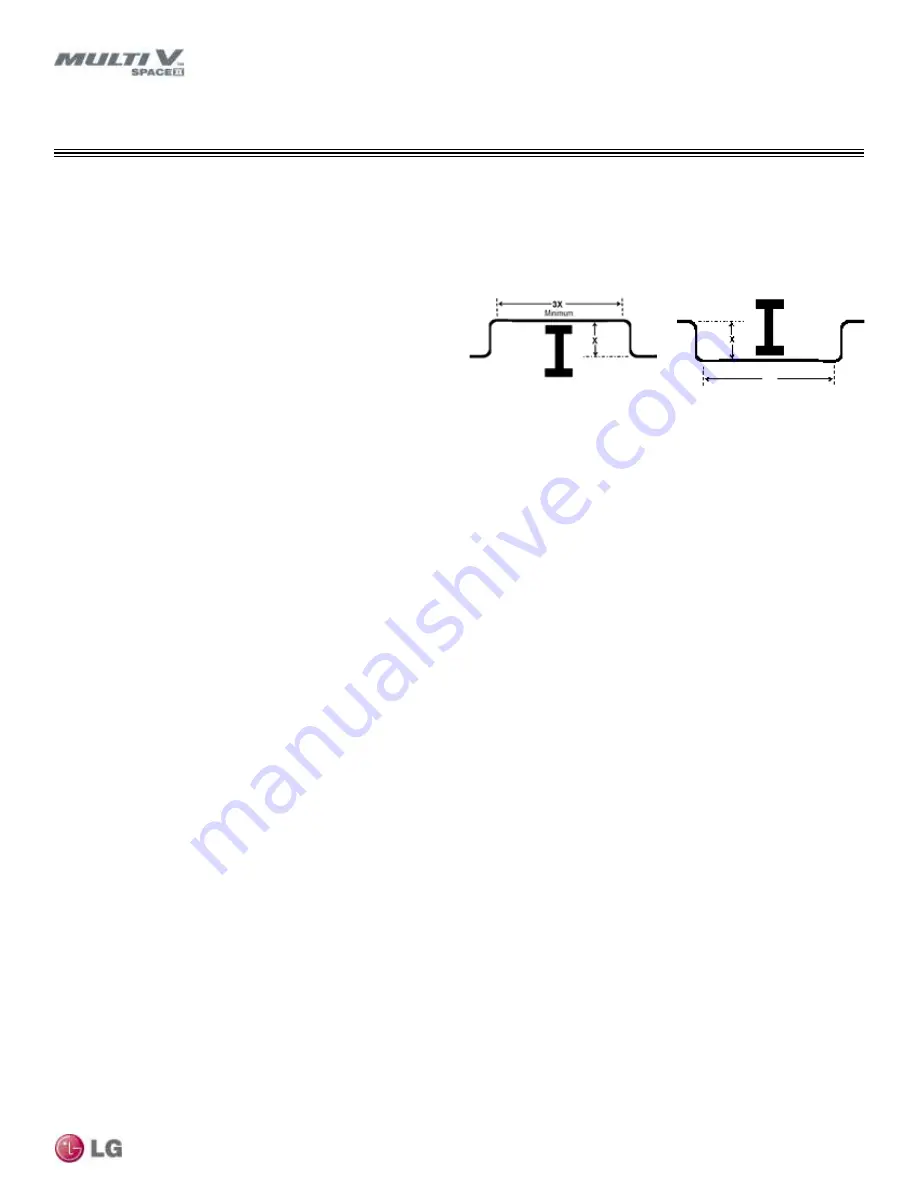
21
General Installation Guidelines
Due to our policy of continuous product innovation, some specifications may change without notification.
©LG Electronics U.S.A., Inc., Englewood Cliffs, NJ. All rights reserved. “LG” is a registered trademark of LG Corp.
Figure 19: Installing Piping Above and Below an Obstacle.
Above an obstacle.
3X
Below an obstacle.
obstacles
When an obstacle, such as an I-beam or concrete T, is in the path
of the planned refrigerant pipe run, it is best practice to route the
pipe over the obstacle. If adequate space is not available to route
the insulated pipe over the obstacle, then route the pipe under the
obstacle. In either case, it is imperative the length of the horizontal
section of pipe above or below the obstacle be a minimum of three
(3) times the longest vertical rise (or fall) at either end of the
segment.
no Pipe size substitutions
Use only the pipe size selected by the LATS Multi V pipe system design software. Using a different size is prohibited and may result in a
system malfunction or failure to work at all.
Under normal operating conditions, the vapor pipe temperature of a
Multi V Space II system can vary as much as 280°F. With this large
variance in pipe temperature, the designer must consider pipe
expansion and contraction to avoid pipe and fitting fatigue failures.
Refrigerant pipe along with the insulation jacket form a cohesive
unit that expands and contracts together. During system operation,
thermal heat transfer occurs between the pipe and the surrounding
insulation.
If the pipe is mounted in free air space, no natural restriction to
movement is present if mounting clamps are properly spaced and
installed. When the refrigerant pipe is mounted underground in a
utility duct stacked among other pipes, natural restriction to linear
movement is present. In extreme cases, the restrictive force of
surface friction between insulating jackets could become so great
that natural expansion ceases and the pipe is “fixed” in place. In this
situation, opposing force caused by change in refrigerant fluid/vapor
temperature can lead to pipe/fitting stress failure.
The refrigerant pipe support system must be engineered to allow
free expansion to occur. When a segment of pipe is mounted
between two fixed points, provisions must be provided to allow pipe
expansion to naturally occur. The most common method is the
inclusion of expansion Loop or U-bends. See Figure 20 on page 23.
Each segment of pipe has a natural fixed point where no
movement occurs. This fixed point is located at the center point
of the segment assuming the entire pipe is insulated in a similar
fashion. The natural fixed point of the pipe segment is typically
where the expansion Loop or U-bend should be. Linear pipe
expansion can be calculated using the following formula:
1. From Table 10, find the row corresponding with the actual length
of the straight pipe segment.
2. Estimate the minimum and maximum temperature of the pipe.
In the column showing the minimum pipe temperature, look up the
anticipated expansion distance. Do the same for the maximum
pipe temperature.
3. Calculate the difference in the two expansion distance values.
The result will be the anticipated change in pipe length.
General Example:
A Multi V Space II system is installed and the design shows that
there is a 120 feet straight segment of tubing between a Y-branch
and an indoor unit. In heating, this pipe transports hot gas vapor to
the indoor units at 120°F. In cooling, the same tube is a suction line
returning refrigerant vapor to the outdoor unit at 40°F. Look up the
copper tubing expansion at each temperature and calculate the
difference.
Vapor Line
Transporting Hot Vapor: 120 ft. pipe at 120°F = 1.68 in.
Transporting Suction Vapor: 120 ft. pipe at 40°F = 0.48 in.
Anticipated Change in Length: 1.68 in. – 0.48 in. = 1.20 in.
Liquid Line
The liquid temperature remains relatively the same temperature; only
the direction of flow will reverse. Therefore, no significant change in
length of the liquid line is anticipated.
When creating an expansion joint, the joint height should be a
minimum of two times the joint width. Although different types of
expansion arrangements are available, the data for correctly sizing
an Expansion Loop is provided in Table 11. Use soft copper with
long radius bends on longer runs or long radius elbows for shorter
pipe segments. Using the anticipated linear expansion (LE) distance
calculated, look up the Expansion Loop or U-bend minimum design
dimensions. If other types of expansion joints are chosen, design
per ASTM B-88 Standards.
LE = C x L x (T
r
– T
a
) x 12
LE
=
Anticipated linear tubing expansion (in.)
C
=
Constant (For copper = 9.2 x 10
-6
in./in.°F)
L
=
Length of pipe (ft.)
T
R
=
Refrigerant pipe temperature (°F)
T
a
=
Ambient air temperature (°F)
12
=
Inches to feet conversion (12 in./ft.)
copper expansion and contraction
General InstallatIon GuIDelInes
Piping Materials and Handling
Содержание Multi V ARUN053GF2
Страница 1: ...Installation Manual Variable Refrigerant Flow Outdoor Unit 4 4 Tons ...
Страница 73: ......
Страница 74: ......