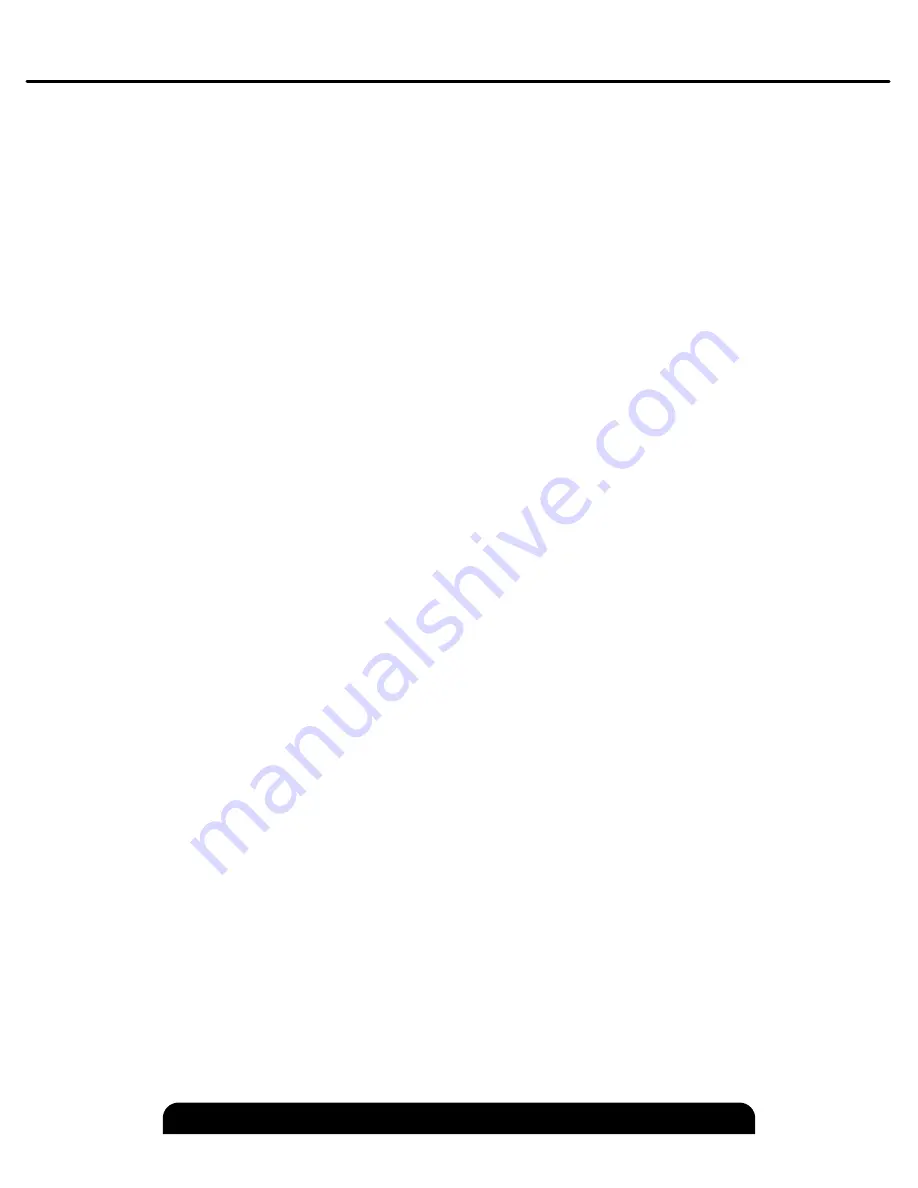
www.lionprecision.com/two-year-warranty/
Document No. M017-7500.004
43
Oakdale, MN, USA www.lionprecision.com 651-484-6544
Many of the definitions here are taken from ASME B89.3.4-2010: Axes of Rotation: Methods for
Specifying and Testing.
Asynchronous error motion
- the portion of the total error motion that occurs at frequencies
other than integer multiples of the rotation frequency. Asynchronous error motion comprises
those components of error motion that are: (a) not periodic (b)periodic but occur at frequencies
other than the spindle rotational frequency and its integer multiples, (c) periodic at frequencies
that are subharmonics of the spindle rotational frequency.
Asynchronous error motion value
- the maximum scaled width of the asynchronous error
motion polar plot, measured along a radial line through polar chart center.
Axial error motion
- error motion coaxial with the Z reference axis. Axial slip, end-camming,
pistoning and drunkenness are common but inexact terms for axial error motion.
Axial thermal drift
- applicable when the displacement is collinear with the Z reference axis.
Axis average line
- a line segment passing through two axially separated radial motion polar
profile centers. The axis average line is used to describe the unambiguous location of an axis of
rotation with respect to the reference coordinate axes, or changes in the location, for example,
in response to changes in load, temperature or speed.
Axis of rotation
- a line segment about which rotation occurs
Axis shift
– a change in position of the axis of rotation caused by a change in operating
conditions.
Bearing
- an element of a spindle that supports the rotor and allows rotation between the rotor
and the stator.
Displacement indicator
- a device that measures displacement between two specified objects.
Error motion
– changes in position, relative to the reference coordinate axes, of the surface of
a perfect workpiece, as a function of rotation angle, with the workpiece centerline coincident
with the axis of rotation.
Face error motion
– the sum of the axial error motion and the axial component of tilt motion
at the specified radius. Face error motion is parallel to the Z reference axis at a specified radial
location. The term “face runout” has an accepted meaning analogous to radial runout and hence
is not equivalent to face error motion.
Face thermal drift
- applicable to a combination of axial and tilt displacement measured at a
specified radial location.
Fixed sensitive direction
– the sensitive direction is fixed when the workpiece is rotated by
the spindle and the point of machining or measurement is not rotating.
Fundamental error motion
- that portion of the total error motion that occurs at the rotational
frequency of the spindle. Fundamental axial and fundamental face motions are error motions
and cause flatness errors on parts. However, fundamental error motion will create a part with
the property of circular flatness: The surface is flat and will provide a “sealing surface” at any
given radius. This unique property is important to the hydraulic industry. Fundamental radial and
fundamental tilt displacements are not error motions because they represent misalignment of
the artifact, not a property of the axis of rotation. Fundamental axial and fundamental face
motions are error motions and have important engineering consequences.
Fundamental error motion value
- twice the scaled distance between the PC center and a
specified polar profile center of the synchronous error motion polar plot. Alternatively defined as
the amplitude of the rotational frequency component. The value is twice the amplitude because,
in this case, amplitude represents the average-to-peak value rather than the peak-to-peak
value. Fundamental axial value and fundamental face value are the same value. There is no
fundamental radial error motion value - in the radial direction, motion that occurs at the
rotational frequency is caused by an off-center reference target and is not a property of the axis
of rotation.
GLOSSARY