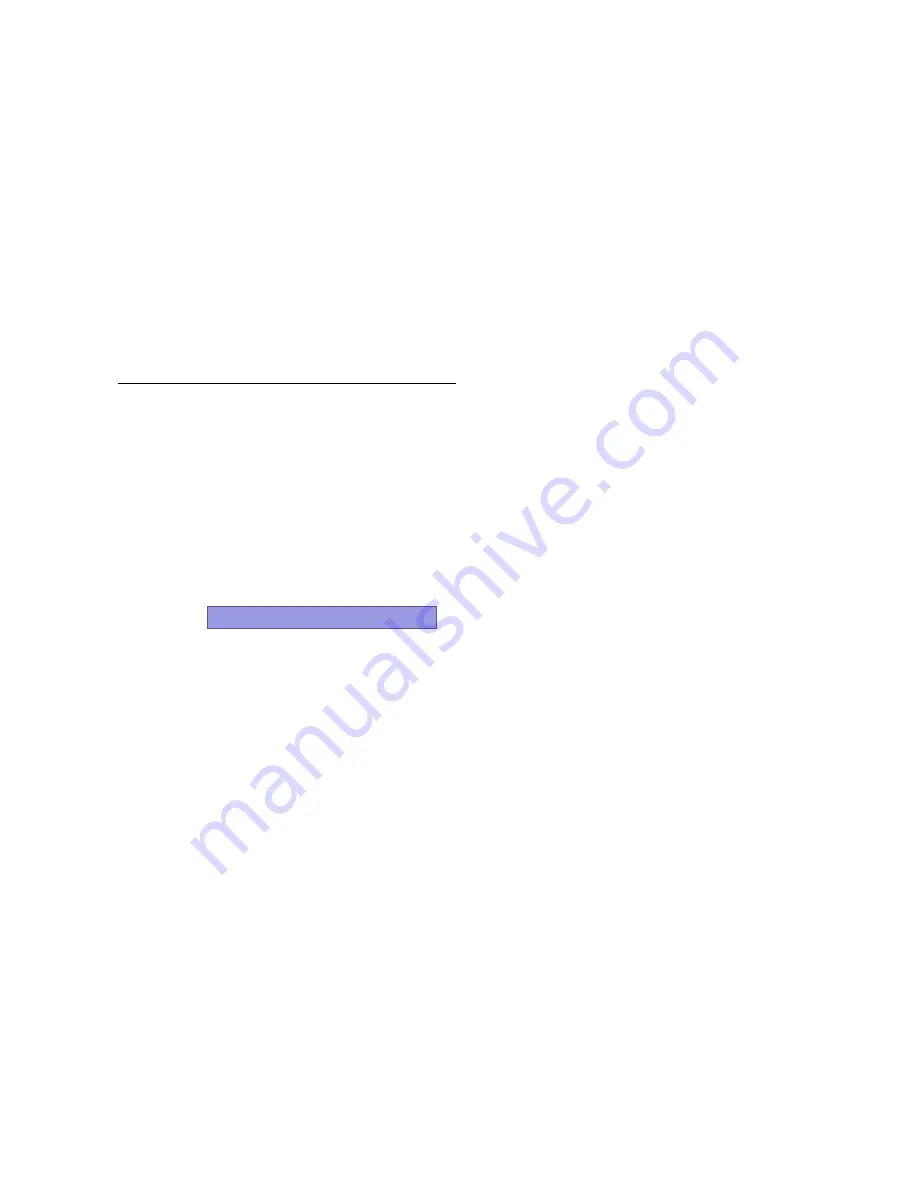
LINCOLN ELECTRIC
SAE-300® HE Service Manual
61
NOTE:
The sleeve collar will have to be removed with a gear puller. Be careful not to damage the
rotor slip ring assembly.
12.
Remove the rotor by pulling it free of the generator shaft.
REPLACEMENT PROCEDURE
1.
Carefully mount the rotor onto the generator shaft. Install a new sleeve collar (part number
T14337), washer and rotor locking nut.
NOTE:
Be careful not to damage or deform the new sleeve collar. Carefully tap the new sleeve
collar into position. The rotor locking nut should be torqued to 175 ft.-lbs.
After the rotor locking nut is properly torqued, bend the washer down over the locking nut.
2.
Check rotor air gap, .017" minimum is allowed.
3.
Mount the brush holder assembly to the stator frame using two bolts, washers and nuts
Installing and Seating Exciter Slip Ring Brushes
a. Make sure the slip rings are clean and free from oil and grease.
b. With the brushes in place, insert one end of a minimum 24" long piece of 180 grit sandpaper
between the slip rings and brushes (abrasive against brushes). Pull the paper around the
circumference of the rings in the direction of rotation only. Repeat this procedure until the entire
face of the brush is contoured to the radius of the slip ring.
c. Check the brushes to be certain that there is spring tension holding them firmly against the slip
rings.
4.
Install the alternator cover and wrap-around.
5.
Connect the negative battery cable.
6.
Attach the roof panel and close the left and right side panels.
7.
Perform the
Содержание SAE-300 HE
Страница 8: ...LINCOLN ELECTRIC SAE 300 HE Service Manual 3 Theory of Operation Figure F 1 Block Diagram ...
Страница 51: ...LINCOLN ELECTRIC SAE 300 HE Service Manual 46 Figure F 13 Rocker w marks ...
Страница 54: ...LINCOLN ELECTRIC SAE 300 HE Service Manual 49 Figure F 14 Brush spring Figure F 15 Windings insulated wedge ...
Страница 55: ...LINCOLN ELECTRIC SAE 300 HE Service Manual 50 Figure F 1 Insulator spring locations Figure F 2 Shaft tube ...
Страница 64: ...LINCOLN ELECTRIC SAE 300 HE Service Manual 59 Figure F 22 Rheostat terminal locations ...
Страница 68: ...LINCOLN ELECTRIC SAE 300 HE Service Manual 63 Figure F 25 Rotor removal ...
Страница 75: ...LINCOLN ELECTRIC SAE 300 HE Service Manual 70 Figure F 28 Sling lift ...
Страница 79: ...LINCOLN ELECTRIC SAE 300 HE Service Manual 74 Figure F 30 Current sense board plug location ...
Страница 83: ...LINCOLN ELECTRIC SAE 300 HE Service Manual 78 Figure F 32 Rheostat terminal locations ...