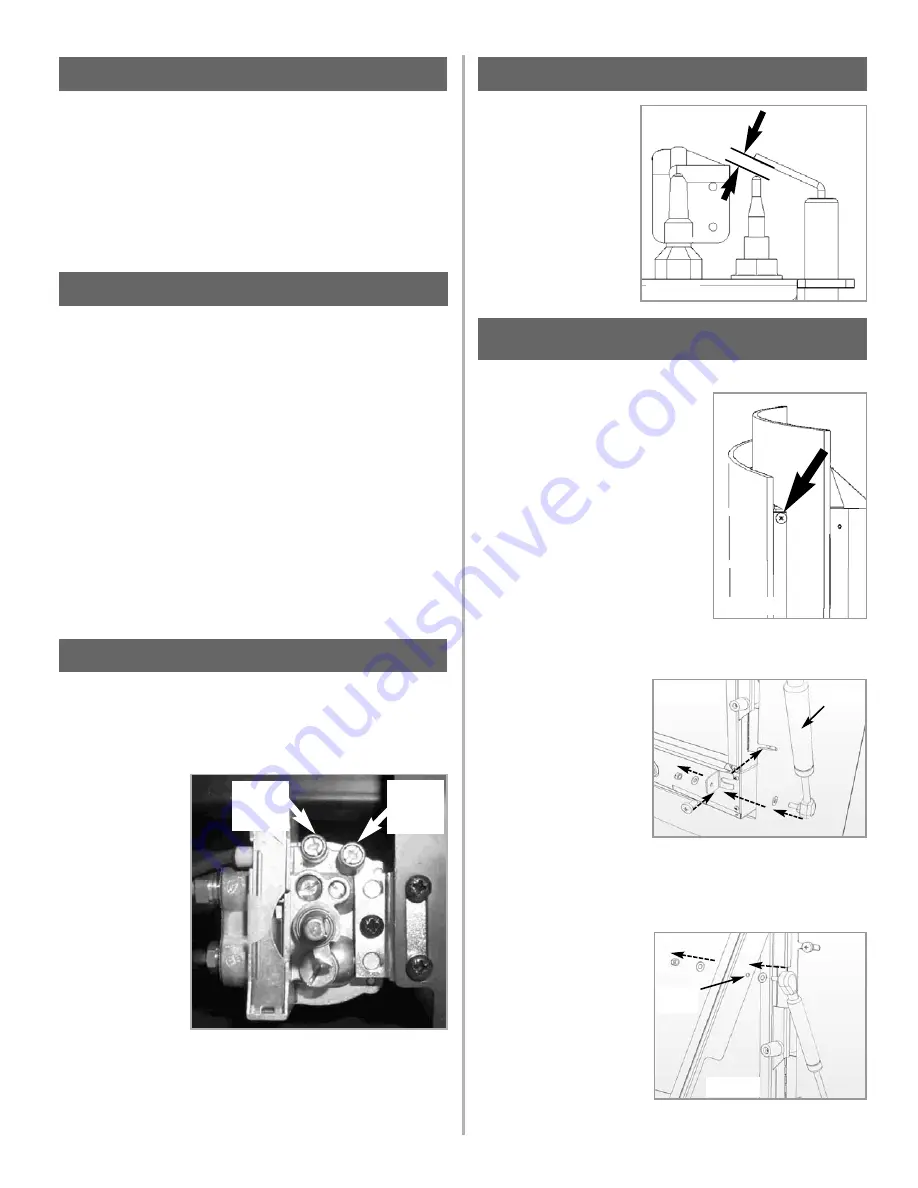
7
cavity when rigid pipe is used. Ensure that a sediment trap is installed
upstream of the heater (figure 4) within the structure’s piping system to
prevent moisture and contaminants from passing through the pipe to
the heater controls and burner. Failure to do so could prevent the heater
from operating reliably.
The heater gas inlet connection is 3/8” NPT at the regulator, located
below the burner, in the right hand side of the heater. When tightening
up the joint to the regulator hold the regulator securely with a wrench to
prevent the regulator from moving.
Turn on gas supply and test for gas leaks using a gas leak test solution
(also referred to as bubble leak solution).
NOTE: using a soapy water solution (50% dish soap, 50% water) is an
effective leak test solution, but it is not recommended, because the
soap residue that is left on the pipes/fittings can result in corrosion over
time.
A.
Light the appliance (refer to the lighting instructions label in the con-
trol compartment or on page 10).
B.
Brush all joints and connections with the gas leak test solution to
check for leaks. If bubbles are formed, or gas odor is detected, turn the
gas control knob (off/pilot/on) to the “OFF” position. Either tighten or
refasten the leaking connection, then retest as described above.
C.
When the gas lines are tested and leak free, be sure to rinse off the
leak testing solution.
D.
Observe the individual tongues of flame on the burner. Make sure all
ports are open and producing flame evenly across the burner. If any
ports are blocked, or partially blocked, clean out the ports.
The heater regulator controls the burner pressure which should be
checked at the pressure test points located on the control valve itself
(shown in figure 5) for burner (manifold) and regulator setting pressure.
The valve is found on the centre of the appliance behind the valve
cover. Remove the
cover plate by
unscrewing the four
retaining screws.
Release the test
point screws and
ensure operating
pressures are as
specified in section 3
“Appliance data” on
page 2 of these
instructions.The
pressure should be
checked with the gas
heater burning and
the control set to high flame.
The pressure regulator on manual models is preset and locked to avoid
tampering. If the pressure is not as specified in the Appliance Data sec-
tion on page 2, replace the regulator with P/N H6063. Replace the test
point screws after pressure measurement ensuring no gas leaks.
The gap between the
spark electrode and the
pilot should be 1/8” to
3/16” to produce a good
spark. There should be no
need to adjust this. If
under any circumstances
the piezo electric spark
fails, the pilot cannot be lit
manually.
The glass panel is supported by two
self-locking M6 screws, one on each
side of the fire. The glass panel must be
held in position while the screws are
inserted on each side - it is
recommended to seek assistance for
this operation. See figure 6a. The
screws should be screwed in fully and
then undone one turn to allow the glass
panel to swing open for access to the
controls.
The appliance features a piston damper
hinge assembly. The damper assembly
should be fitted onto the rear of the
glass facia, on the lower right hand side
as follows:
1) Ensure that the piston
portion of the damper is
positioned as shown in
figure 6b. Remove the
Philips screw securing the
frame, and fit the lower
piston bracket to the frame
and fully re-tighten the
screw.
Now fit the lower piston bolt
through the hole in the bracket, with the two nylon washers positioned
either side of the bracket. Finally, attach the “nyloc nut” to the damper
thread, tighten and then release one quarter turn. Check that the
assembly can swivel.
2) The damper top fixing is
shown in figure 6c. Locate
the fixing hole in the glass
window bracket. Place a
nylon washer each side of
the bracket, and affix the
damper bolt using the “nyloc
nut” provided. Tighten the
nut and release one quarter
turn. Finally check operation of damper from the fully open to fully
closed positions.
12.0 CHECKING THE GAS CONNECTIONS
13.0 GAS PRESSURE CHECK
Burner
(Manifold)
pressure
Regulator
pressure
setting
Figure 5
14.0 SPARK GAP
Figure 6
Spark gap
15.0 FITTING THE GLASS FACIA
11.0 CONNECTING A GAS LINE - continued
Damper
Fixing
hole
Figure 6a
Figure 6b
Figure 6c