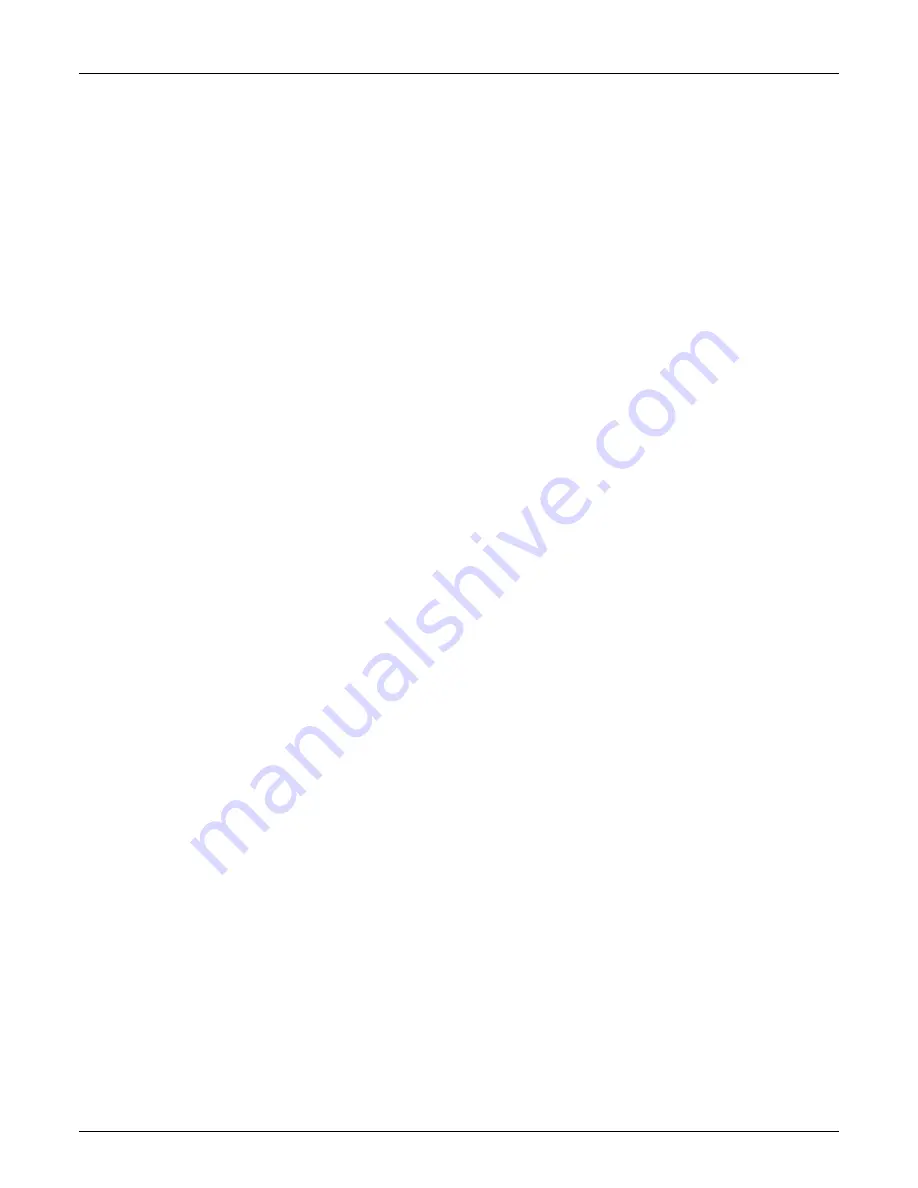
Spirit II User’s Manual
Section 2: Specifications
This information is subject to the controls of the Export Administration Regulations [EAR]. This information shall not be provided to
non-U.S. persons or transferred by any means to any location outside the United States contrary to the requirements of the EAR.
2-7
Gas Supply Requirements
Plasma gas types:
Mild Steel ..................................................... Oxygen
Stainless Steel ............................................ Air, Nitrogen, or H17
Aluminum .................................................... Air or Nitrogen
Shield gas types:
Mild Steel ..................................................... Oxygen or Air
Stainless Steel ............................................. Air or Nitrogen
Aluminum .................................................... Air or Nitrogen
Preflow gas type ............................................... Air or Nitrogen
Marking gas type............................................... Nitrogen or Argon/Air
Plasma gas flow rate (maximum):
Oxygen ........................................................ 78 scfh (2209 liters/hour)
Air ................................................................ 67 scfh (1897 liters/hour)
H17 or Nitrogen ........................................... 106 scfh (3002 liters/hour)
Shield gas flow rate (maximum):
Oxygen ........................................................ 19 scfh (538 liters/hour)
Air ................................................................ 258 scfh (7306 liters/hour)
Nitrogen ...................................................... 326 scfh (9231 liters/hour)
Preflow gas flow rate (maximum) ...................... 60 scfh (1699 liters/hour)
Marking gas flow rate (maximum) ..................... 89 scfh (2520 liters/hour)
Rated Inlet gas pressure ................................... 115 psi (7.9 bar)
Minimum Inlet gas pressure .............................. 105 psi (7.2 bar)
Maximum Inlet gas pressure ............................. 145 psi (10.0 bar)
Oxygen and nitrogen should be supplied with a purity of at least 99.5%.
H17 should be supplied with a purity of at least 99.995%.
A potential fire hazard exists when cutting with oxygen. It is recommended that
an exhaust ventilation system be used when cutting with oxygen. Flashback
arrestors must be supplied (unless they are not available for the chosen gases
and pressures) to prevent a possible fire from propagating back to the gas
supplies.
Ensure that oxygen lines remain free from contaminants such as oil and grease. The
mixture of such contaminants with oxygen presents an additional fire hazard.
Compressed air must be clean, dry, and oil-free and may be supplied from compressed
cylinders or from an air compressor. Be aware that shop air systems are prone to oil
and moisture contamination. If shop air is used, it must be cleaned to ISO 8573.1:
Class 1.4.1. Specify dry air when using compressed cylinders. Breathing quality air
contains moisture and must not be used.
3/8” (inside diameter) hoses are required for all inlet gas connections. Mating
connectors are available as an option.
Quick-connect fittings must not be used.